10 spannende voorbeelden van 3D-printen in de auto-industrie in 2021

Dit artikel is bijgewerkt in mei 2021
De auto-industrie wordt op alle fronten geconfronteerd met eisen:de vraag naar nieuwere, beter presterende voertuigen, evenals de noodzaak om de productie te optimaliseren en de toeleveringsketens en logistiek te stroomlijnen. Een technologie die helpt om deze uitdagingen aan te gaan, is 3D-printen.
3D-printen wordt steeds meer onderzocht in alle gebieden van de autoproductie. Afgezien van het uitgebreide gebruik voor rapid prototyping, wordt de technologie ook gebruikt om tooling en, in sommige gevallen, eindonderdelen te produceren.
Nu het aanbod van 3D-printtoepassingen voor auto's zich blijft uitbreiden, vindt u hieronder enkele van de meest veelbelovende voorbeelden van autobedrijven die de technologie gebruiken om hun productie te verbeteren.
1. Porsche's 3D-geprinte aangepaste stoelen
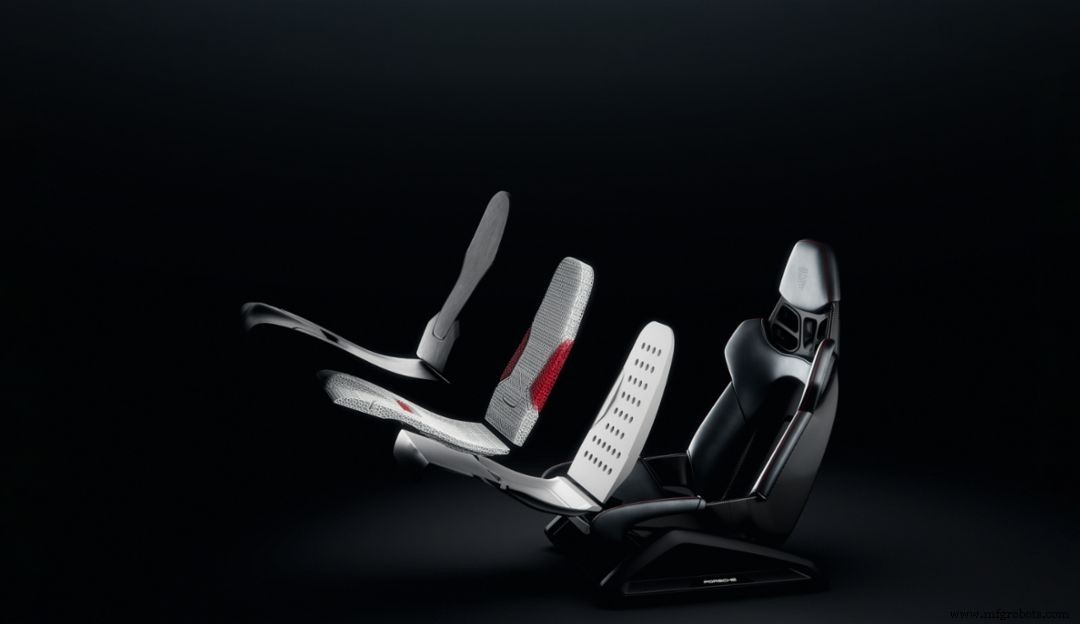
Porsche heeft onlangs een nieuw concept voor sportwagenstoelen geïntroduceerd dat gebruikmaakt van 3D-printen en roosterontwerp.
De nieuwe stoelen zijn voorzien van polyurethaan 3D-geprinte centrale zit- en rugleuningkussensecties, die kunnen worden aangepast met drie stevigheidsniveaus:hard, medium en zacht.
Met zijn gepersonaliseerde stoelen haalt de Duitse autofabrikant signalen uit de autosportsector, waar op maat gemaakte bestuurdersspecifieke stoelmontage een norm is.
Porsche is van plan om al in mei 2020 40 prototypestoelen te printen voor gebruik op Europese racecircuits, waarbij feedback van klanten wordt gebruikt om de definitieve straatlegale modellen voor medio 2021 te ontwikkelen.
Over de hele lijn wil Porsche de stoelaanpassing verder uitbreiden dan stevigheid en kleur door de stoel aan te passen aan de specifieke lichaamscontouren van de klant. 3D-printen blijft momenteel de enige technologie die dit niveau van maatwerk mogelijk maakt.
