Ken uw materialen:polyetheretherketon (PEEK)
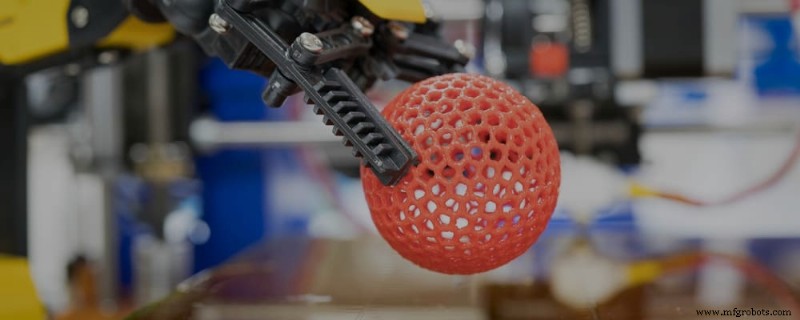
PEEK werd voor het eerst bedacht in 1978 - relatief recent volgens productienormen - als een materiaal dat bestand is tegen hoge temperaturen voor kabelisolatie. In de afgelopen 50 jaar heeft PEEK zich ontwikkeld tot een van de meest gebruikte materialen voor hoogwaardige toepassingen.
PEEK is zelfs een van de meest geproduceerde polyaryletherketonen (of PAEK's) voor grootschalige productieruns. Om het meeste uit dit veelzijdige en aanpasbare materiaal te halen, moeten ingenieurs en productteams zich vertrouwd maken met de eigenschappen, kenmerken en beperkingen van PEEK.
Wat is PEEK?
PEEK is een polymeer dat ontstaat door stap-groeipolymerisatie, waarbij de polymeerketen bij elke polymerisatiestap verdubbelt. Dit materiaal heeft een ongelooflijke elektrische weerstand, samen met hittebestendigheid, slijtvastheid en weerstand tegen vermoeidheid. PEEK is ook kruipvast, wat betekent dat het zijn vorm behoudt in ruwe omgevingen en hoge temperaturen, en bij mechanische belasting. PEEK is niet alleen robuust, maar ook lichtgewicht en gemakkelijk te vervaardigen.
Omdat PEEK fysiek licht is en toch zeer goed bestand is tegen bijtende stoffen, is het zeer geschikt voor een verscheidenheid aan productiemethoden. PEEK kan worden verwerkt met behulp van spuitgieten of additieve fabricage, waarbij het hoge smeltpunt snellere voedingen en snelheden mogelijk maakt. PEEK kan ook worden vervaardigd via CNC-bewerking. Bij alle productiemethoden biedt PEEK herhaalbaarheid en nauwkeurigheid van component tot component en kan het onderdelen produceren met nauwe toleranties.
Puur, ongevuld PEEK is op zich best duurzaam, maar PEEK wordt ook vaak versterkt met koolstof- of glasvezels om minder broos te worden. Met glas gevuld PEEK biedt meer stijfheid dan ongevuld PEEK en wordt vaak gebruikt in de olie- en gasindustrie om slechte reacties op stoom, chemicaliën en hoge temperaturen af te weren.
Een nadeel van met glas gevuld PEEK is de neiging om bijpassende onderdelen te verslijten. Met koolstof gevulde PEEK heeft een verhoogde druksterkte, wat de uitzettingssnelheid drastisch verlaagt en betere slijtvastheid en belastingdragende eigenschappen ondersteunt. Met koolstof gevulde PEEK heeft ook meer thermische geleidbaarheid, waardoor de levensduur en prestaties van een onderdeel toenemen.
Eigenschappen en mechanische specificaties van PEEK
PEEK is ontwikkeld als een zeer hittebestendige kunststof en smelt alleen bij extreem hoge temperatuur. PEEK stoot ook zeer lage rook- en giftige gassen uit bij blootstelling aan vuur, waardoor de gevaren in de buurt van vlammen of extreme hitte worden verminderd. Dit maakt PEEK een uitstekende keuze voor productiemethoden die verhitting en smelten vereisen, zoals spuitgieten.
