Nieuwe technologie stimuleert groei van robotlassen
Is dit het juiste moment om uw laswerkzaamheden te automatiseren? Maakt u zich zorgen over hoe lang u uw ervaren lassers kunt behouden? Wilt u uw doorvoer verhogen, maar weet u niet hoe met het beschikbare personeel? Last van hardere materialen? Een verscheidenheid aan technische ontwikkelingen maken het relatief eenvoudig om deze problemen op te lossen door uw lasbewerkingen te automatiseren, met een verrassend snelle terugverdientijd.
Drie keer sneller
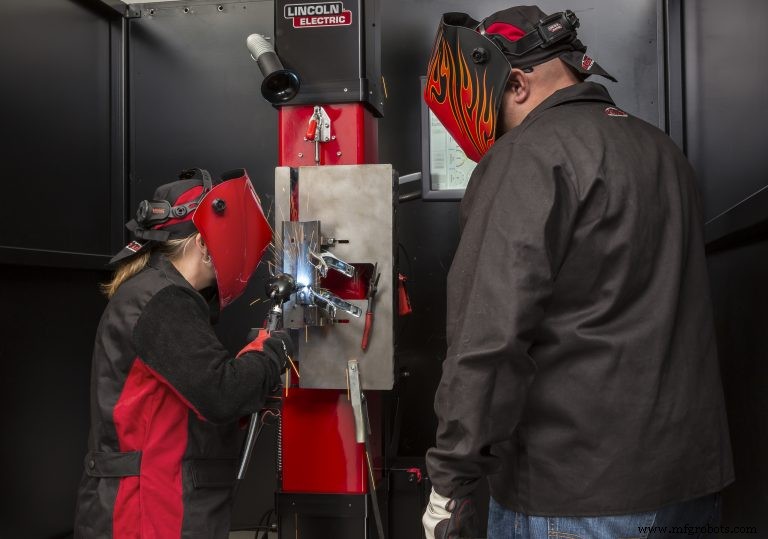
Er zijn twee brede categorieën van geautomatiseerd lassen, de zogenaamde "vaste" automatisering en "flexibele" (of robot) lassen. Vaste automatisering is vaak specifiek voor de toepassing en het is het beste als de onderdeelgeometrie en de las heel eenvoudig zijn. Het is bijvoorbeeld over het algemeen de beste oplossing voor het lassen van buizen. Maar voor de meeste industriële toepassingen en alles wat complex is, is robotlassen ideaal en daar gaat dit artikel over.
Zoals Jason Lange, manager inside sales, Lincoln Electric Co. (Cleveland) uitlegt:“Het belangrijkste doel van een robot is om te helpen bij de herhaalbaarheid van een las. Nummer twee is om het misbruik van de lasser te verminderen. De hele dag onderdelen verplaatsen en onder verschillende armaturen kruipen is een belasting voor een mens. Robots helpen de ergonomie.”
Het is dubbel zo belangrijk om het lassers gemakkelijker te maken, omdat ze steeds moeilijker te vinden zijn. "Er zijn veel technische scholen in het hele land die investeren in lasprogramma's om te proberen die kloof te overbruggen", vervolgde Lange. “Maar op een bepaalde dag overtreft het aantal mensen dat met pensioen gaat de inkomende vervangingen, waardoor er een leegte ontstaat. Robotlassen helpt die leegte op te vullen.”