2. 3D-printen voor autobeugels
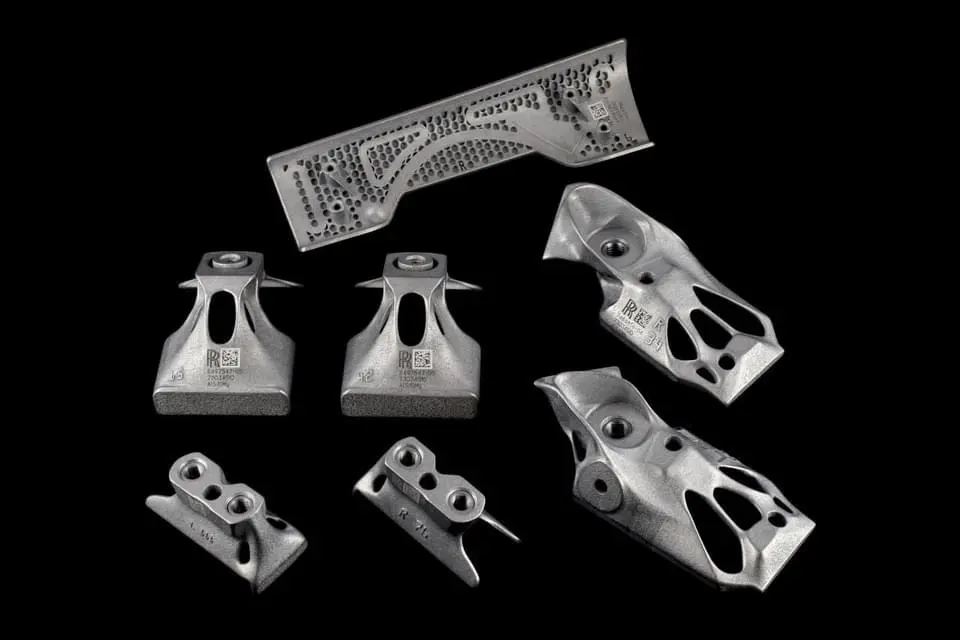
Beugels zijn kleine en nogal alledaagse onderdelen, die in het verleden moeilijk te optimaliseren waren, toen ingenieurs werden beperkt door traditionele productiemethoden. Tegenwoordig kunnen ingenieurs geoptimaliseerde beugels ontwerpen en deze ontwerpen tot leven brengen met behulp van 3D-printen.
Rolls Royce heeft onlangs de mogelijkheden van 3D-printen voor beugels getoond. Het bedrijf toonde de grote partij DfAM-geoptimaliseerde en 3D-geprinte metalen auto-onderdelen, waarvan er vele op beugels lijken.
Kostenbesparingen, snellere productie en ontwerpoptimalisatie zijn doorgaans de belangrijkste redenen om AM voor beugels te gebruiken.
In het voorbeeld van de Rolls Royce was het team in staat om een aantal echt coole functies in onderdelen op te nemen, waaronder de 3D-geprinte merknaam en een QR-code, samen met nummers om het specifieke, unieke onderdeel te identificeren.
Het toevoegen van deze functies tijdens het productieproces is iets dat alleen kan worden bereikt met digitale productie, aangezien geen enkele subtractieve methode ooit zou kunnen concurreren in termen van productiekosten en tijd.
Lees ook:Toepassingsspotlight:3D-geprinte beugels
3. Ford 3D print onderdelen voor de krachtige Mustang Shelby GT500
Ford Motor Company is een van de eerste gebruikers van 3D-printen en kocht zo'n 30 jaar geleden de derde 3D-printer ooit gemaakt.
Ford, dat vorig jaar zijn Advanced Manufacturing Center opende, heeft stappen gezet om 3D-printen te integreren in zijn productontwikkelingscyclus. Nu wil het bedrijf de technologie gebruiken voor productietoepassingen.
Zijn nieuwste voertuig, de 2020 Shelby GT500, is daar een voorbeeld van. De 2020 Shelby GT500, die later dit jaar in de verkoop gaat, is naar verluidt de meest aerodynamisch geavanceerde Mustang tot nu toe.
Virtuele ontwerptests waren een belangrijk onderdeel van het ontwerpproces voor het high-performance voertuig. Met behulp van virtuele tests werden meer dan 500 koelings- en aerodynamische 3D-ontwerpen geanalyseerd om het team in staat te stellen zijn downforce-, rem- en koelingsdoelen te bereiken.
