10 van de grootste uitdagingen bij het opschalen van additieve productie voor productie in 2020 [Expert Roundup]
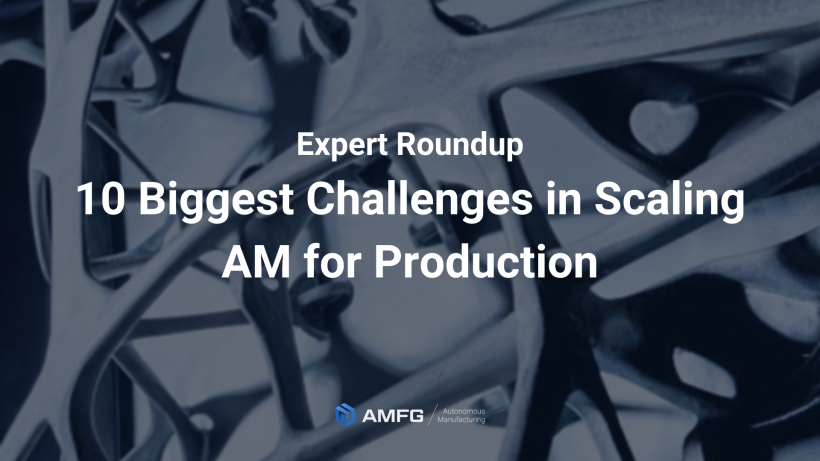
[Bijgewerkt in 2020]
Ontwerpflexibiliteit, materiaalefficiëntie en levensvatbare productie in kleine volumes zijn slechts enkele van de redenen waarom bedrijven zich steeds meer tot additive manufacturing (AM) hebben gewend. Maar om het meeste uit AM in productie te halen, moeten er nog enkele problemen worden aangepakt.
Hieronder bekijken we enkele van de meest urgente uitdagingen die de technologie moet overwinnen om de acceptatie ervan te versnellen:
Technologische uitdagingen
1. Lage productiesnelheden
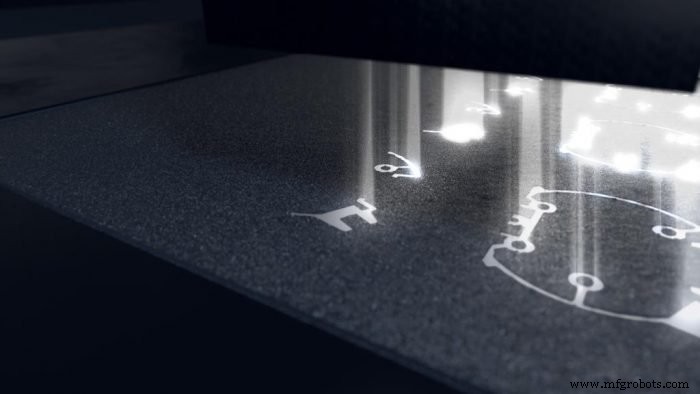
Niemand zal beweren dat snelheid belangrijk is, vooral niet als het doel is om op grote schaal te produceren. Veel huidige industriële 3D-printers lopen echter nog steeds achter op traditionele gemechaniseerde apparatuur in termen van snelheid en efficiëntie.
Dit is met name een obstakel voor adoptie in industrieën die worden aangedreven door massaproductie, zoals auto's en consumptiegoederen. In deze industrieën moeten producten in een zo kort mogelijk tijdsbestek worden vervaardigd en geleverd om de productie-efficiëntie te behouden.
“Het laatste onderdeel is de doorvoer of de snelheid van de machines. De productievolumes van [Automotive] verschillen aanzienlijk van de volumes in de lucht- en ruimtevaart of de medische sector. We moeten dus kijken naar systemen die onderdelen in minuten of seconden kunnen produceren in plaats van dagen en uren. Alles wat we kunnen doen om de technologie naar hogere bouwsnelheden te duwen, zal ons zeker ook helpen."
Harold Sears, technisch leider van additieve productietechnologieën bij Ford
High-speed AM is de afgelopen jaren een gebied van robuuste ontwikkeling en investeringen geweest.
De meeste fabrikanten van 3D-printers, die zich richten op productietoepassingen, zijn op zoek naar manieren om 3D-printen te maken sneller. Sommige hebben modulaire systemen ontwikkeld die de doorvoer kunnen helpen verhogen, terwijl anderen werken aan het verder verbeteren van de technologie achter hun bestaande machines.
De Duitse hardwarefabrikant EOS ontwikkelt bijvoorbeeld zijn Laser Pro Fusion-technologie, met als doel de doorvoer in Selective Laser Sintering (SLS)-technologie te vergroten. Terwijl de huidige SLS-systemen een of twee CO2-lasers gebruiken om polymeerpoeder samen te smelten, zal de nieuwe 3D-printer worden uitgerust met maximaal 1 miljoen diodelasers, wat de afdruktijd aanzienlijk zou kunnen versnellen.
Er zijn ook waren enkele opmerkelijke ontwikkelingen op het gebied van metaal 3D-printen. De Multilevel Concurrent Printing (MCP™)-technologie van Australian Aurora Labs is daar een voorbeeld van. Met dit poederbedfusieproces wil Aurora Labs 3D-printen van metaal met veel hogere snelheden mogelijk maken.
