Applicatie Spotlight:3D-printen in de spoorwegindustrie
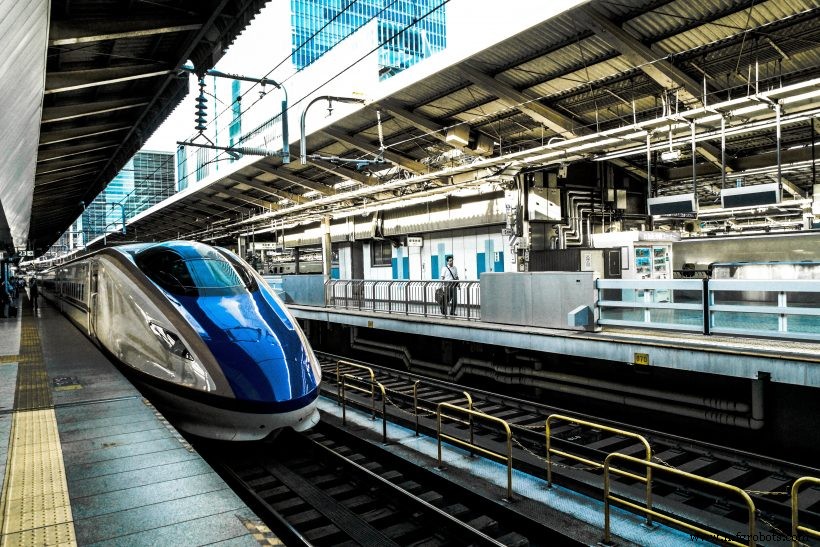
In de afgelopen 12 maanden hebben veel spoorwegmaatschappijen, waaronder Deutsche Bahn, Bombardier en Angel Trains, geïnvesteerd in 3D-printen of hun 3D-printmogelijkheden opgevoerd.
16 procent van de bedrijven in de logistiek en transportsector gebruikt nu 3D-printen om reserveonderdelen te vervaardigen, volgens een recent rapport van EY.
Wat drijft deze adoptie?
In de Application Spotlight van deze week kijken we naar de drijvende krachten achter de toegenomen acceptatie van additive manufacturing (AM) in de spoorwegindustrie, naast het verkennen van de meest opwindende gebruiksscenario's.
Bekijk de andere toepassingen die in deze serie worden behandeld:
3D-printen voor warmtewisselaars
3D-printen voor lagers
3D-printen voor fietsproductie
3D-printen voor productie van digitale tandheelkunde en heldere uitlijners
3D-printen voor medische implantaten
3D-geprinte raketten en de toekomst van de fabricage van ruimtevaartuigen
3D-printen voor de productie van schoenen
3D-printen voor elektronische componenten
3D-geprinte brillen
3D-printen voor productie van eindonderdelen
3D-printen voor beugels
3D-printen voor turbineonderdelen
Hoe 3D-printen zorgt voor beter presterende hydraulische componenten
Hoe 3D-printen innovatie in de kernenergie-industrie ondersteunt
Waarom gebruiken spoorwegmaatschappijen industrieel 3D-printen?
Een trein bouwen is geen sinecure, omdat er hoogwaardige componenten nodig zijn om de trein op het spoor te houden, meestal tientallen jaren.
Maar wat gebeurt er als sommige componenten kapot gaan? Het kan relatief eenvoudig zijn om vervangingen te vinden voor recent vervaardigde onderdelen, maar als het gaat om componenten die 20 tot 30 jaar geleden zijn gemaakt, wordt het proces ingewikkeld.
In veel gevallen worden spoorwegmaatschappijen geconfronteerd met de situatie dat de productie van de benodigde reserveonderdelen is stopgezet of dat fabrikanten niet meer actief zijn. Gezien het kleine aantal benodigde reserveonderdelen, is het opnieuw ontwerpen en vervaardigen van het onderdeel, met behulp van traditionele methoden die zijn afgestemd op de productie van grote volumes, vaak economisch niet zinvol.