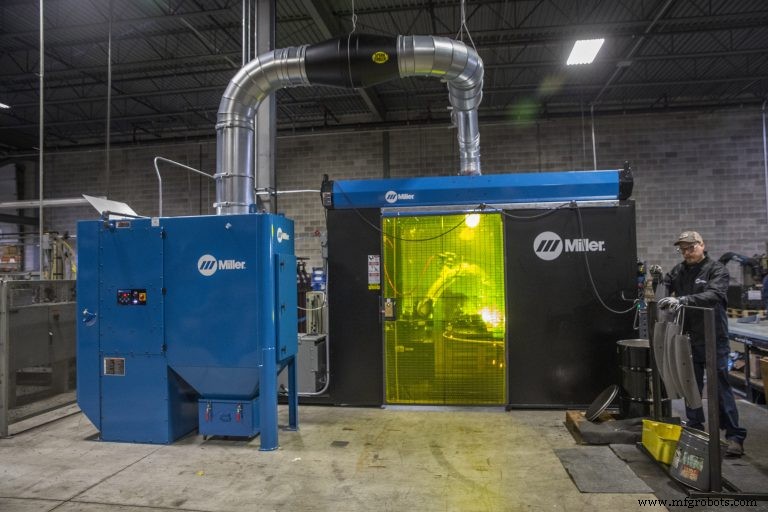
Tegelijkertijd "is de terugverdientijd van een robotsysteem doorgaans veel beter dan je zou denken", legt Erik Miller uit, business development manager laser group bij Miller Electric Mfg. Co. (Appleton, WI). “Eén robotsysteem maakt evenveel onderdelen als drie lassers. U bespaart twee salarissen per dienst en de gemiddelde kosten voor vooraf ontworpen cellen bedragen $ 100.000 tot $ 120.000. Het betaalt zichzelf terug in ongeveer een jaar. Als u een proces kunt automatiseren en in minder dan een jaar kunt terugverdienen, doet u dat meestal meteen. Als het twee jaar is, moet je het serieus overwegen."
Dus robotautomatisering is een enorme hulp bij het verhogen van de doorvoer. Maar bronnen die voor dit artikel werden geïnterviewd, benadrukten dat het geen vervanging is voor geschoolde arbeidskrachten. "Je hebt nog steeds een goede lasser nodig om die robot te laten werken", zoals Lange het uitdrukte.
Materialen veranderen Nog een reden om te automatiseren
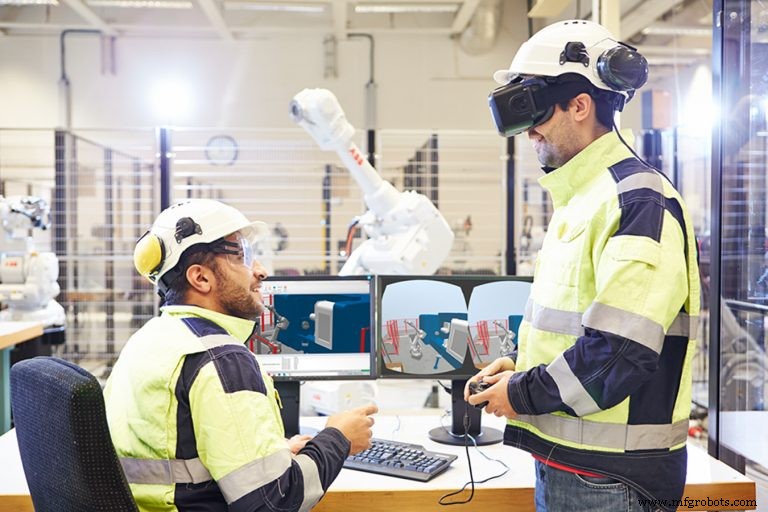
Veranderingen in werkmaterialen in de afgelopen tien jaar hebben geleid tot verbeteringen in het lassen, waarvan vele niet handmatig kunnen worden toegepast, zoals laserlassen, volgens Erwin DiMalanta, directeur, las- en snijbedrijf, ABB Robotics (Auburn Hills, MI) . "De fabrikanten van alles, van mijnbouwvoertuigen tot auto's, gebruiken verschillende materialen om de kosten en het gewicht te verlagen en om verschillende aandrijflijnoplossingen mogelijk te maken", zei hij. “Autofabrikanten zijn overgestapt op staal met meer hoge en ultrahoge sterkte, die metallurgische eigenschappen hebben waardoor ze sterker, lichter en corrosiebestendiger zijn, maar met een hoge vormbaarheid en lasbaarheid. Dat verandert de manier waarop metalen constructies worden ontworpen, gevormd en geassembleerd drastisch.” Terwijl fabrikanten misschien traditionele stansmessen hebben gebruikt om kenmerken in het onderdeel te snijden, gebruiken ze nu hot stamp-processen en geautomatiseerde lasertechnologieën om de onderdelen te vormen en te snijden.