Enkele andere mechanische specificaties voor pure, ongevulde PEEK zijn:
- Treksterkte :14.000 psi
- Trekmodulus :590.000 psi
- Wateropname :0,50% over 24 uur
- Smeltpunt :van 343°C (bijna 650°F)
- UL 94 V-0 ontvlambaarheidsclassificatie :(0.059″ dikte)
PEEK is ook zeer chemisch bestendig en slijtvast en kan zijn vorm behouden tijdens continue blootstelling aan heet water of stoom. PEEK is ook biologisch afbreekbaar en kan extreme natuurlijke omstandigheden overleven, zoals intense omgevingen en temperaturen.
Belangrijkste overwegingen voor productie met PEEK
PEEK is een zeer aanpasbaar materiaal, maar er zijn een paar technische overwegingen waarmee u rekening moet houden om de beste resultaten te garanderen. Hoewel PEEK bijvoorbeeld zeer hittebestendig is, voert het de warmte niet goed af en moet het tijdens het bewerken worden gekoeld om breuk of vervorming te voorkomen. Dit kan worden bereikt door standaard vloeibare koelmiddelen te gebruiken, maar dit kan de biocompatibiliteit beïnvloeden. In gevallen waar PEEK-producten direct menselijk contact vereisen, is perslucht het betere alternatief voor het koelen van PEEK.
Een maltemperatuur van 160°C tot 190°C (320°F tot 374°F) wordt aanbevolen bij het gebruik van PEEK, omdat dit kromtrekken helpt te minimaliseren en optimale kristallisatie oplevert. Bij gebruik van PEEK voor additive manufacturing moet de temperatuur van de printmondstukken 360°C tot 400°C (680°F tot 752°F) zijn met een verwarmd bed van 120°C (248°F).
Andere overwegingen zijn:
- Lagere rek :Aangezien PEEK een lagere rek heeft dan andere kunststoffen, kan het barsten als u er diep in boort. Speciale behandeling is vaak vereist om hittescheuren en andere interne spanningsschade te minimaliseren.
- Gevoeligheid voor kraken :Gloeien is ook vereist bij gebruik van PEEK. Dit proces helpt de kans op oppervlaktescheuren en vervorming te verminderen, waar PEEK vatbaar voor is tijdens het bewerken. Afhankelijk van hoeveel PEEK er zal worden bewerkt, kunnen meerdere gloeifasen nodig zijn.
- Gereedschapskeuze :Vaak kunt u PEEK bewerken met snijgereedschappen van siliciumcarbide. Diamantgereedschap kan nodig zijn bij het gebruik van met koolstof gevulde PEEK of bij het bereiken van nauwe toleranties. Zorg er ook voor dat uw snijgereedschap niet eerder op metalen is gebruikt om besmetting te voorkomen.
Populaire PEEK-applicaties
Er zijn drie belangrijke industrieën die PEEK-componenten gebruiken:de industriële sector, de gezondheidszorg en de voedingsmiddelen- en drankenindustrie.
Industriële toepassingen
PEEK van industriële kwaliteit is inherent zuiver en ondersteunt een hoge mechanische en chemische stabiliteit. Dit minimaliseert vervuiling en maximaliseert de veiligheidsinspanningen voor chemische en energietoepassingen, evenals voor componenten in de auto-, ruimtevaart- en elektronica-industrie. PEEK kan zelfs beter presteren dan metalen, zoals roestvrij staal, als het gaat om industriële wielen en pompen.
Medische toepassingen
PEEK kan componenten maken voor de gezondheidszorg, zoals orthopedische apparaten en spinale fusie-apparaten. PEEK kan ook worden gebruikt voor tandheelkundige implantaten, healing caps en meer wanneer het wordt vervaardigd met biocompatibele methoden.