Nadat de meest veelbelovende ontwerpen waren geïdentificeerd, gebruikte het technische team van Ford 3D-printen om prototypes te maken en te testen. Het team heeft bijvoorbeeld meer dan 10 ontwerpen voor frontsplitter-wickers geprint en getest, die ze tegelijkertijd konden verzenden voor testevaluatie.
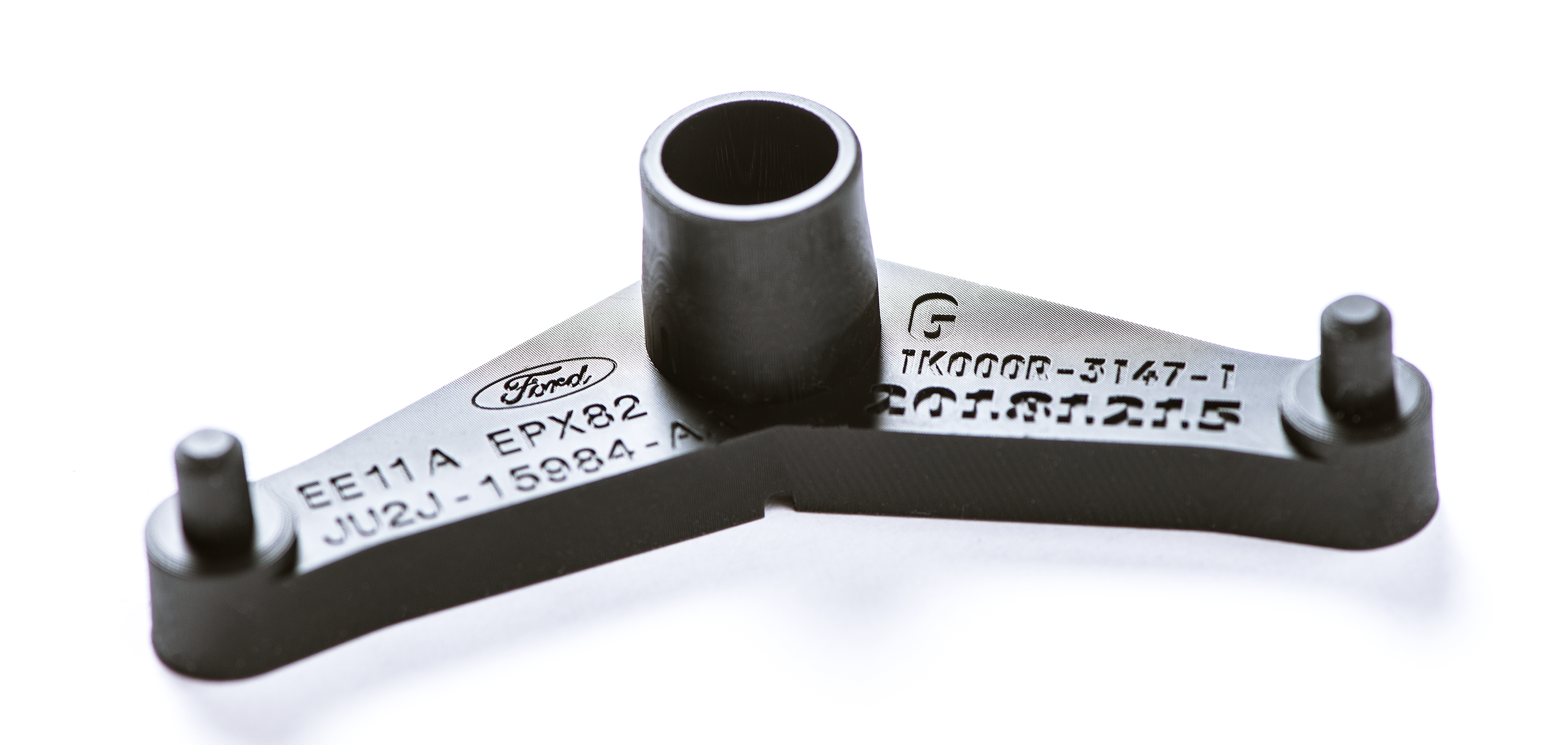
Naast het gebruik van 3D-geprinte prototypes voor ontwerpvalidatie en functionele testen, zal de aanstaande 2020 Shelby GT500 ook twee structurele 3D-geprinte remcomponenten bevatten. Deze componenten zijn gemaakt met behulp van Carbon's Digital Light Synthesis (DLS) 3D-printtechnologie en EPX (epoxy) 82-materiaal, en voldoen aan alle prestatienormen en -vereisten van Ford.
