Beknopte handleiding voor het afdichten van FDM met Insight
Dus je bent geïnteresseerd in het kwalificeren van dat nieuwe productontwerp dat vloeistof vasthoudt maar bang is voor de vereiste nabewerking? Blijf kalm en inzicht.
Er lijkt een eindeloze hoeveelheid toepassingen te zijn naarmate de Additive Manufacturing (AM) -technologie evolueert. Desalniettemin blijven degenen die AM zoeken voor functionele prototyping en onderdelen voor eindgebruik de klus klaren met een 25 jaar oud werkpaard - Fused Deposition Modeling (FDM) -technologie. Maar liefst 85% van de markt is gebaseerd op FDM en dat is geen verrassing. Het produceert nauwkeurige en functionele onderdelen in een breed scala aan speciaal ontworpen productiekunststoffen.
Afgezien van al zijn voordelen, is FDM ook inherent poreus. Voor veel toepassingen speelt dit helemaal geen rol. Als je thermovormen doet, zou je deze fout omarmen. Als u echter een gas of vloeistof (in of uit) probeert vast te houden, is dit een flagrante beperking. Dus als porositeit een probleem is, is beginnen met Insight-verwerkingssoftware de beste manier om ervoor te zorgen dat uw aanvraag succesvol is.
Geometrie heeft grote invloed op welke techniek, of combinaties van technieken, nodig zijn om het onderdeel af te dichten voor testen en vervolgens voor het eindgebruik. Het gebruik van de Insight-software van Stratasys, meegeleverd met de Fortus-lijn van Stratasys, is een gemakkelijke manier om porositeitsproblemen op de meeste geometrieën op te lossen; omgekeerd kunnen sommige complexe geometrieën mogelijk een arbeidsintensieve nabewerking vereisen. Dus als je het zuinige type bent, moet je je best doen om STL's vooraf te verwerken met een Ultem-vuist om ervoor te zorgen dat die handmatige bewerkingen niet nodig zijn. En raad eens? In tegenstelling tot de meeste nabewerkingsmethoden, verandert deze strategie de onderdeelgeometrie niet.
Als u al bekend bent met FDM, weet u misschien waarom porositeit vaak nodig is. Zo niet, dan is dit de reden:het model kan delen hebben die niet zelfdragend zijn, dus de steunen moeten worden verwijderd en opgelost. De natuurlijke porositeit zorgt ervoor dat de oplosbare oplossing het dragermateriaal kan bereiken en kan wegvloeien uit diezelfde gebieden die mogelijk verborgen zijn. Met andere woorden, soms is uitloging nuttig. Houd dat in gedachten.
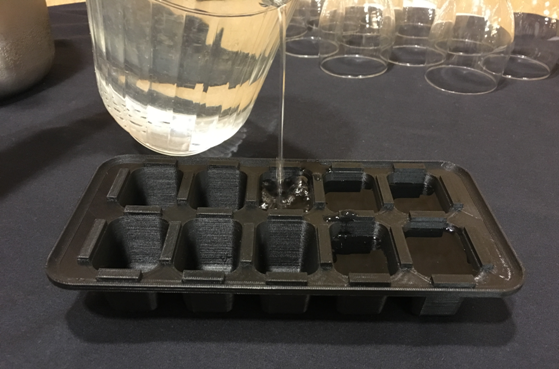
Verzegelen met inzicht
Met Insight heeft u de mogelijkheid om het probleem van porositeit te beheersen of zelfs te elimineren, vooral bij eenvoudige geometrieën. Dit is waar zolang de toepassingsvereisten zijn om een gas of vloeistof rond atmosferische druk te houden. Het zal niet zo effectief zijn bij hogere drukken/vacuüm, of bij complexe onderdeelgeometrieën.
De eerste stap is het aanpakken van de oriëntatie van de build op het platform. Dit vereist uw oordeel en de toepassingsbehoeften. De belangrijkste regel is om het onderdeel zo te oriënteren dat de meeste oppervlakken verticaal zijn georiënteerd.
Nadat je de optimale oriëntatie hebt bepaald, is de volgende stap het toevoegen van meerdere contouren aan de verticale wanden (onderste afbeelding). Deze techniek is in wezen gebaseerd op het gebruik van extra contouren en vermindert of verwijdert op zijn beurt rasters uit deze lagen. Het bestaan van rasters in een model verhoogt het risico op lekkage, vanwege de luchtspleten die ze creëren, zoals hieronder weergegeven (bovenste afbeelding).
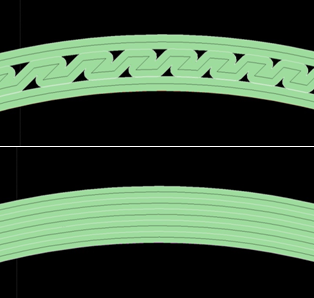
Via de werkbalk Groepen kunt u de parameters instellen om luchtspleten te verkleinen door deze stappen te volgen:
- Bepaal uw wanddikte door bij elke laag te meten en reken vervolgens uit, zodat de wanddikte gelijk is aan het aantal contouren vermenigvuldigd met de contourbreedte. U kunt een reeks lagen selecteren met dezelfde wanddikte.