De kosten van stilstand per dag voor een trein zijn ook behoorlijk hoog, waardoor spoorwegmaatschappijen nieuwe manieren zoeken om verouderde reserveonderdelen op een snellere en goedkopere manier te produceren.
3D-printen wordt een van de technologieën die dergelijke problemen kunnen oplossen. Het is een digitale productietechnologie, wat betekent dat het afhankelijk is van digitale workflows en geen extra hulpmiddelen, zoals mallen, nodig heeft om een onderdeel te maken.
Productie zonder gereedschap, mogelijk gemaakt door 3D-printen, kan de productietijd voor verouderde reserveonderdelen aanzienlijk verkorten, in sommige gevallen met wel 95%. Het proces gaat ook vaak gepaard met reverse engineering, vooral wanneer het oorspronkelijke ontwerp van een onderdeel verloren is gegaan.
Op deze manier kunnen spoorwegmaatschappijen het onderhoudsproces van de trein versnellen en de treinen efficiënter dan voorheen weer in gebruik nemen.
Earge adopters van 3D-printen in de spoorwegindustrie , zoals Deutsche Bahn, hebben meerdere onderdelen geïdentificeerd die als vervanging 3D-geprint kunnen worden. Hiertoe behoren koffiemachine-onderdelen, kapstokhaken, stuurhoezen, hoofdsteunframes en zelfs brailleborden voor blinde reizigers. De lijst met onderdelen die 3D-geprint kunnen worden voor de spoorwegindustrie wordt echter voortdurend uitgebreid.
Een andere drijfveer voor de adoptie van 3D-printen in de spoorwegindustrie is de mogelijkheid om productiehulpmiddelen zoals mallen en armaturen sneller en op aanvraag te produceren. Hoewel het een minder gepubliceerde use case is, zijn 3D-geprinte tools doorgaans lichter dan traditionele tegenhangers en kunnen ze ergonomisch worden ontworpen, wat meer gebruiksgemak voor werknemers oplevert.
3D-printtechnologieën gebruikt voor spoorwegonderdelen
De meeste 3D-geprinte reserveonderdelen en gereedschappen voor de spoorwegindustrie worden vervaardigd met behulp van polymeeradditieventechnologieën, zoals Fused Filament Fabrication (FFF) en Selective Laser Sintering (SLS). De technologieën zijn geoptimaliseerd om te werken met hoogwaardige thermoplasten, zoals nylon en ULTEM.
Om te worden gebruikt voor treincomponenten, moeten deze materialen voldoen aan de brandveiligheidsnormen van de industrie. Verschillende bedrijven bieden vlamvertragende thermoplasten aan. Stratasys heeft bijvoorbeeld een materiaal ontwikkeld dat voldoet aan de Rail Standard EN45545-2 voor brandveiligheid.
Markforged, een ontwikkelaar van composiet 3D-printers, heeft onlangs ook een vlamvertragend composietmateriaal op nylonbasis geïntroduceerd. Het materiaal is bedoeld om het scala aan 3D-printtoepassingen in de spoorwegindustrie te verbreden, naast de lucht- en ruimtevaart-, automobiel- en defensie-industrie.
Hoewel het merendeel van de 3D-geprinte onderdelen voor de spoorwegindustrie uit polymeer bestaan, wint ook 3D-printen met metaal aan populariteit. Technologieën zoals Selective Laser Melting (SLM) en Metal Binder Jetting worden het vaakst toegepast om onderdelen te maken met metalen zoals aluminium, staal en, meer recentelijk, titanium.