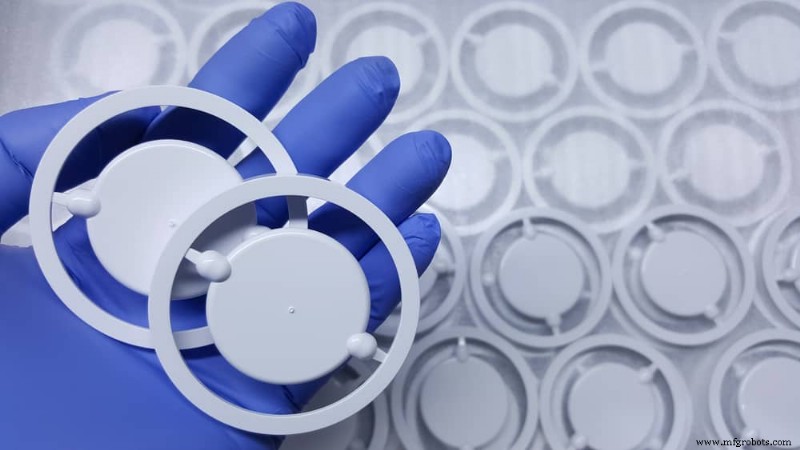
Eten en drinken toepassingen
PEEK is onlangs goedgekeurd door de Amerikaanse Food and Drug Administration (FDA) voor veilig menselijk contact, mits goed voorbereid. Nu vindt PEEK zijn weg naar de voedingsmiddelen- en drankenindustrie voor gebruik in componenten zoals kookgerei, drankdispensers en -mondstukken en verwerkingstoepassingen.
Waarom kiezen voor PEEK?
PEEK kan in de smelt worden verwerkt zonder bijtende gassen te creëren, waardoor het uiterst veilig en effectief is om te gebruiken bij spuitgieten en additieve fabricage. Het hoge smeltpunt van PEEK opent het ook voor CNC-bewerkingsmogelijkheden, omdat snel bewegende gereedschappen PEEK kunnen snijden zonder smelten te veroorzaken.
Het vervaardigen van PEEK met behulp van een van deze methoden resulteert in goede mechanische prestaties en consistentie tussen onderdelen. PEEK kan ook complexe ontwerpen en geometrieën ondersteunen met additive manufacturing - PEEK biedt zelfs een aanzienlijk hogere treksterkte en trekmodulus dan polyethersulfon (PES), een concurrent van primair materiaal.
PEEK is hittebestendiger dan PES en polyfenyleensulfide (PPS), een ander materiaalproductteams ruilen vaak voor PEEK. Terwijl PES kan worden gebruikt tot 220ºC en PPS continu kan worden gebruikt tot 250ºC, begint PEEK niet eens te smelten bij deze temperaturen. PEEK biedt een vergelijkbare water- en chemische bestendigheid als PPS, terwijl het beschikt over verbeterde temperatuurregeling, wat resulteert in totale prestaties bij toepassingen met hoge temperaturen.
Aan de slag met PEEK
PEEK is een relatief nieuw polymeer dat ongelooflijke hittebestendigheid, elektrische weerstand en corrosieweerstand biedt. Naast zijn duurzaamheid is PEEK lichtgewicht en ongelooflijk verwerkbaar, waardoor nauwkeurige en consistente productieruns mogelijk zijn, zelfs bij gebruik van nauwe toleranties. Productteams moeten hun eigen onderzoek doen om te bepalen of PEEK het juiste materiaal is voor een bepaald onderdeel, maar het nemen van deze beslissingen is veel eenvoudiger met de hulp van een vertrouwde fabrikant.
Bij Fast Radius zijn we toegewijd om u te helpen uw productiedoelen te bereiken. Ons deskundige productieteam heeft ervaring met een breed scala aan materiaalsoorten en productiemethoden. Als u denkt dat PEEK het juiste materiaal is voor uw aanstaande project, begeleiden we u door het hele productieproces, van materiaalkeuze tot lancering. Neem vandaag nog contact met ons op.
Neem een kijkje in het Fast Radius-bronnencentrum voor toegang tot meer Know Your Materials-pagina's, inclusief materiaalvergelijkingen.
Klaar om uw onderdelen te maken met Fast Radius?
Start uw offerteIndustriële technologie
- Ken uw materialen:flexibele hars
- Ken uw materialen:elastische hars
- Ken uw materialen:EPU
- Ken uw plastic materialen:PA 12 (Nylon 12)
- Ken uw materialen:MPU
- Ken uw materialen:CE 221
- Ken uw materialen:EPX 82
- Ken uw materialen:RPU 70
- Ken uw materialen:SIL 30
- Ken uw materialen:flexibel polyurethaan (FPU 50)
- Ken uw materialen:urethaanmethacrylaat (UMA)