In tegenstelling tot traditionele poederbedtechnologieën, waarbij één laag tegelijk wordt geprint, print MCP meerdere lagen tegelijk in één doorgang. Op Formnext 2018 meldde het bedrijf dat het in staat was om ongeveer 30 lagen tegelijk te printen, met als doel dit in de komende 12 maanden te verhogen tot 100 lagen.
Onlangs heeft het bedrijf gemeld dat zijn PMP1 3D-printer een printsnelheid van 350 kg/dag kan halen. Aurora Labs zegt dat dit resultaat een snelheidsverbetering van 2000 procent aangeeft in vergelijking met de snelheid die vorig jaar werd gerapporteerd.
Het verhogen van de productiesnelheid is geen sinecure en vereist substantiële technologische innovatie. Vanaf 2019 bevinden de technologieën van zowel EOS als Aurora Labs zich nog in de ontwikkelingsfase, wat betekent dat het tijd zal kosten om hun beweringen over de productiesnelheid te bewijzen.
Dat gezegd hebbende, hebben we er alle vertrouwen in dat 3D-printen er uiteindelijk zal komen, naarmate de vooruitgang vordert.
2. Materiaalontwikkeling en inconsistenties in materiaaleigenschappen
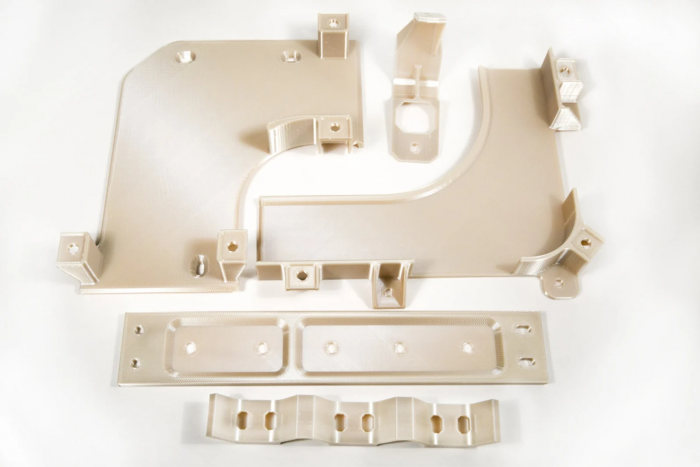
“De additive manufacturing-industrie heeft absoluut oplossingen nodig voor meer materialen. 3D-printen is theoretisch in staat om onderdelen met een hoge complexiteit en functionaliteit te produceren, of het nu mechanisch, biologisch of elektrisch is. Maar om dat voor elkaar te krijgen, moet je voldoende materiële mogelijkheden hebben.”
Simon Fried, mede-oprichter van Nano Dimension
De beschikbaarheid van geschikte materialen is een andere uitdaging voor de 3D-printindustrie. In vergelijking met traditionele productieprocessen, die tientallen jaren van materiaalontwikkeling hebben ondergaan, is de eigen materiaalontwikkeling van 3D-printen net begonnen.
In de beginjaren van 3D-printen, toen de focus van de industrie lag op prototyping, werd veel minder nadruk gelegd op materiaaleigenschappen. Nu de technologie echter verandert in een productieoplossing, is het materiaalontwikkelingsproces enorm versneld.
Een bijzonder opwindende trend is de vooruitgang in hoogwaardige 3D-printpolymeer- en composietmaterialen. Grote chemiebedrijven als Arkema, BASF en DuPont ontwikkelen met koolstof versterkte polymeren, die soms een sterkte bieden die vergelijkbaar is met die van metalen.
Een fabrikant van composiet 3D-printtechnologieën, Markforged, is ook bezig op dit gebied en heeft verschillende nieuwe materialen ontwikkeld. De meest recent geïntroduceerde is de Onyx FR, het eerste vlamvertragende composietmateriaal.
Aan de metaalkant duurt de materiaalontwikkeling langer, soms een paar jaar, maar de vooruitgang gaat ook door.
Hoewel de beschikbaarheid van materialen toeneemt, zijn er nog steeds veel inconsistenties in de eigenschappen van de 3D-printbare materialen. Momenteel heeft de industrie geen solide database van materialen met bewezen printparameters en gedefinieerde specificaties. Als gevolg hiervan wordt het een uitdaging om een consistent en herhaalbaar 3D-printproces te realiseren.
Dit betekent dat de meeste fabrikanten terughoudend zullen blijven om de technologie te gebruiken, totdat ze ervoor kunnen zorgen dat de materiaaleigenschappen voldoen aan de vooraf gedefinieerde en geaccepteerde normen en standaarden van de industrie.
De enige weg vooruit is de ontwikkeling van een AM-materiaaldatabase met informatie over mechanische en thermische eigenschappen en specificaties voor succesvol printen.
De 3D-printindustrie werkt aan het bereiken van dit doel. Organisaties die normen ontwikkelen, zoals ISO en ASTM, hebben een aantal specificaties uitgegeven voor metaalpoeders zoals nikkel, titanium en roestvrij staal.