3D-printtoepassingen in de spoorwegindustrie
Deutsche Bahn 3D print een metalen vervangend onderdeel
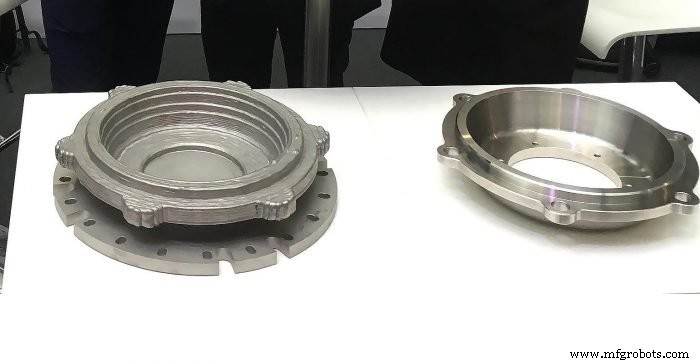
De Duitse spoorwegmaatschappij Deutsche Bahn is een van de pioniers geweest bij het toepassen van 3D-printen voor reserveonderdelen. Deutsche Bahn heeft de afgelopen jaren de mogelijkheden geïdentificeerd om AM voor meer dan 100 use-cases te gebruiken. De meeste onderdelen zijn relevant voor de beschikbaarheid, wat betekent dat ze moeilijk te verkrijgen kunnen zijn, waardoor het voertuig een maand lang stilstaat.
Een voorbeeld van zo'n onderdeel is een wielstellagerdeksel voor een locomotief van de serie 294. Dit model is in de jaren 60 en 70 in gebruik genomen en voor sommige onderdelen, zoals deze kap, ontbreken reserveonderdelen.
Traditioneel zou Deutsche Bahn een nieuw onderdeel moeten laten produceren met behulp van een gietproces. Deze methode omvat echter meestal hoge minimale aankoophoeveelheden en de levering van een deel kan enkele maanden duren.
AM verscheen als een natuurlijk alternatief, omdat het dit onderdeel sneller en op aanvraag kon maken. Het bedrijf wendde zich tot een servicebureau dat een lagerdeksel in 3D printte met behulp van Wire Arc Additive Manufacturing (WAAM)-technologie. Het WAAM-proces gebruikt draad als grondstof. De draad wordt door een mondstuk gevoerd en laag voor laag in het uiteindelijke werkstuk gelast.
Het onderdeel, dat 13 kg weegt, werd in slechts 7 uur bedrukt, waardoor Deutsche Bahn voordelen kreeg zoals een groter onderdeel beschikbaarheid en aanzienlijk lagere productiekosten.
Siemens Mobility:3D-geprinte tooling
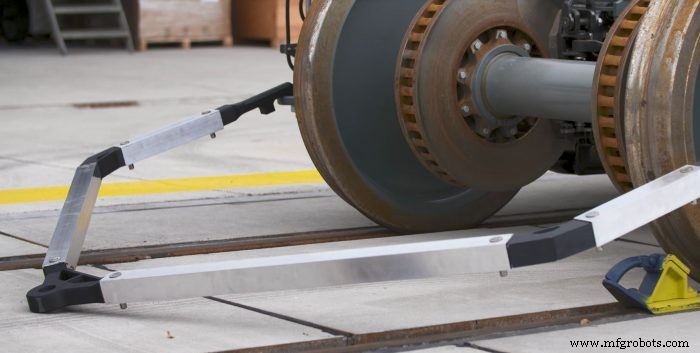
Siemens Mobility, een bedrijf dat gespecialiseerd is in intelligente verkeerssystemen en spoortechnologie, heeft 3D-printen toegepast in zijn RRX Rail Service Center om naast reserveonderdelen ook complexe gereedschappen te produceren.
In een voorbeeld heeft het nieuwe onderhoudsdepot een 3D-geprint onderdeel van een essentieel verbindingshulpmiddel dat wordt gebruikt bij het onderhoud van treinstellen (het draaistel is het chassis of de constructie die de wielstelas draagt). Het is vrij moeilijk om met conventionele methoden te produceren, omdat het gereedschap een complexe vorm heeft die een hoge mate van maatwerk vereist.
Bovendien wegen draaistellen enkele tonnen, wat betekent dat ze moeten worden gemaakt van robuuste en duurzame materialen die bestand zijn tegen de aanzienlijke spanningen die worden uitgeoefend wanneer de trein in beweging is.