Met deze toepassingen is het duidelijk dat Ford de basis legt om behoorlijk indrukwekkende dingen te kunnen doen met additive manufacturing.
"Additive manufacturing zal steeds meer ingebakken blijven in het dagelijkse deel van wat we als bedrijf doen", verklaarde Ford's technisch leider van AM Technologies, Harold Sears, onlangs in AMFG's Expert Interview-serie. "In plaats van een uitzondering op de norm te zijn, wordt het veel meer geaccepteerd zoals het is gedaan."
Vooruitkijkend zal het spannend zijn om te zien hoe Ford de mogelijkheden van 3D-printen blijft benutten om de productie van zijn voertuigen verder te verbeteren.
4. Volkswagen Autoeuropa:3D-geprint productiegereedschap
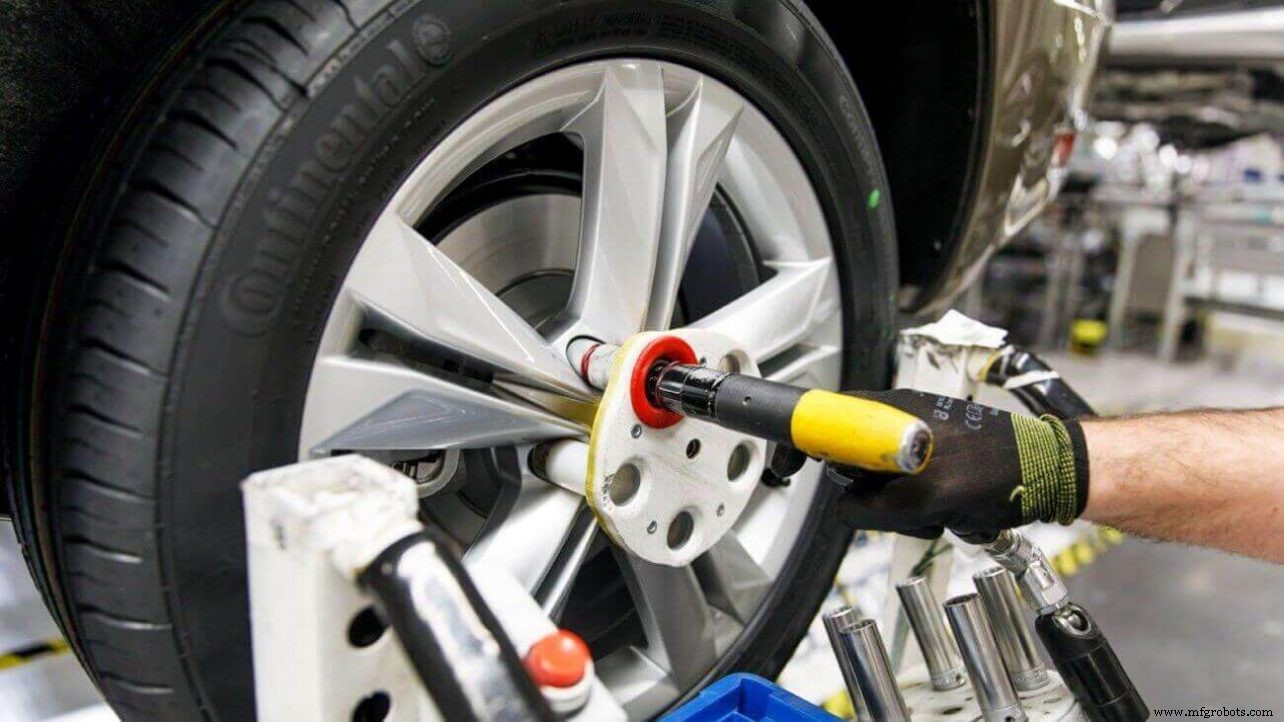
Hoewel prototyping de primaire toepassing van 3D-printen binnen de auto-industrie blijft, wint het gebruik van de technologie voor tooling snel aan populariteit.