Tegelijkertijd bouwen andere instanties een database met materialen en procesinformatie voor AM op. Zo heeft America Makes in samenwerking met Stratasys en het National Institute for Aviation Research (NIAR) eerder dit jaar een database met materiaaleigenschappen vrijgegeven voor ULTEM™ 9085 Type I die wordt gebruikt in Fused Deposition Modeling (FDM).
Het opzetten van een dergelijke database zal het gebruik van het gecertificeerde polymeermateriaal voor vliegtuiginterieurcomponenten helpen bevorderen.
Uiteindelijk zullen ontwikkelingen zoals deze de sleutel zijn om ervoor te zorgen dat AM-materialen kunnen voldoen aan de verwachtingen van fabrikanten op het gebied van prestaties en betrouwbaarheid.
3. Handmatige nabewerking
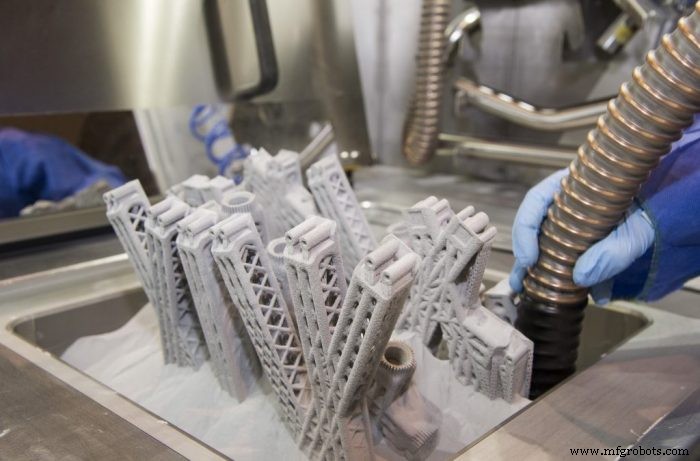
De realiteit van 3D-printen is dat vrijwel alle onderdelen die uit een 3D-printer komen, enige vorm van nabewerking vereisen om de mechanische eigenschappen, nauwkeurigheid en esthetiek van een onderdeel te verbeteren.
Dit is geen groot probleem bij het gebruik van 3D-printen voor prototyping. Nu de technologie echter overgaat naar een fabricageproces aan het einde van een onderdeel, is schaalvergroting en automatisering, nabewerking, een van de belangrijkste knelpunten geworden bij het opzetten van AM-productielijnen.
“Bij metal AM zijn veel stappen nodig om de kwaliteit te waarborgen. Dit omvat het op de juiste manier verwijderen van het poeder en het doorlopen van een spanningsontlastende verwarmingscyclus, zodat de onderdelen niet kromtrekken en vervormen door de restwarmte die in de onderdelen is opgebouwd wanneer ze van de bouwplaat worden verwijderd.
Vaak is er veel tijd nodig om de draagconstructies weg te snijden en weg te slijpen. Andere stappen zijn onder meer CNC-bewerking en ander afwerkingswerk, evenals heet isostatisch persen, wat ervoor zorgt dat het onderdeel geen porositeit bevat.”
Terry Wohlers, oprichter en voorzitter van Wohlers Associates
De meeste nabewerkingen die Terry Wohlers hierboven beschrijft, zijn nog steeds zwaar handmatige processen, waarbij bekwame operators belangrijke taken moeten uitvoeren.
Het kan kosteneffectief zijn om menselijke arbeid te gebruiken om een prototype of zelfs een paar dozijn onderdelen af te werken. Bij het produceren van honderden of zelfs duizenden 3D-geprinte onderdelen wordt de behoefte aan nabewerkingsautomatisering echter extreem acuut.
"Geautomatiseerde oplossingen zullen een van de grootste problemen op dit moment oplossen, namelijk een verhoogde doorvoer met consistente output van de post-printfunctie."
Jeff Mize, CEO van PostProcess Technologies
Momenteel zijn er slechts een paar AM-specifieke oplossingen die helpen bij het automatiseren van nabewerkingen, zoals de reinigingsmachines van DyeMansion, de oplossingen voor het gladmaken van oppervlakken van AMT en de ondersteuningssystemen voor verwijdering en oppervlakteafwerking van PostProcess Technologies. Toegegeven, deze systemen zijn in de eerste plaats ontworpen voor 3D-geprinte polymeeronderdelen.
Als het gaat om 3D-printen van metaal, worden momenteel nabewerkingstechnologieën, die worden gebruikt voor traditioneel vervaardigde onderdelen, aangepast voor 3D-geprinte componenten.
Om deze technologieën verder te automatiseren, beginnen bedrijven nu ook robotoplossingen te implementeren om bewerkingen zoals materiaalwisselingen en onderdeelhandling te elimineren. Zo lanceerde 3D-printerfabrikant Digital Metal vorig jaar een volledig geautomatiseerd productieconcept.
Volgens dit concept zal een robot de meeste processtappen uitvoeren, zoals het voeden van de printer met bouwdozen en deze vervolgens verwijderen voor nabewerking. Het doel is om al het handmatige werk te elimineren om een continue productie van grote volumes mogelijk te maken.