Als alternatief gebruikte het team in het centrum de FDM-technologie van Stratasys en een industriële ULTEM 9085. Door 3D-printen kon Siemens Mobility de voordelen van 3D-printen op maat benutten en de traditionele productiemethoden hiervoor vervangen tooling applicatie.
Het bedrijf meldt ook dat 3D-geprinte tooling hen heeft geholpen hun afhankelijkheid van outsourcingtools via leveranciers te verminderen en ook de kosten per onderdeel te verlagen.
Angel Trains' verkenning van 3D-printen
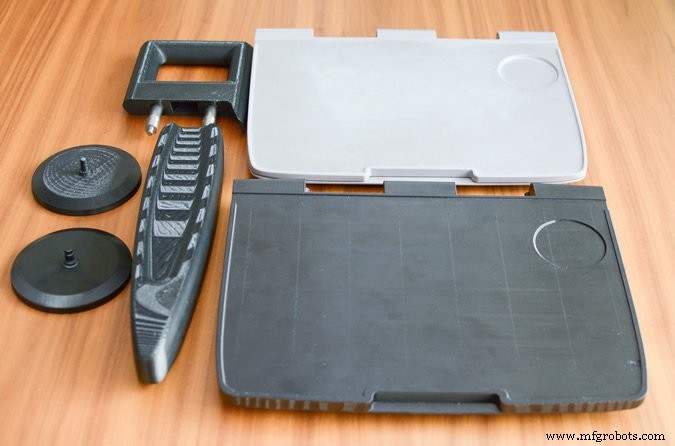
Leasemaatschappij voor rollend materieel, Angel Trains, is onlangs een samenwerking aangegaan met Stratasys, op zoek naar 3D-geprinte treininterieurcomponenten, zoals armleuningen, handgrepen en rugleuningtafels.
De gekozen componenten worden nu getest op in dienst zijnde passagierstreinen. Tot nu toe is de proef positief verlopen. De productie van de 3D-geprinte armleuning duurde bijvoorbeeld slechts een week - een afname van 94% in vergelijking met conventionele productiemethoden
Het bedrijf gebruikt Stratasys FDM-technologie in combinatie met ULTEM 9085 voor hoge temperaturen thermoplast, om op aanvraag reserveonderdelen in 3D te printen. Het gebruikte filament zou compatibel zijn met de normen van de spoorwegindustrie (met name de spoornorm EN45545-2) en heeft een grotere brandweerstand en duurzaamheid dan traditionele thermoplasten.
In een ander geval hielp 3D-printen Angel Trains om vervangingen voor handgrepen te produceren. De originele reserveonderdelen waren verouderd en de leverancier was failliet. Voor het maken van een reserveonderdeel, met behulp van een traditionele methode, zou de productie van een nieuwe productietool nodig zijn geweest, wat zou kunnen leiden tot kosten tot £ 15.000 en een doorlooptijd van twee en een halve maand.
Met behulp van FDM 3D-printen kon het bedrijf echter alle zeven hendels die nodig zijn voor de treinen produceren in slechts drie weken en tegen aanzienlijk lagere kosten.
Het is opwindend dat Angel Trains ook nieuwe aanpassingsmogelijkheden onderzoekt met 3D-printen. Zo onderzoekt het bedrijf de mogelijkheid om tafels op de rugleuningen in 3D te printen met braille, zodat de passagier weet dat het toilet tien rijen van zijn stoel verwijderd is.
Als ze succesvol zijn, kunnen dergelijke toepassingen het onderhoud van treinen en de passagierservaring in de toekomst aanzienlijk verbeteren.