Een mooi voorbeeld hiervan is Volkswagen, dat al een aantal jaren 3D-printen in huis heeft.
In 2014 begon het bedrijf met het testen van Ultimaker's desktop 3D-printers om gereedschapsapparatuur te produceren in de Volkswagen Autoeuropa-fabriek in Portugal. Sinds het succes van de pilot heeft Volkswagen de productie van gereedschappen bijna volledig overgeschakeld op 3D-printen.
Het gebruik van de technologie voor deze toepassing brengt een aantal voordelen met zich mee.
Door zijn gereedschap intern te produceren, worden de productiekosten van gereedschap voor de autofabrikant met 90% verlaagd - en worden de doorlooptijden teruggebracht van weken tot slechts enkele dagen. Om een voorbeeld te noemen:een tool als een badge voor de achterklep zou naar verluidt 35 dagen nodig hebben om te worden ontwikkeld met behulp van traditionele productie en zou tot 400 euro kunnen kosten. Met 3D-printen kan dezelfde tool in vier dagen worden geproduceerd voor slechts € 10.
Het gebruik van 3D-printen voor tooling zou Volkswagen in 2017 bijna € 325.000 hebben bespaard, terwijl de ergonomie, productiviteit en tevredenheid van de machinist zijn verbeterd.
Als het gaat om fabricagehulpmiddelen, groeit 3D-printen snel als alternatief voor meer gevestigde manieren om gereedschappen te vervaardigen. Over een paar jaar zullen we waarschijnlijk meer OEM's in de auto-industrie zien overstappen op 3D-geprinte tooling om de efficiëntie van hun productie en de prestaties van hun tools te verbeteren.
Lees ook:6 manieren om de productie-efficiëntie te verbeteren met 3D-geprinte mallen en armaturen