Hoewel dergelijke ontwikkelingen bemoedigend zijn, is het innovatietempo op dit gebied traag. Het aantal geavanceerde nabewerkingsoplossingen zal echter zeker toenemen om de steeds groter wordende AM-productievolumes te evenaren.
Software-uitdagingen
4. Beperkte mogelijkheden bij het voorbereiden en ontwerpen van gegevens
"Ontwerp en gegevensvoorbereiding vormen nog steeds een knelpunt in deze branche, terwijl de nadruk wordt gelegd op hardwaresystemen met een hogere productiviteit, waarbij intelligente softwareoplossingen buiten deze vergelijking vallen."
Yves Hagedorn, algemeen directeur bij Aconity3D
Hoewel het lijkt alsof 3D-printen zo simpel is als het indrukken van een knop, is dat in de verste verte niet het geval. Om te beginnen vereist industrieel 3D-printen een aanzienlijke ontwerpvoorbereiding om een model printklaar te maken.
Het ontwerpproces wordt bemoeilijkt door het feit dat Computer-Aided Design (CAD) en Computer-Aided Engineering-software lange tijd grotendeels niet is geoptimaliseerd voor de vereisten van 3D-printen.
Het kan bijvoorbeeld moeilijk zijn om traditionele CAD-software te gebruiken om componenten te ontwerpen die gemaakt zijn met gegradeerde materialen, om roosterstructuren te creëren of porositeit te modelleren.
Bovendien omvat de AM-ontwerpworkflow meerdere stappen, die vaak vastlopen door de noodzaak om aparte softwareoplossingen te gebruiken.
“We horen van veel van onze klanten dat ze met zeer onsamenhangende workflows werken. Ze doen het ontwerpproces in een CAD-tool, vertalen dat vervolgens naar een STL-bestand en importeren het in een buildprocessor, zoals Netfabb. Van daaruit wordt het naar de machine gestuurd en de machine verzamelt daarover gegevens. Dus je eindigt met deze silo's met gegevens die niet goed met elkaar zijn verbonden."
Robert Yancey, Director of Manufacturing and Production Industry Strategy and Business Development bij Autodesk
In een typisch scenario zou een ontwerper bijvoorbeeld een solide model in zijn CAD-systeem maken en dit vervolgens omzetten in een driehoekig model om bedrukbaarheidscontroles uit te voeren, de structuur te optimaliseren om het gewicht te verminderen, ondersteuningen toe te voegen en simulatieanalyse uitvoeren. Voor al deze stappen zijn verschillende programma's, verschillende softwareomgevingen en meerdere bestandsindelingen nodig.
Stel je dan voor dat je een simulatie uitvoert en de resultaten wijzen op een bouwfout, waardoor je de oriëntatie van het onderdeel of de ondersteunende structuren moet wijzigen om dit te voorkomen. Als gevolg hiervan moet u alle stappen en programma's opnieuw doorlopen om enkele parameters te wijzigen en het model afdrukbaar te maken.
Deze noodzaak om AM-ontwerpgegevens via meerdere softwareoplossingen over te dragen, resulteert in een tijdrovend en foutgevoelig ontwerpproces.
De industrie probeert op meerdere manieren de last van de voorbereiding van 3D-modellen te verlichten. Softwarebedrijven, zoals PTC, Autodesk en Dassault Systèmes, voegen bijvoorbeeld specifieke 3D-printfunctionaliteit toe aan hun CAD-programma's.
PTC biedt bijvoorbeeld zijn Creo 6.0-software aan om ontwerp en drukvoorbereiding in één omgeving mogelijk te maken. Eind 2018 nam PTC het generatieve ontwerpsoftwarebedrijf Frustum over. Het bedrijf werkt nu aan het toevoegen van generatieve ontwerptechnologie, die vaak wordt gecombineerd met 3D-printen, aan zijn CAD-platform.
Tegelijkertijd ontwikkelen 3D-printerfabrikanten hun eigen softwareoplossingen om de voorbereiding van 3D-modellen te stroomlijnen. GrabCAD van Stratasys en 3DXpert van 3D Systems zijn slechts twee voorbeelden van de software die is ontwikkeld om de noodzaak van meerdere gegevensoverdracht en conversies te elimineren of te minimaliseren.
Hoewel er grote vooruitgang wordt geboekt op het gebied van AM-ontwerp en drukvoorbereiding, is er nog ruimte voor ontwikkeling. De ontwerpers de mogelijkheid bieden om 3D-modellen binnen de CAD-omgeving aan te passen en ze snel te herhalen zonder omslachtige gegevensconversie, zal de sleutel zijn om de uitdagingen op het gebied van ontwerpvoorbereiding tot het verleden te laten behoren.