CAF's prestaties op het gebied van 3D-printen
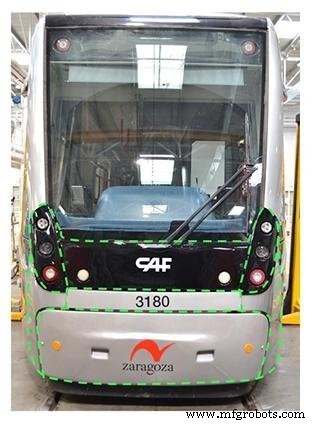
CAF, een Spaanse fabrikant van spoorvoertuigen, uitrustingen en bussen, is er ook in geslaagd om 3D-printen in te zetten voor de productie van reserveonderdelen en functionele componenten. Sinds september 2016 zou CAF ongeveer 2 400 3D-geprinte onderdelen hebben geproduceerd voor gebruik in zijn rollend materieel, waaronder bekerhouders, radiobeugels, raamkozijnen, ruitenwisserkappen en deursteunen.
Het bedrijf maakt ook gebruik van grootschalig 3D-printen om externe onderdelen tot enkele meters te produceren. Een van die onderdelen is een front-end component, 3D-geprint voor een Urbos tram. Vermoedelijk is het onderdeel 3D-geprint met een Super Discovery FFF 3D-printer, ontwikkeld door de Spaanse fabrikant CNC Bárcenas.
CAF noemt de mogelijkheid om onderdelen te produceren, met verschillende afmetingen en complexe geometrieën, als een belangrijk voordeel van 3D-printtechnologieën. Het bedrijf zegt dat het hen helpt de afhankelijkheid van mallen en originele patronen te doorbreken bij het produceren van componenten, waardoor de time-to-market voor een nieuw onderdeel wordt verkort.
Andere voorbeelden
Het aantal spoorwegmaatschappijen dat 3D-printen begint te verkennen, groeit.
Bombardier gaat bijvoorbeeld een Stratasys 3D-printer installeren om de productie van railonderdelen te versnellen en aan te passen. De fabrikant is van plan de technologie te gebruiken voor het 3D-printen van treinonderdelen binnen en buiten, zoals luchtkanalen, behuizingen en kabelhouders.
Wabtec Corporation, een wereldwijde fabrikant voor de spoorweg- en vervoersindustrie, is ook op de kar van 3D-printen gesprongen. Deze zomer investeerde het bedrijf in de H2-binderstraaltechnologie van GE Additive. Wabtec heeft al gebruiksscenario's geïdentificeerd voor maar liefst 250 componenten in zijn productlijnen, die met AM kunnen worden vervaardigd.
3D-printen in de spoorwegindustrie:een transformatieve impact
De voordelen van het gebruik van 3D-printen in de spoorwegindustrie worden steeds duidelijker. Bedrijven in de sector staan te popelen om de technologie te implementeren, problemen met verouderde reserveonderdelen en lange doorlooptijden voor tooling en eindgebruikcomponenten aan te pakken.
Uit bovenstaande voorbeelden blijkt echter dat de reis van 3D-printen voor de meeste bedrijven nog maar net is begonnen. Het zal hen zowel tijd als geld kosten om erachter te komen hoe ze de technologie ten volle kunnen benutten. Maar de beloning die aan het einde van de reis wacht, belooft een transformerende, positieve impact te hebben op de toeleveringsketens en serviceactiviteiten van het spoor.
3d printen
- 6 manieren om de kosten van 3D-printen te verlagen
- Applicatie Spotlight:3D-printen voor medische implantaten
- Applicatie Spotlight:3D-printen voor digitale tandheelkunde &Clear Aligner-productie
- Applicatie Spotlight:3D-printen voor fietsproductie
- Applicatie Spotlight:3D-printen voor lagers
- Applicatie Spotlight:3D-printen voor warmtewisselaars
- Applicatie Spotlight:5 elektronische componenten die kunnen profiteren van 3D-printen
- Applicatie Spotlight:3D-printen voor schoenen
- COVID-19 heeft 3D-printen in de schijnwerpers geduwd
- De toekomst van 3D-printen in de maakindustrie
- Is 3D-printen de toekomst van productie?