Mark X-toepassing:Unibody 3D-geprinte drone
Als je ons recentelijk hebt gevolgd, heb je waarschijnlijk ons nieuwe favoriete Mark X-onderdeel gezien:een unibody, 3D-geprinte drone. Bedacht als een mogelijke demonstratie van de grootte, sterkte en oppervlakteafwerking van Mark X-onderdelen, heeft het in de praktijk de verwachtingen ver overtroffen. In dit bericht bespreken we hoe we het onderdeel hebben ontworpen voor afdruk- en vliegkwaliteit.
Vereisten voor drones
Bij het helemaal opnieuw ontwerpen van een onderdeel, is het belangrijk om eerst na te denken over de vereisten voor een succesvol onderdeel. Van onze kant hadden we vier centrale vereisten:
- Unibody :Om de grootte van de Mark X te laten zien, wilden we dat de hoofdstructuur van de drone één onderdeel zou zijn. Dit pronkt zowel met de grootte van de Mark X als met het elimineren van zwakke punten waar meerdere onderdelen op elkaar zouden aansluiten.
- IRIS+-hardware plaatsen :We hebben ervoor gekozen om de hardware, besturing en motoren van een IRIS+ Drone te gebruiken voor ons eindproduct. We hebben eerder een IRIS+-drone aangepast, dus het gebruik van deze hardware was een gemakkelijke keuze. Dit betekende dat alle kritieke componenten en bedrading van die drone gemakkelijk in het holle lichaam van het onderdeel moesten passen zonder het zwaartepunt te verstoren. Ten tweede moest de hardware gemakkelijk te verwijderen zijn, omdat we van plan waren verschillende prototypes te doorlopen.
- Afdrukken in Onyx zonder ondersteuning :Een unibody-drone is een tijdrovende print. Op zichzelf bevat de drone meer dan 220 kubieke centimeter Onyx. We wilden de printtijd beperken tot maximaal drie dagen, wat inhield dat we het gebruik van koolstofvezel moesten minimaliseren (of zelfs elimineren in sommige prototypes) en dat we de ondersteuning volledig moesten elimineren.
- Past op een Mark X-bouwplaat :Dit lijkt misschien eenvoudig, maar het betekende dat we creatief moesten zijn bij het plaatsen van de propeller. We zullen meer details geven over de plaatsing van de propeller in het volgende gedeelte.
Ontwerp en iteratie
Zelfs met duidelijk gedefinieerde vereisten is het vaak moeilijk om aan de slag te gaan met het ontwerpen van een onderdeel van deze omvang en complexiteit. We begonnen simpelweg met een top-down schets van de 3D-geprinte drone. Door de vier rekwisieten op hun locaties neer te leggen, konden we de schaal zien waaraan we werkten en de algemene lichaamsvorm schetsen. Hier kwamen we ons eerste probleem tegen:de propellers hadden een diameter van 245 mm en de bouwplaat is slechts 250 mm in de Y-richting. Rekening houdend met de extra 50 mm ruimte die we nodig hadden voor de motorsteunen, betekende dit dat de voorste en achterste propellers dezelfde ruimte innamen op de schets (zoals hieronder te zien is). Als dit problematisch klinkt, is dat omdat het zo is; het zou catastrofaal zijn om propellers tegen elkaar aan te laten botsen. Gelukkig was er een vrij eenvoudige oplossing:til de achterste twee steunen boven de paden van de voorste steunen zodat ze verschillende vlakken bezetten en allemaal vrij konden ronddraaien.