Uitdagingen op het gebied van kwaliteitsborging
5. Variatie van deel tot deel
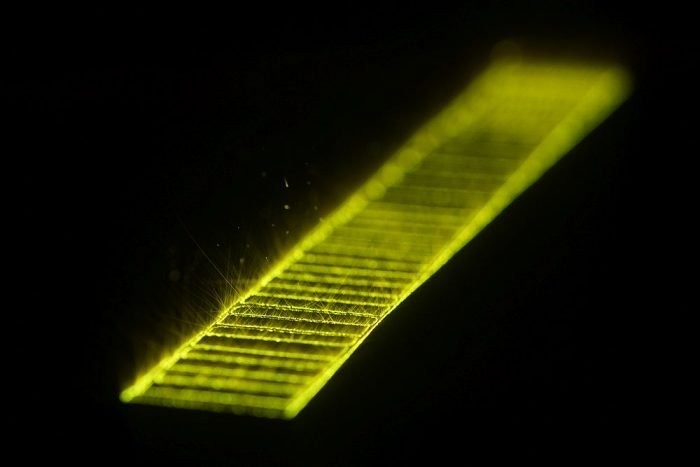
"Een ander belangrijk ding dat de industrie moet aanpakken om breder geaccepteerd te worden, is de variatie van deel tot deel [...] De reden daarvoor is dat de consistentie van het materiaal dat uit het systeem komt niet noodzakelijkerwijs is wat je wilt dat het is. Je moet ontwerpen voor het zwakste deel dat je zou kunnen krijgen, wat betekent dat je sommige van de mogelijkheden van AM niet volledig benut.”
Zachary Murphree, VP of Technology Partnerships bij VELO3D
Traditionele CNC-bewerking, spuitgieten of gieten zijn bekende fabricageprocessen. 3D-printen daarentegen biedt een nieuwe benadering van het vervaardigen van onderdelen. Naast nieuwe mogelijkheden heeft de technologie ook nieuwe gebreken die niet worden gezien in traditionele productie, wat kan leiden tot variaties in de kwaliteit van onderdelen van build tot build.
Dit is met name het geval bij 3D-printen van metaal. Enkele van de gebreken die uniek zijn voor metaal AM, kunnen bijvoorbeeld poeder zijn dat in een onderdeel zit, microscheuren en het ontbreken van fusie.
Een van de belangrijkste bronnen van variaties in de kwaliteit van onderdelen is de materiaalchemie. Veiligheidskritische toepassingen, zoals vliegtuigonderdelen of medische hulpmiddelen, vereisen dat een materiaal de juiste morfologie (deeltjesgrootte en vorm) heeft en 100% vrij is van verontreiniging.
Onzuiverheden, veroorzaakt door onjuiste opslag of behandeling, of twijfelachtige kwaliteit van de grondstof, kunnen de eigenschappen van het uiteindelijke onderdeel veranderen, wat op zijn beurt kan leiden tot een mislukte afdruk.
Het waarborgen van de kwaliteit van het materiaal vereist gestandaardiseerde testmethoden en hulpmiddelen, die de industrie grotendeels ontbreekt. Om deze problemen op te lossen, werken AM-gebruikers samen met vertrouwde testlaboratoria of, als ze over voldoende middelen beschikken, de nodige expertise in huis te ontwikkelen.
Een andere uitdaging die de variabiliteit van onderdelen beïnvloedt, is het gebrek aan geavanceerde procescontrole in 3D-printers. Om de variatie in onderdelen te minimaliseren, moeten 3D-printers overschakelen van een open-loop naar een closed-loop besturingssysteem.
Dit laatste verwijst naar het vermogen van een 3D-printsysteem om afwijkingen tijdens het printproces te detecteren en het systeem automatisch aan te passen om deze te compenseren. Dit wordt bereikt door sensoren en camera's in een 3D-printer in te bouwen, waardoor gebruikers de build in realtime kunnen volgen.
Door controle te houden over het bouwproces, via het gesloten-lusbesturingssysteem, kunnen fabrikanten consistente geometrieën, oppervlakteafwerkingen en materiaaleigenschappen bereiken die de kwaliteit ondersteunen.
"Ik denk dat dat de heilige graal voor AM is, want met controle tijdens het proces kun je vrijwel onmiddellijk reageren op tekortkomingen in je proces."
Yves Hagedorn, algemeen directeur bij Aconity3D
In-proces kwaliteitscontrole, mogelijk gemaakt door een gesloten-lussysteem, is echter nog relatief nieuw voor AM-technologieën en vormt een barrière voor fabrikanten om te implementeren. Vanaf 2019 is slechts een klein percentage van de 3D-printers die op de markt verkrijgbaar zijn uitgerust met closed-loop control units.
Dat gezegd hebbende, zal controle tijdens het proces een absolute noodzaak worden, aangezien 3D-printen naar de productievloeren verhuist. Dit betekent uiteindelijk dat het aantal slimmere systemen in de nabije toekomst alleen maar zal toenemen.
6. Gebrek aan industriebrede standaarden
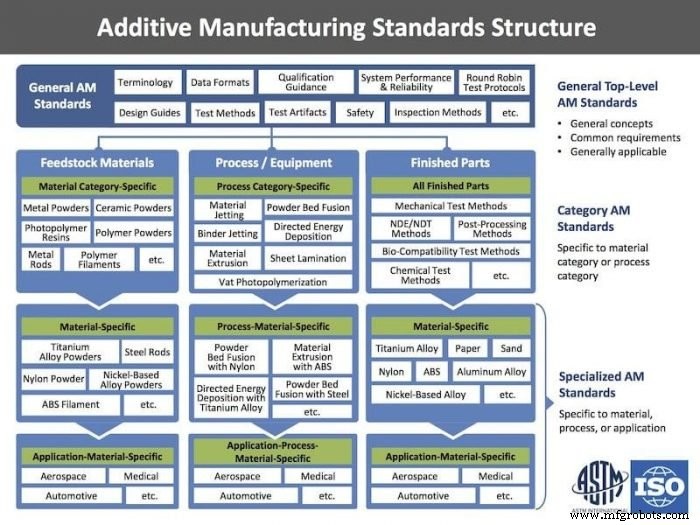
“Het zou ongelooflijk gunstig zijn voor alle belanghebbenden en kiezers als de industrie over het algemeen betere normen zou hebben, normen die universeel worden begrepen en geaccepteerd. Met standaarden kunnen bedrijven appels met appels vergelijken en intelligente beslissingen nemen die geïmplementeerd kunnen worden binnen een alomvattend ecosysteem van leveranciers, fabrikanten en gebruikers.”