- Stel Aangepaste groepen in voor elke dikte en voeg de lagen toe aan de groepen. Binnen elke groep kun je het aantal contouren en hun respectieve breedtes bepalen.
- Selecteer de Link Contouren functie en voeg waar mogelijk een lichte negatieve luchtspleet van contour tot contour toe. Deze functie creëert doorlopende gereedschapsbanen door start- en stoppunten tussen elke contour te elimineren.
In dit voorbeeld, weergegeven in de parameters voor een aangepaste groep, heb ik een wanddikte van 0,100. Ik heb vijf (5) contouren gebruikt met een contourbreedte van 0,020. Ik heb ook de Link Contour box gecontroleerd en gaf het een luchtspleet van -0,001. U kunt ook Contourbreedte . toepassen en Koppelingscontouren wereldwijd als het aan uw behoeften voldoet via de Toolpath Setup menu.
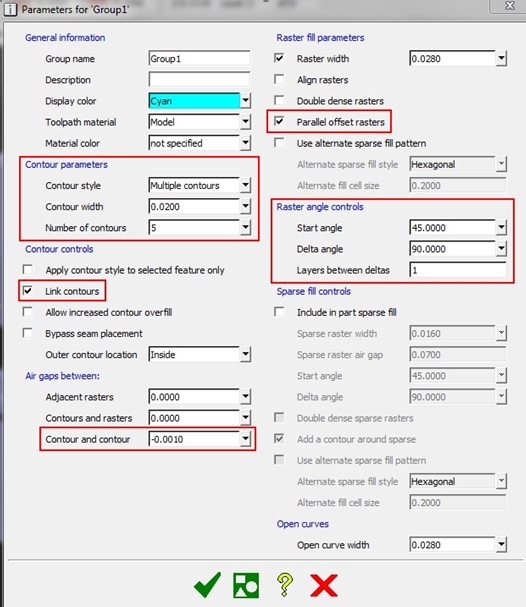
Opmerking: Het wijzigen van enkele van deze parameters kan uw bouwtijd en materiaalgebruik variëren. Het beste is om een "groene vlag" te gebruiken als controle en nota te nemen van de geschatte tijd en het materiaal voordat u parameters wijzigt.
Vervolgens zullen we naar rasters kijken, omdat je waarschijnlijk een aantal gebieden hebt die ze nodig hebben. Standaard zijn rasterhoekbesturingselementen ingesteld om te beginnen bij 45° en afgewisseld met 90° delta (zie hierboven). Deze afwisselende omslaggebieden laten paden of luchtgaten door de lagen, d.w.z. de zwarte driehoeken waar de rasters de binnenranden van de contouren raken.
Door Parallel Offset te selecteren Rasters, Insight zal drie parameters aanpassen.
- Varieert het aantal contouren op elke laag om de rasteromkeringen te verbergen. Dit is nog steeds van toepassing, zelfs als u al meerdere contouren heeft ingesteld.
- Plaats de rastergereedschapspaden parallel met aangrenzende lagen (0° delta).
- Verschuift de raster-toolpaths zodat ze de naden van de vorige lagen bedekken.
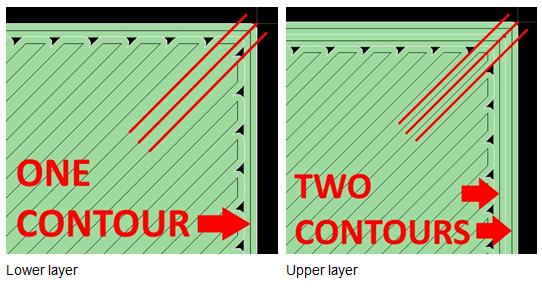
Dus dat bezegelt de deal ongeveer. Dit zou u een uitstekend startpunt moeten geven bij het verwerken van STL's ter voorbereiding op FDM-afdichtingstoepassingen.
Hier is een artikel over enkele andere nabewerkingstechnieken die afdichting naar een hoger niveau zullen tillen. Maar wees voorzichtig, want ze zullen je geometrie beïnvloeden.
Tags:FDM Technologie, Thermovormen, Ultem
3d printen
- Een gids voor 3D-printen met HP's Multi Jet Fusion
- Een korte handleiding voor 3D-printen met Binder Jetting
- Frezen – Een beknopte handleiding
- Java 8 - Beknopte handleiding
- Beknopte handleiding voor GD&T-parallellisme
- Een beknopte handleiding voor koude persmachines
- Een beknopte handleiding voor planetaire versnellingsbakken
- Een beknopte handleiding voor servopersmachines
- Een korte handleiding voor Gear Decoiler
- Een beknopte handleiding voor de CNC-draaibankas
- Een beknopte handleiding voor Power Chucks