5. 3D-geprinte wielmoeren die autowielen redden van dieven
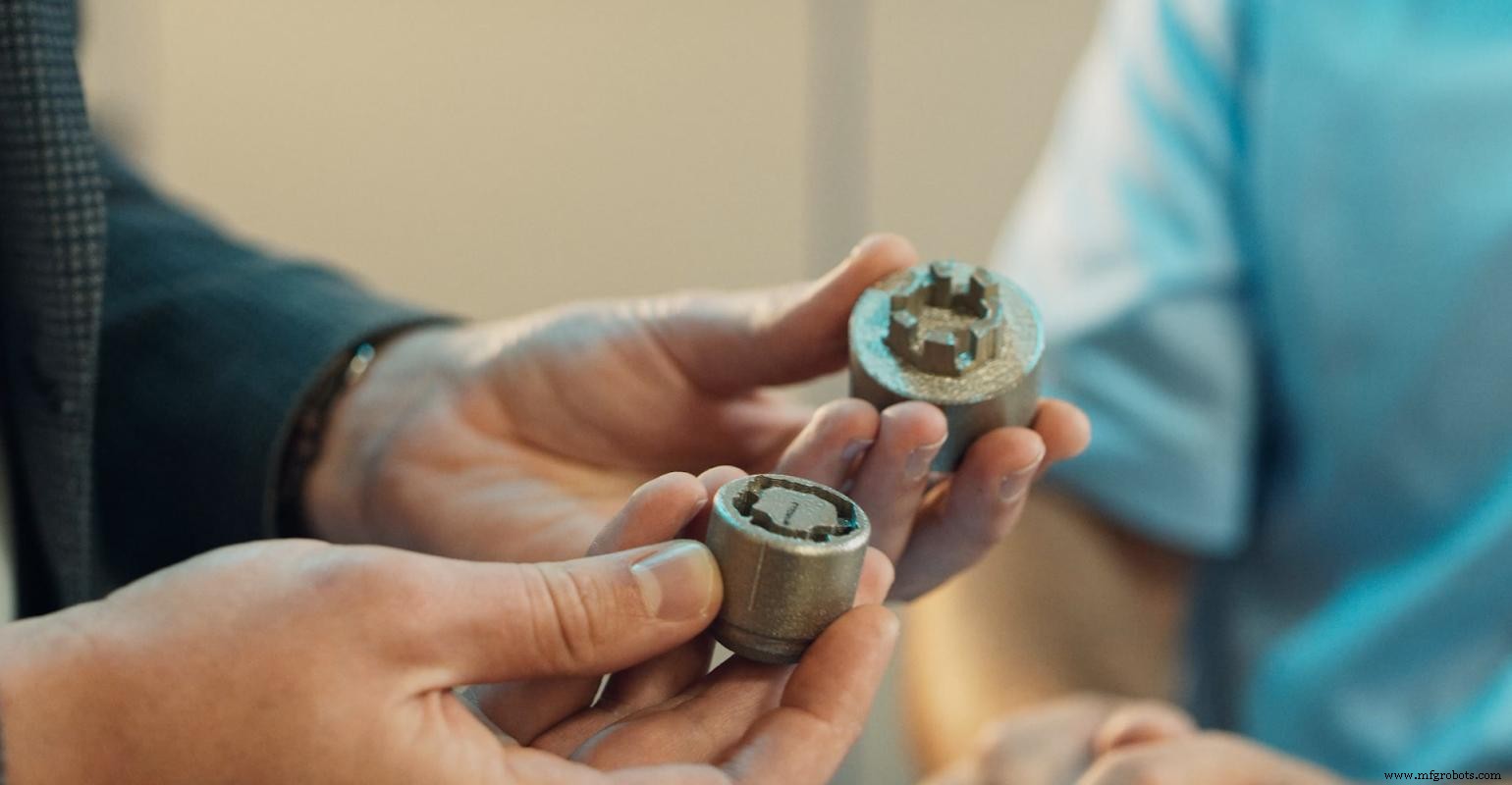
Hoe voorkom je dat dieven autowielen stelen? Ford beantwoordt die vraag met een programma in Europa om op maat gemaakte wielmoeren te 3D-printen voor auto's die beter bestand zijn tegen diefstal.
Normaal gesproken hebben auto's een enkele borgmoer per wiel om te voorkomen dat deze kan worden verwijderd zonder de speciale sleutel die aan de wielsleutel is bevestigd. Maar deze kunnen worden verslagen, dus Ford print patronen voor zijn sloten in 3D die niet zo gemakkelijk kunnen worden gekloond.
Met behulp van 3D-printers van EOS maakt Ford sloten met een aangepast patroon voor elke klant. Door een geluidsgolfpatroon uit een eenvoudige zin te gebruiken, is het mogelijk om een volledig uniek patroon te creëren dat een extra beveiligingslaag biedt op dezelfde manier als vingerafdrukherkenning.
Eenmaal ontworpen, worden het slot en de sleutel 3D-geprint als een enkel roestvrijstalen onderdeel. Nadat ze de twee uit elkaar hebben gehaald, hoeven ze maar een beetje te worden gepolijst om te werken.
Het voordeel van deze sloten is dat ze vrijwel onmogelijk te klonen zijn. Met ongelijk verdeelde ribben in de moer en inkepingen die groter worden naarmate ze dieper naar binnen gaan, is het voor dieven onmogelijk om een wasafdruk van deze sloten te maken zonder de was te breken.
Het veiliger maken van wielen en het aanbieden van meer productpersonalisatie zijn een verder bewijs dat 3D-printen een game-changer is voor de autoproductie.