Avi Reichental, oprichter van XponentialWorks
In de productie zijn normen essentieel, omdat ze de parameters schetsen waaraan moet worden voldaan om een kwaliteitsproduct te leveren. Grondstoffen, machines, operators en ingenieurs van apparatuur, leveranciers en het fabricageproces zelf hebben allemaal normen en een mechanisme nodig voor kwalificatie/certificering volgens die normen om onderdelen met de vereiste kwaliteit te maken.
Hoewel 3D-printen bestaat al meer dan 30 jaar, maar de productiewereld begon het pas recentelijk te erkennen als een productiemethode. Om deze reden is de industrie net begonnen met het ontwikkelen van productierelevante en industriebrede normen.
“Het is geweldig als je het onderdeel kunt maken, maar als je niet kunt bewijzen dat het een goed onderdeel is, heeft niemand er iets aan. Normen brengen ons over die grens om onderdelen te kunnen produceren, verkopen en in de productie te kunnen gebruiken.”
Matthew Donovan, hoofdingenieur voor additieve productie bij Oerlikon
Het gebrek aan 3D-printstandaarden blijft een van de belangrijkste knelpunten die de bredere acceptatie ervan vertragen.
Er zijn echter veel veelbelovende ontwikkelingen op dit gebied. Enkele van de grootste organisaties die normen ontwikkelen, zoals ISO en ASTM International, hebben commissies opgericht die zich bezighouden met de ontwikkeling van AM-normen. In 2018 keurden de twee organisaties 28 normen goed, en de komende jaren zullen er nog veel meer worden uitgegeven.
De ontwikkeling van normen wordt ook enorm ondersteund door samenwerking en partnerschappen in de sector. Een voorbeeld is een samenwerking tussen Oerlikon en Boeing. De samenwerking is gericht op het gebruik van AM in de lucht- en ruimtevaart en defensie en is gericht op het standaardiseren van materialen en processen voor het 3D-printen van structurele titaniumcomponenten op poederbasis.
Misschien is de krachtigste samenwerking de lancering van Additive Manufacturing Center van Excellence (AM CoE) vorig jaar. De nieuwe faciliteit, opgericht door ASTM International in samenwerking met Auburn University, NASA, EWI en het in het VK gevestigde Manufacturing Technology Centre (MTC), is gericht op het overbruggen van R&D en standaardisatie om belangrijke lacunes in de sector op te vullen.
In september kondigde ASTM International de tweede financieringsronde aan met als doel de standaardisatieprojecten van AM CoE te ondersteunen. Elk van de negen projecten draagt bij aan verschillende standaardlacunes in ontwerp, grondstof, proces, nabewerking, testen en kwalificatie.
Hoewel het ontwikkelen van normen een tijdrovend proces is, suggereert de recente vooruitgang dat het zal uiteindelijk resultaten opleveren, waardoor fabrikanten AM-toepassingen sneller en gemakkelijker kunnen ontwikkelen en implementeren.
Uitdagingen voor het personeel
7. Gebrek aan begrip en expertise in AM
“[Het] personeelsbestand is op dit moment erg belangrijk. Er zijn niet genoeg ingenieurs, managers, leidinggevenden die de technologie echt goed genoeg begrijpen om te werken en een strategie te ontwikkelen om te krijgen wat ze nodig hebben om eruit te halen.”
John Barnes, oprichter van The Barnes Group Advisors
Een gebrek aan grondig begrip van de mogelijkheden van 3D-printtechnologieën kan veel toetredingsdrempels creëren. Momenteel is er nog een kennislacune in termen van wat 3D-printtechnologieën zijn, wat hun mogelijkheden zijn en hoe ze kunnen worden gebruikt. Als gevolg hiervan zijn bedrijven, die zouden kunnen profiteren van de technologie, niet bereid om deze over te nemen, omdat ze moeite hebben om een businesscase of use case voor 3D-printen te ontwikkelen.
"Bedrijven zien de mogelijkheid voor additive manufacturing, maar hebben vaak niet genoeg expertise met de technologie om echt te begrijpen hoe ze snel in productie kunnen gaan."
Robert Yancey, Director of Manufacturing and Production Industry Strategy and Business Development bij Autodesk
“De meerderheid van onze klanten begrijpen de technologie nog steeds niet echt goed en weten niet hoe ze deze moeten gebruiken of wanneer ze deze moeten gebruiken. Vaak denken ze dat je met een 3D-printer alles kan en dat 3D-printen andere technologieën kan vervangen, wat niet waar is.”