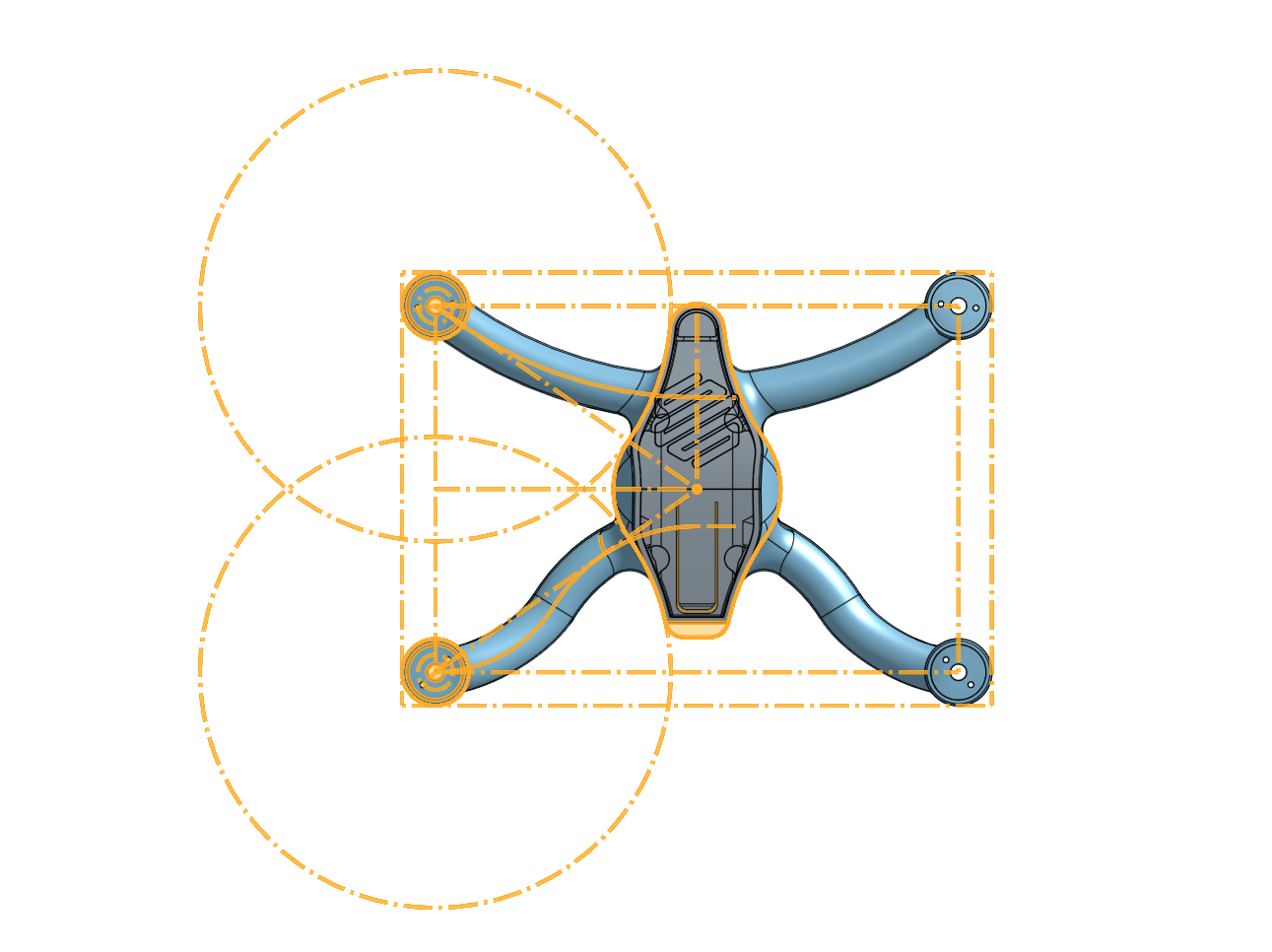
Nu we de algemene locatie en vorm voor alles hadden bepaald, was het tijd om in de details van het ontwerp te duiken. We gebruikten Onshape om elk stuk IRIS+-hardware te CAD-tekenen en gebruikten de modellen om de interne vorm van het hoofdgedeelte te bepalen. Elk stuk hardware kreeg op maat gemaakte interne bevestigingen, waardoor er ruimte was voor kabelgeleiding in het lichaam en de holle armen. Toen alles in de drone werd geplaatst, hebben we ervoor gezorgd dat het onderdeel goed zou afdrukken zonder ondersteuning. Dankzij het vermogen van Onyx om niet-ondersteund te printen op hellingen van 70 graden, hoefden we geen enkel aspect van het ontwerp ernstig in gevaar te brengen. Toen we ons bestand naar Eiger uploadden, waren we aangenaam verrast om te ontdekken dat het maar ongeveer twee dagen zou duren om af te drukken (in plaats van de gebudgetteerde drie). We waren klaar met het neerleggen van het onderdeel en lieten de machine zijn werk doen.