“Een ander voorbeeld is de overstap naar aluminium voor meer toepassingen”, zegt DiMalanta. “Afhankelijk van de auto kan nu wel 90% van de carrosserie van aluminium zijn. Door de hogere geleidbaarheid heb je meer elektrische stroom nodig om aluminium te puntlassen en stroom staat synoniem voor warmte. Toch gaan we dunnere meetmaterialen gebruiken. In sommige voertuigen zijn de materialen ongeveer 1 mm dik. Dus hoe ga je om met deze trends die in tegengestelde richting gaan?”
Het antwoord is verbeterde technologie voor zowel elektronische als mechanische besturing van booglassen en een toenemend gebruik van laserlassen. Voor booglassen zei DiMalanta dat "stroombronnen nu extreem geavanceerd en elektronisch geregeld zijn. De afzetting van materiaal in een smeltbad wordt zorgvuldig gecontroleerd, met aangepaste golfvormen.” Miller voegde eraan toe dat dergelijke speciale golfvormen "de warmte-invoer op onderdelen regelen, wat vervorming kan verminderen en ook het cosmetische uiterlijk van lassen kan verbeteren."
Hij wees ook op een mechanische methode genaamd Active Wire van Panasonic. "Het is een bidirectionele draadaanvoer waarbij de draad naar voren wordt gevoerd om de kortsluiting te creëren en vervolgens achteruit uit de plas terugkeert, waarbij deze naaimachine-achtige actie wordt herhaald bij 120 Hertz. Dit vermindert de warmte-inbreng en vermindert ook aanzienlijk spatten. Het verbetert ook de consistentie van de boogaanval op elke las. Het is erg populair voor het lassen van aluminium en voor het lassen van dun plaatwerk.”
Hoe lichter het onderdeel, hoe geavanceerder de materialen moeten worden om complexe structuren mogelijk te maken met behoud van sterkte, zei DiMalanta. "Robots en hun geavanceerde softwaresystemen helpen de processen om deze materialen te verwerken te verbinden met het pad van de robot."
Laserlassen een aantrekkelijke optie
Met zijn bliksemsnelle vermogen om een grote verscheidenheid aan materialen (inclusief ongelijksoortige materialen) te lassen, is laser waarschijnlijk het grootste wat er in decennia is gebeurd met lassen. En zoals Masoud Harooni, senior ingenieur geavanceerde technologie - laserlassen bij Trumpf Inc. (Hoffman Estates, IL) het stelt:"Het grootste nieuws in laserlassen van de afgelopen jaren is de daling van de laserprijzen.
“Laserlassystemen zijn gemakkelijker te bedienen”, vervolgt Harooni. “Je selecteert één vermogen en één snelheid. Als het eenmaal is aangepast, verwerk je het hele onderdeel met weinig spatten. Bij booglassen moet je de boog behouden en de lasparameters zijn gevoelig voor eventuele veranderingen in de afstand tussen de toorts en het werkstuk. Verschillende delen van het [werkstuk] hebben meer of minder stroom nodig en dit zorgt voor minder processtabiliteit. Hoewel de feedbackloops op moderne booglassystemen erg goed zijn, zijn deze systemen nooit echt perfect afgesteld. Lasergelaste componenten vereisen veel minder nabewerking dan booggelaste componenten, die vaak moeten worden geslepen. Je hebt ook het probleem om met spatten om te gaan en het mondstuk in booglassystemen te moeten reinigen.”
Misschien nog belangrijker, laserlassen kan een diepere las bereiken zonder schade door hitte, zelfs in materialen zoals aluminium en magnesium die bij booglassen vatbaar zijn voor scheuren of porositeit. Harooni legde uit dat dit komt omdat laser een vermogensdichtheid van 108 watt per vierkante centimeter kan bereiken. Dit genereert een sleutelgat, een diep hol gebied dat ontstaat door het metaal van het werkstuk te verdampen. Terwijl de laserstraal langs het onderdeel beweegt, houdt het dit kleine sleutelgat omgeven door een gesmolten poel, terwijl het materiaal erachter stolt.