Alessio Lorusso, CEO van Roboze
Het is een andere uitdaging om het verschil tussen traditionele en additieve technologieën te begrijpen. 3D-printen heeft zijn eigen ontwerp- en fabricageregels, die de haalbaarheid bepalen om een onderdeel met deze technologie te produceren.
Dit betekent dat de technologie contra-intuïtief kan zijn voor ingenieurs die zijn opgeleid om te ontwerpen voor traditionele productie en die een steile leercurve nodig hebben om deze onder de knie te krijgen.
“Je hebt een mentaliteit van kijken naar traditionele productietechnieken, en we zijn opgeleid met traditionele productietechnieken. Mensen beginnen vaak met onderdelen die op traditionele wijze zijn gemaakt en willen dat onderdeel forceren, maar dat komt niet altijd overeen."
Wiener Mondesir, medeoprichter en Chief Technology Officer van Arevo
Gelukkig richten veel bedrijven zich nu op het overbruggen van deze kenniskloof. Sommigen lanceren online en on-site cursussen om ingenieurs te helpen bij het ontwikkelen van 3D-printvaardigheden, terwijl anderen centres of excellence oprichten om hun expertise in AM te verdiepen.
Het inschakelen van AM-adviesbureaus is een andere geweldige manier om kennisoverdracht te bevorderen, naast het bijwonen van AM-conferenties.
Uiteindelijk kunnen bedrijven alleen door te leren over de mogelijkheden en beperkingen van 3D-printen deze kennis gebruiken om succesvolle toepassingen voor de technologie te ontwikkelen.
“Het is de vraag of je goed moet nadenken over welke technologieën het beste bij welke toepassingen passen. Het is belangrijk om duidelijk te zijn over het probleem dat je probeert op te lossen en de juiste tool te kiezen om dat probleem op te lossen.”
Duncan McCallum, CEO van Digital Alloys
Financiële uitdagingen
8. De initiële investering doen
AM adopteren kost tijd en moeite. De grootste barrière voor adoptie kan echter liggen in de substantiële investeringen die nodig zijn om AM op de productievloer te krijgen.
Investeren in AM gaat niet alleen over het kopen van de apparatuur. Het gaat meer om investeren in het AM-ecosysteem, dat software, materialen, training van medewerkers, nabewerkingsapparatuur, certificering omvat en ten slotte het opzetten van een faciliteit om dit alles te huisvesten.
Het kapitaal en de middelen die nodig zijn om deze puzzel in elkaar te zetten, zijn soms zo enorm dat een organisatie niet wil of zelfs niet kan investeren in AM.
"De kosten van apparatuur moeten omlaag om de technologie voor bredere markten te ontsluiten."
Armin Wiedenegger, Strategy &Business Development voor Additive Manufacturing bij voestalpine High Performance Metals GmbH
Er zijn echter bedrijven die hardware toegankelijker maken. Aan de polymeerkant ontwikkelt een aantal 3D-printerfabrikanten industriële desktop 3D-printers, die eenvoudig te installeren en te gebruiken zijn. Dergelijke systemen kosten doorgaans veel minder dan high-end 3D-printers, die gemakkelijk honderdduizenden dollars kunnen opleveren.
Het in het VK gevestigde autoproductiebedrijf Dunlop Systems and Components heeft bijvoorbeeld de composiet 3D-printer van Markforged geïntegreerd, met een prijs van ongeveer $ 15.000.
In minder dan negen maanden na installatie van de 3D-printer ontdekte het bedrijf meerdere toepassingen voor de technologie, waardoor het tot £ 40.000 per jaar kon besparen. Het bedrijf zegt ook dat het de terugverdientijd binnen zes maanden had, wat behoorlijk indrukwekkend is.
Er zijn vergelijkbare ontwikkelingen aan de metaalkant, met bedrijven als Desktop Metal, Markforged en Xact Metal, die metalen AM-systemen op instapniveau aanbieden. Dergelijke metalen 3D-printers zijn compact en kosten tot $ 150.000, wat een fractie is van de kosten in vergelijking met grotere metalen 3D-printers.
Hoewel investeringen in AM-technologie ontmoedigend kunnen zijn, kan het vaak worden gerechtvaardigd als we kijken naar de algehele impact van de technologie op het uiteindelijke resultaat. Daarom is het belangrijk om een businesscase te ontwikkelen voordat je aan de slag gaat. In het geval van Dunlop bijvoorbeeld, begon het bedrijf met het identificeren van een handvol quick wins die de kosten konden verlagen en op korte termijn duidelijke financiële uitbetalingen konden genereren.
Als ze succesvol zijn, zullen de quick wins de aandacht trekken en een gevoel van momentum creëren, waardoor uiteindelijk middelen worden gegenereerd die kunnen worden geïnvesteerd in ambitieuzere projecten op langere termijn.
Workflow- en integratie-uitdagingen
9. Onsamenhangend AM-ecosysteem
“Het hele AM-ecosysteem is gefragmenteerd:er zijn veel kleine oplossingen en bedrijven die je bij elkaar moet rapen om een workflow en end-to-end-oplossing te creëren.”