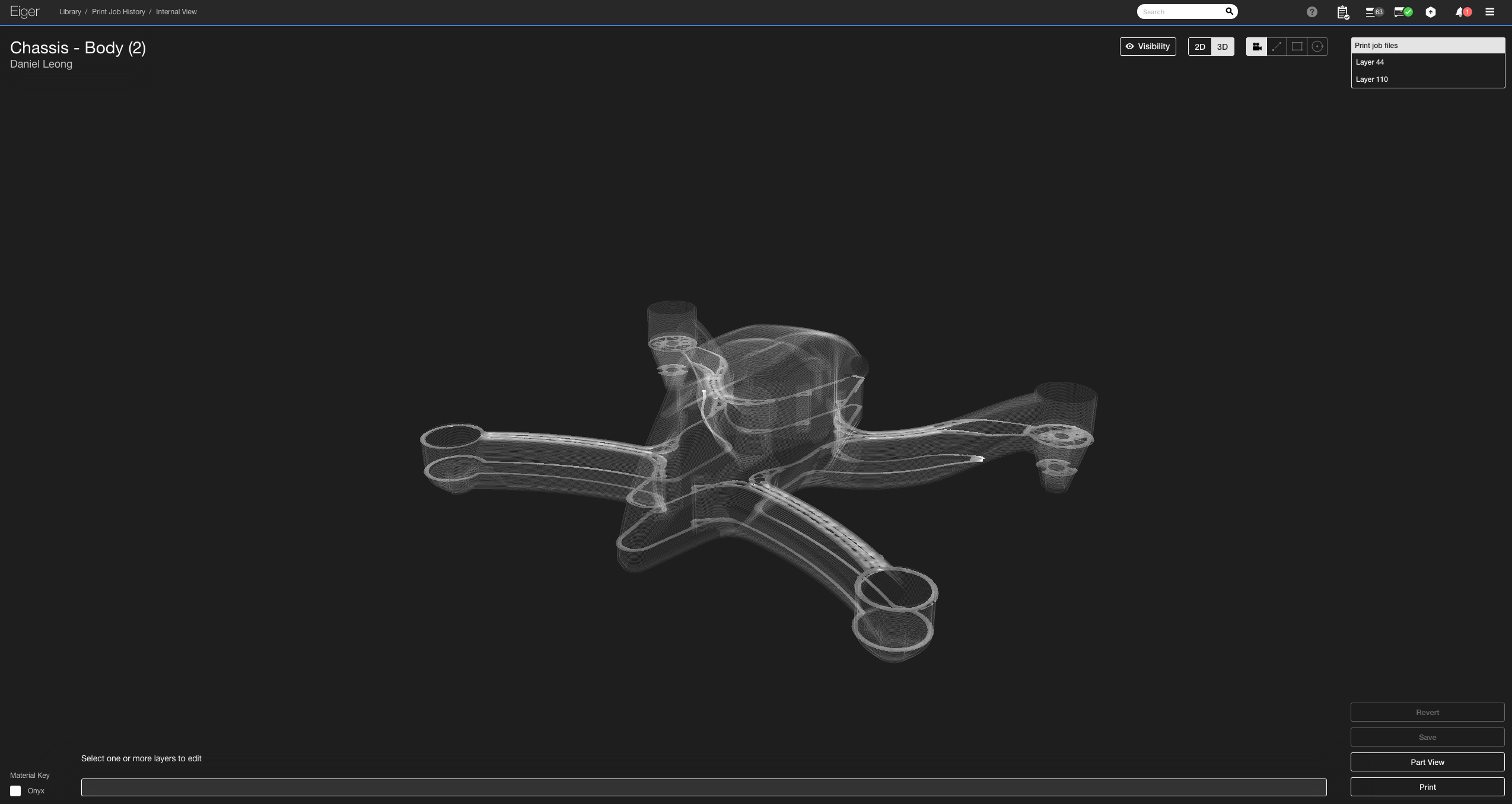
Hoewel die time-lapse en laser misschien een beknopt einde van het verhaal lijken, was het dat niet. De eerste drone werkte, maar paste niet helemaal goed. Dus gingen we door (en zijn we nog steeds) bezig met het herhalen van het ontwerp. We hebben vier unieke versies van de 3D-geprinte drone geproduceerd, elk een beetje beter dan de vorige. Dankzij het gemak en de snelheid van de Mark X is het herhaaldelijk prototypen van iets van deze omvang geen pijnlijk proces. We gaan door met het verbeteren van deze drone totdat we er helemaal tevreden mee zijn.
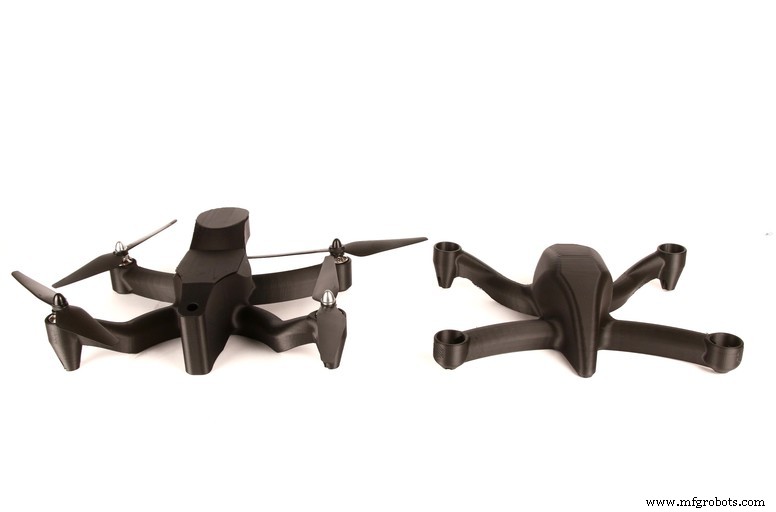
3D-geprinte drone-prestaties
Voor het grootste deel overtrof de 3D-geprinte drone onze verwachtingen. Elke iteratie vliegt iets anders dan de vorige, maar ze zijn allemaal vergelijkbaar in prestaties met de IRIS+. Al met al zijn we erg blij met de prestaties van de drone.