"Je krijgt een sterke, diepe las zonder extreme warmte-inbreng in het onderdeel", zei hij. “Booglassen heeft niet de vermogensdichtheid, dus de enige manier om een diepere las te bereiken, is door de warmte-inbreng te vergroten. De mechanische eigenschappen van gelaste onderdelen die minder warmte-invoer en minder vervorming hebben, zijn veel beter dan onderdelen met een hogere warmte-invoer."
Miller verklaarde dat "de eerste impact van laserlassen was bij het lassen van auto's, vanwege het hoge volume en de [technische voordelen]. Fabrikanten van plaatwerk zouden ook naar laserlassen moeten kijken. De echte voordelen zitten in het vervangen van weerstandspuntlassen, wat een uitdaging kan zijn voor middelgrote tot kleine productievolumes. Bevestiging kan moeilijk zijn, omdat toegang nodig is tot zowel de boven- als onderkant van het onderdeel, terwijl laserlassen alleen toegang aan de bovenzijde vereist, dus het is gemakkelijker te automatiseren. Je kunt ook een robot met een lager laadvermogen gebruiken voor laserlassen, samen met een eenvoudige vaste optiek.”
Vergeleken met een robot met een groot laadvermogen en een sterke arm die een groot gereedschap met twee elektroden draagt, kunnen fabrikanten nu een veiligere robot van acht kg gebruiken, er een proceskop op monteren en weerstandspuntlassen relatief eenvoudig automatiseren.
"Het andere gebied in plaatwerk waar laserlassen nuttig is, is de fabricage van dozen", zei hij. "Buitenhoeklassen die een cosmetisch uiterlijk vereisen en die achteraf weinig tot geen metaalafwerking vereisen, is een gebied waar we veel interesse in hebben gezien."
Volgens Miller biedt laser een goede oplossing op onderdelen waar de toegang beperkt is. Een laser heeft alleen een zichtlijn nodig om de las te maken, terwijl bij een booglastoepassing de robot een omvangrijke toorts in en rond onderdelen moet verplaatsen, wat erg moeilijk kan zijn. “Bij laserlassen zijn we vaak 500 mm verwijderd van het werkstuk. Het is alsof je met een straalpistool schiet. Laser heeft ook veel hogere verwerkingssnelheden en een lagere totale warmte-invoer in het onderdeel, waardoor vervorming wordt verminderd. Het is een perfect hulpmiddel voor autogeen lassen.”
Het nadeel van laserlassen, legt Harooni uit, is dat je "of ervoor moet zorgen dat er vrijwel geen opening tussen de componenten is, of dat je een smeltlijn moet gebruiken, die laserlassen combineert met draadondersteuning, waarbij je de draad in het zwembad smelt, zodat je de kloof kan overbruggen. Maar laserlassen gaat zo veel sneller dat het de extra investering in opspanning zeker waard is. Als je bijvoorbeeld 50 onderdelen per dag maakt met robotbooglassen, kan robotlaserlassen 300, 500 of zelfs duizenden van hetzelfde onderdeel per dag produceren."
Aan de slag met lasautomatisering
De sprong wagen in lasautomatisering is gemakkelijker dan ooit. Ten eerste bieden de belangrijkste spelers offline setup-software die de volgende taak op een pc met een hoge mate van realisme programmeert, dat programma overbrengt naar de robot en de las start. ABB gebruikt zelfs virtual reality-technieken om gebruikers in staat te stellen te 'samenwerken' met robotlasapparatuur.
"Je kunt de robot bij wijze van spreken letterlijk bij de nek nemen en hem sturen zoals je een hond aan de lijn zou doen", legt DiMalanta uit. "Dit kan veel intuïtiever zijn dan het gebruik van een leerhanger."