Dave Conover, Chief Technologist of Additive Manufacturing bij Ansys
Om AM-processen op industrieel niveau te laten schalen, moet de AM-waardeketen, die begint van concept tot productie en nabewerking van het product, meer geconsolideerd worden.
Momenteel is de markt verzadigd met veel verschillende oplossingen, die idealiter zouden kunnen worden geïntegreerd om een alomvattend aanbod te creëren, waardoor de acceptatie van de technologie wordt vereenvoudigd.
Als gevolg hiervan worden bedrijven die AM willen adopteren, geconfronteerd met de noodzaak om verschillende oplossingen te kopen en deze vervolgens samen te laten werken. Dit gebrek aan integratie in de AM-waardeketen zorgt voor veel inefficiënties in de workflow.
Sommige bedrijven overwinnen deze uitdaging door samenwerking. Veel AM-hardwarefabrikanten werken samen met softwareleveranciers om de gebruikerservaring te verbeteren.
Een voorbeeld is de samenwerking tussen ontwikkelaar van industriële desktop 3D-printers, RIZE, en softwarebedrijf Dassault Systèmes. Met deze samenwerking zullen SOLIDWORKS en RIZE van Dassault samenwerken om een naadloze integratie tussen SOLIDWORKS-ontwerpsoftware en RIZE-printers mogelijk te maken.
Andere bedrijven consolideren het AM-ecosysteem door hun rol in de waardeketen uit te breiden. Henkel, een chemische fabrikant en formuleringsspecialist, heeft bijvoorbeeld een verscheidenheid aan aanbiedingen ontwikkeld in de hele waardeketen.
Deze omvatten het produceren van op maat gemaakte materiaalformuleringen, het verkopen van printers onder het Loctite-merk en het doorverkopen van printapparatuur vervaardigd door HP en Carbon. Henkel biedt ook diensten aan voor het printen en nabewerken van onderdelen.
"Het creëren van ecosystemen en samenwerken kan een belangrijke factor zijn om de acceptatie van [3D-printen] nog verder te versnellen."
Avi Reichental, oprichter van XponentialWorks
Uiteindelijk zal het optimaliseren van de onderlinge verbinding tussen alle elementen in de AM-waardeketen de sleutel zijn tot het creëren van een sterkere industrie.
10. Een gebrek aan digitale infrastructuur
Om 3D-printen in productie te kunnen gebruiken, hebben bedrijven de juiste digitale infrastructuur nodig om hun 3D-printactiviteiten efficiënt te beheren.
Veel bedrijven zetten een dergelijke infrastructuur op door gebruik te maken van kant-en-klare IT-oplossingen. In veel gevallen zijn deze oplossingen ontwikkeld met de vereisten van traditionele productie in gedachten en zijn ze vaak niet geoptimaliseerd voor 3D-printworkflows.
Om dit probleem op te lossen, heeft de industrie software voor workflowbeheer ontwikkeld, specifiek voor 3D-printen. Dergelijke software helpt bij het beheren van de volledige workflow, van aanvraagbeheer, afdrukbaarheidsanalyse en machineanalyse tot productieplanning, naverwerkingsbeheer en communicatie met leveranciers.
Als gevolg hiervan kan een bedrijf een gecentraliseerd productieplanning- en monitoringsysteem hebben, waarmee het onderdelen kan volgen en projecten kan bekijken, wat een betere traceerbaarheid mogelijk maakt.
Werkstroombeheersoftware is hard op weg een van de belangrijkste oplossingen te worden die nodig zijn om de digitale infrastructuur voor AM-productie te creëren. It makes day-to-day business processes more efficient, by coordinating tasks between people. Finally, it helps to synchronise data between systems, making the integration of AM into a digital manufacturing environment much simpler.
The evolving industry
As a young technology, 3D printing has many challenges, but the good thing is that the industry is eager to overcome them. Over the last decade, the industry has made a quantum leap forward by developing better and faster systems, creating more materials and automation solutions and expanding the list of approved standards.
Furthermore, we’ve seen a lot of effort made to bridge the knowledge gaps and foster a new generation of AM professionals. Finally, the industry itself is becoming more consolidated, as companies are looking to partner, in a bid to create comprehensive solutions.
All these activities are indicative of a thriving industry, which will continue to grow and evolve in the years to come.
Take a look at our previous Expert Roundup discussing the future of industrial 3D printing .
3d printen
- Een businesscase opstellen voor een productie-uitvoeringssysteem in additieve productie
- Wat is de businesscase voor het uitvoeringssysteem voor additieve fabricage bij de productie van reserveonderdelen?
- Heroverwegen van het software-integratieproces voor additive manufacturing-activiteiten
- Additive manufacturing en spuitgieten — een nieuwe visie op productielevenscycli
- De waarheid over schaalvoordelen voor additieve productieprocessen
- De volgende grens voor schaalbare additieve productie? Additieve MES-software
- De zaak voor 3D-printen in de productie
- De impact van additive manufacturing op industriële productie
- Een snelle blik op de grootste trends in industriële productie voor 2020
- Productieproductie aanpassen aan de EV-boom
- De voordelen en uitdagingen voor hybride productie begrijpen