6. Local Motors &XEV:op weg naar 3D-geprinte auto's?
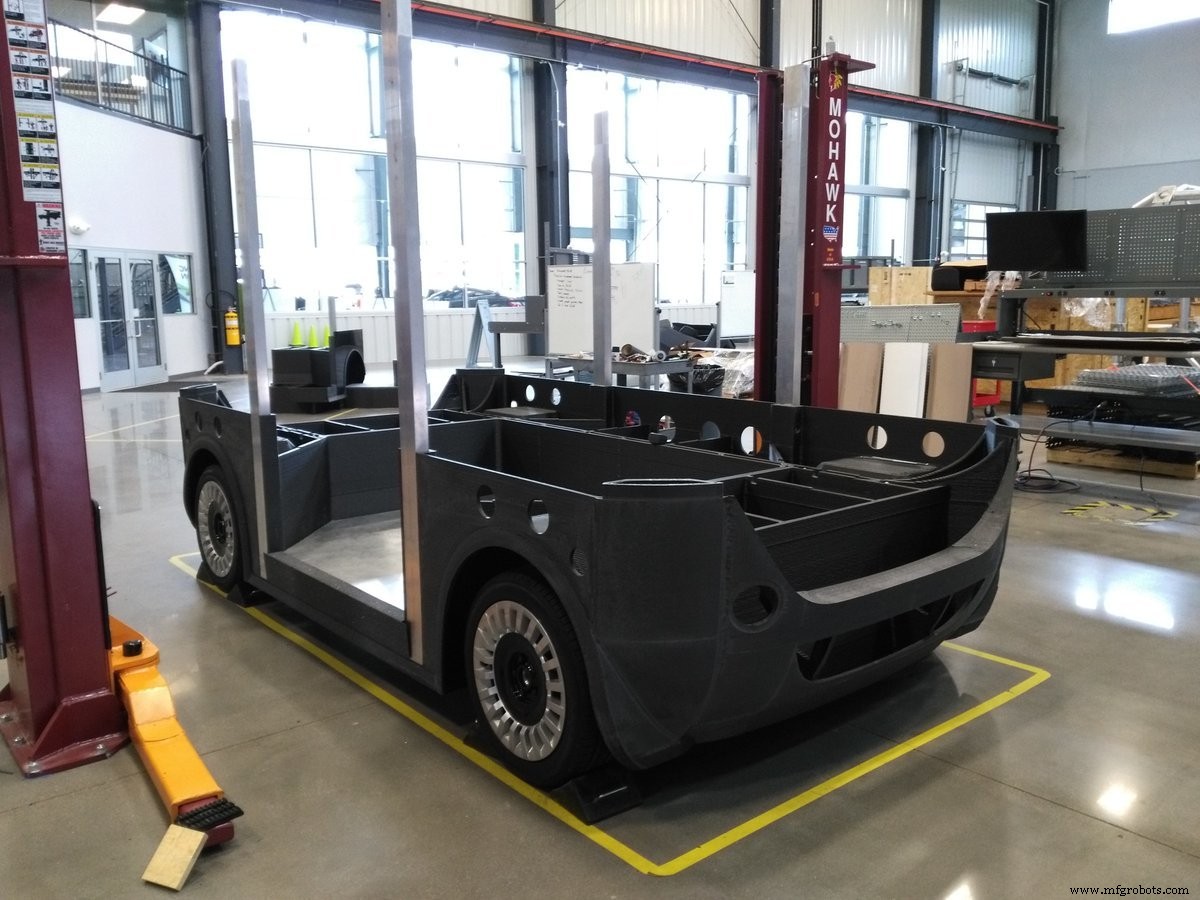
Hoewel nog ver weg, streven een aantal bedrijven ernaar om volledig 3D-geprinte auto's te realiseren. Local Motors, gevestigd in Arizona, is een bedrijf met als doel om volledige voertuigen in 3D te printen.
Het bedrijf maakte een plons in 2014 toen het op de International Manufacturing Technology Show (IMTS) aankondigde wat het beweerde de allereerste 3D-geprinte elektrische auto te zijn - Strati. De auto is gemaakt in samenwerking met Oak Ridge National Laboratory (ORNL) en Cincinnati, Inc.
Twee jaar later onthulde Local Motors Olli, een 3D-geprinte, autonome elektrische shuttle ontworpen voor lokaal vervoer met lage snelheid. De shuttle is voornamelijk ontworpen voor gebruik in stedelijke centra in steden, bedrijfs- en universiteitscampussen en ziekenhuizen.
Dus hoe heeft het bedrijf dit bereikt?
Local Motors gebruikte enkele van 's werelds grootste 3D-printers - ORNL's Big Area Additive Manufacturing (BAAM) en Thermwood's Large Scale Additive Manufacturing (LSAM) -machines - om de meeste componenten van Olli te produceren, inclusief het dak en de onderkant van het voertuig.
Evenzo werd Strati geprint met behulp van de grootschalige 3D-printer van Cincinnati, Inc., en het duurde slechts 44 uur om te voltooien. De wielen en wieldoppen van de auto werden geproduceerd met behulp van een direct 3D-printproces van metaal.
Sinds Olli voor het eerst werd geïntroduceerd, heeft Local Motors meer dan 2.000 combinaties van printmateriaal en versterkende additieven getest en is het nu in staat om de hele minibus in ongeveer 10 uur te printen.
Local Motors schrijft zijn succes toe aan zijn 'digitale voertuigproductiemodel'. Dit bedrijfsmodel stelt het bedrijf in staat om producten op een geheel nieuwe manier op de markt te brengen door samen met een wereldwijde gemeenschap van experts nieuwe ontwerpen te creëren. Het bedrijf gebruikt digitale productietechnologieën, zoals 3D-printen, om voertuigen te vervaardigen en te assembleren in lokale microfabrieken.