Ten tweede kunnen deze systemen mechanismen hebben die zich automatisch aanpassen aan positieveranderingen van het ene onderdeel naar het volgende en de laskwaliteit bewaken.
Zoals David Schaefer, productspecialist bij Miller Electric uitlegt:“Er zijn verschillende sensortypes die omgaan met veranderingen in de gezamenlijke locatie. De ene is gewoon aanraakdetectie en de andere is het volgen van de naad door de boog. Bij gebruik van aanraakdetectie kan de robot naar beneden komen en zijn booglasdraad gebruiken om het onderdeel te tasten. Het controleert de delta tussen de geprogrammeerde locatie en de werkelijke locatie om zichzelf in principe te herprogrammeren.
“Bij het volgen van naden door de boog, wanneer je over een verbinding weeft, zoals bij een hoeklas of een laplas als het materiaal dik genoeg is, detecteert het de verandering in stroomsterkte en bepaalt het wanneer het in de verbinding is en wanneer het uit de verbinding, en volgt dan die las terwijl hij aan het lassen is,” vervolgde Schaefer. "Je hebt ook de mogelijkheid om laseroptiek te gebruiken in plaats van draadtypedetectie, maar het is hetzelfde basisidee."
Lange van Lincoln Electric zei dat "een andere manier om dit te doen is door middel van een camera die een 2D- of 3D-foto van het onderdeel maakt. We kunnen programma's en verbindingen compenseren op basis van de fysieke locatie van de onderdelen. Nieuwere camera's worden niet zo beïnvloed door verblinding van een onderdeel als camera's een paar jaar geleden misschien waren. Ze kunnen meer kleur zien en de definities van een onderdeel lezen, waardoor schaduw en reflecties van het onderdeel kunnen worden onderscheiden.” Harooni voegde eraan toe dat "de optica van vandaag ons ook de mogelijkheid geeft om de kwaliteit van de las in realtime te controleren zonder destructieve tests."
Ten derde bieden de robots allemaal een vorm van botsingsdetectie. Miller van Miller Electric zei dat dit de belangrijkste verbetering in de robotarm zelf is. “Voorheen maakte een klant zijn programma op basis van de bekende X-Y-Z-positie van de toorts. Laten we zeggen dat de robot de helft van de dienst heeft gelast en dat de operator een klem open laat. De robot zou waarschijnlijk tegen de klem slaan en de toorts buigen. Dat zou ervoor zorgen dat elke las in dat programma niet goed uitgelijnd is omdat het uiteinde van de toorts is gebogen en die positie is veranderd. Als de robot tegenwoordig een object raakt, zelfs bij hoge snelheid, leest hij de resulterende stroompiek als een obstakel. Dit zorgt ervoor dat de robot onmiddellijk in de flex-servo-modus gaat, waardoor de rem wordt vertraagd voor een bepaalde afstand die voor elke as is gespecificeerd. De robot wordt in feite 'slap'. Hierdoor kan de robot het momentum verdrijven, waardoor schade aan het gereedschap wordt geminimaliseerd. Dit betekent dat je een botsing op hoge snelheid kunt hebben zonder de fakkel te buigen.”
Vier, alle grote spelers bieden voorgefabriceerde robotcellen met alles wat je nodig hebt op een pallet (of meerdere). "Een werkcel zou een volledig ontworpen eenheid zijn met alle beveiligingen", zei Lange. "Je ziet meestal hekken of stalen wanden, meestal veiligheidsscanners, lichten, drukknoppen om de robot te laten gaan, sleutelvergrendelingen en een soort positioneringsapparaat voor de robot, zoals een draaitafel of een reuzenrad. Deze apparaten brengen het onderdeel in de werkzone terwijl de operator extra onderdelen aan de andere kant laadt. Of je hebt gewoon een vaste tafel waar de robot gaat verwerken. Er zou ook een lasstroombron, de toorts en enkele ruimers zijn om de bits indien nodig schoon te maken. Je hoeft hem alleen maar op elektriciteit en een gasbron aan te sluiten.” En als een van de kant-en-klare oplossingen niet werkt, zijn er kant-en-klare oplossingen op maat beschikbaar.