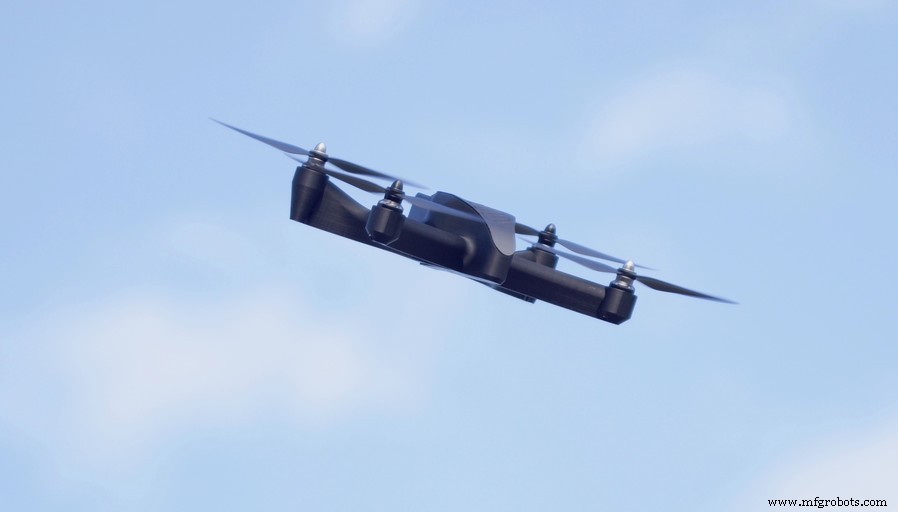
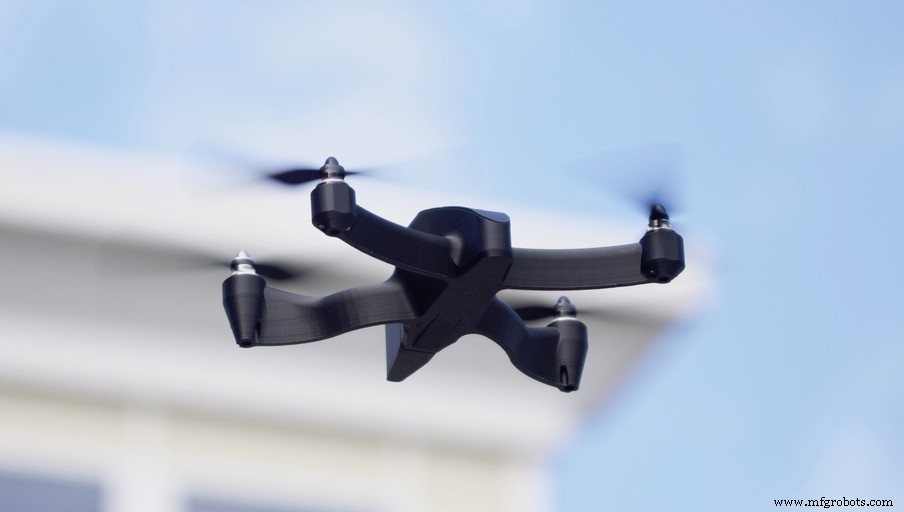
Opmerking:aangezien we nog steeds bezig zijn met het ontwerp, gaan we nog geen .stl-bestand van de drone vrijgeven. We delen het bestand wanneer het ontwerp klaar is. Volg ons op Facebook, Twitter, Instagram en Linkedin voor meer updates!
3d printen
- Applicatie Spotlight:3D-printen voor lagers
- Applicatie Spotlight:3D-printen voor schoenen
- Applicatie Spotlight:3D-geprinte brillen
- Applicatie Spotlight:3D-geprinte beugels
- Siamese tweelingen en 3D-geprinte chirurgische modellen
- 3D-geprinte extreme drones
- Aankomende evenementen — december 2015
- Use Case — 3D-geprinte sensorbehuizing
- Additive Episode One:3D Printed Robots
- Maatnauwkeurigheid van 3D-geprinte onderdelen
- Toepassing van bodemvultechnologie in printplaatassemblage