Dus waar moet je je zorgen over maken?
"Als we een potentiële klant raadplegen over lasautomatisering, kijken we naar hun upstream-fabricage", legt Schaefer van Miller Electric uit. “Als ze lasers en CNC-apparatuur gebruiken om het materiaal te buigen, te remmen en te snijden, zullen ze veel meer succes hebben bij het robotlassen dan wanneer ze het met de hand snijden of een hakzaag gebruiken. Die winkels kunnen er nu mee wegkomen, want als ze de onderdelen met de hand lassen, kunnen de lassers dienovereenkomstig aanpassen, maar de robot niet.” Miller voegde eraan toe dat lassen meestal het laatste is dat geautomatiseerd wordt in een faciliteit, omdat stroomopwaartse processen eerst nauwkeurig moeten zijn. “Onderdelen moeten nauwkeurig worden gesneden en vervolgens nauwkeurig worden gebogen. Dan kun je ze lassen,' zei hij.
Naast de garantie dat onderdelen herhaalbaar zijn, is er ook een bevestiging nodig die de openingen beperkt of elimineert, zoals Schaefer uitlegde:"Je kunt geen lucht lassen. Een menselijke operator kan een opening zien en dienovereenkomstig reageren, in het algemeen door de uitsteking van de draad te vergroten om de stroomsterkte te verminderen, wat de warmte en de penetratie vermindert, en dan beginnen te weven om de opening te vullen. Een robot doet dit niet. Het zal doorbranden.”
Omgekeerd zei Lange dat sommige klanten in sommige gevallen duizenden of honderdduizenden dollars hebben uitgegeven aan gereedschappen om onderdelen vast te houden, terwijl ze die prijs konden halveren door stroomopwaartse processen te verbeteren. Dat zorgt voor de vereiste herhaalbaarheid stroomafwaarts, wat uiteindelijk de kosten van het gereedschap verlaagt en de hoeveelheid nabewerking en afval vermindert.
Na de kwaliteit en herhaalbaarheid van de onderdelen, is de volgende belangrijkste zorg "het kennen en begrijpen van het lasproces in relatie tot om zichzelf te lassen en door het geautomatiseerde apparaat te lassen,” zei Lange.
Dus wie moet je trainen om het geautomatiseerd lassen uit te voeren? Ofwel een ervaren lasser of iemand die graag wil leren lassen (wat weken duurt) plus lasautomatisering.
Schaefer waarschuwde:"Je hebt de juiste cultuur in de faciliteit nodig. Mensen met een baan kunnen zich bedreigd voelen door automatisering die de faciliteit binnenkomt. Ik zou heel duidelijk zijn tegenover mijn mensen over de voordelen, hoe het het bedrijf efficiënter zal maken, het zal helpen groeien en concurrerender zal zijn en uiteindelijk meer mensen zal aannemen."
Ten slotte moeten batchgroottes groot genoeg zijn voor automatisering. Zoals Lange het verwoordde:“De tijd die nodig is om offline te programmeren, de robot in te zetten en een snelle setup uit te voeren, levert zeker een goed rendement op als je batchgroottes ongeveer een dag of anderhalve dag lopen. Als je elk uur een onderdeel verandert, ben je misschien niet zo effectief in ROI.”
Automatisering Besturingssysteem
- Nieuwe draadloze technologie 2015
- NPE2018 Nieuwe technologiefocus:de '4.0'-revolutie
- Het nieuwe technologiecentrum voor gezondheidszorg van Hahn Automation
- Robotische automatiseringssystemen breken terrein op nieuwe faciliteit
- 4 manieren om de prestaties van robotlassen te verbeteren
- Leerlingen bouwen gerobotiseerd afvalsorteersysteem met B&R-technologie
- Acieta lanceert nieuwe laadcel voor robotmachines
- Robotiq lanceert nieuwe robotic bin picking-oplossing
- Best practices voor robotlassen
- AMRC stimuleert innovatie in technologie en circulaire economie
- Robotische doorbraak gemaakt door Manufacturing Technology Centre