3D-printen past perfect bij dit gedistribueerde productiemodel, omdat het een manier biedt om snel ontwerpen te herhalen, onderdelen en producten naar behoefte aan te passen, middelen te besparen en de noodzaak om de inventaris bij te houden, te verminderen.
Hoewel het enige tijd zal duren om volledig 3D-geprinte voertuigen op de weg te zien, kunnen projecten zoals Olli van Local Motors ons een stap dichter bij die opwindende mogelijkheid brengen.
Local Motors is niet het enige bedrijf dat 3D-geprinte auto's nastreeft. Evenzo ontwikkelt de Italiaanse autofabrikant XEV een elektrische LSEV-auto met lage snelheid met behulp van 3D-printen.
Door gebruik te maken van grootformaat FDM-technologie en vier verschillende soorten polyamide en TPU, kan het bedrijf zijn productiekosten met 70% verlagen en profiteren van de lichtgewicht 3D-printaanbiedingen.
De afgewerkte LSEV weegt slechts 450 kilogram en heeft slechts 57 plastic componenten, wat betekent dat hij in een paar dagen kan worden geproduceerd. XEV heeft ook de beslissing genomen om 2.000 van zijn eigen grootformaat extrusie 3D-printers te produceren voor gebruik in zijn fabrieken voor productie.
Hoewel de massaproductie van het voertuig later dit jaar zal beginnen, zijn er al pre-orders gedaan door de Italiaanse postdienst Post Italiane, die 5.000 aangepaste voertuigen in gebruik heeft genomen voor zijn activiteiten.
7. Meer maatwerk met 3D-printen
Met de groeiende vraag naar op maat gemaakte producten en gepersonaliseerde ervaringen, bieden autofabrikanten hun klanten steeds vaker de mogelijkheid om hun voertuigen aan te passen.
Een manier om deze aanpassing economisch haalbaar te maken, is met 3D-printen.
De oudste autofabrikant van Japan, Daihatsu, lanceerde in 2016 een voertuigaanpassingsproject voor zijn Copen-automodel.
In samenwerking met Stratasys kunnen Daihatsu-klanten op maat gemaakte 3D-geprinte panelen ontwerpen en bestellen voor hun voor- en achterbumpers, met een keuze uit meer dan 15 basispatronen in 10 verschillende kleuren.
De op maat gemaakte onderdelen worden bedrukt met ASA, een duurzame en UV-bestendige thermoplast, met behulp van Stratasys’ Fortus 3D-printers. De mogelijkheid om snel en kosteneffectief gepersonaliseerde, eenmalige ontwerpen te maken, was een van de belangrijkste redenen om voor 3D-printen te kiezen in plaats van traditionele processen.
In Europa implementeert Volkswagen nu HP's Metal Jet-technologie met het oog op op maat gemaakte metalen onderdelen zoals achterkleppen, versnellingspookknoppen en sleutelhangers.
Het bedrijf is van plan om zijn klanten de mogelijkheid te bieden om geïndividualiseerde belettering aan deze componenten toe te voegen. Volkswagen merkt ook op dat deze gepersonaliseerde componenten binnen de komende twee tot drie jaar zullen dienen als een proof of concept voor de ontwikkeling van 3D-geprinte structurele onderdelen voor zijn auto's.
Een voordeel van het gebruik van 3D-printen voor maatwerk is dat autofabrikanten hierdoor de doorlooptijden en productiekosten voor onderdelen met een klein volume kunnen verminderen. Dit komt deels omdat de technologie de noodzaak elimineert om individuele gereedschapshulpmiddelen te maken voor elk gepersonaliseerd onderdeel - een vooruitzicht dat financieel onhaalbaar zou zijn.
In de toekomst zullen autofabrikanten nog steeds meer use-cases moeten ontwikkelen voor op maat gemaakte 3D-geprinte componenten om verder te gaan dan eenvoudige trimonderdelen. Dat gezegd hebbende, naarmate de technologie vordert, lijken de mogelijkheden voor het aanpassen van auto's met 3D-printen de komende jaren in een veel sneller tempo uit te breiden.
Lees ook:3D-printen en massaaanpassing:waar zijn we vandaag?
8. Op jacht naar de overwinning:3D-printen voor motorsport
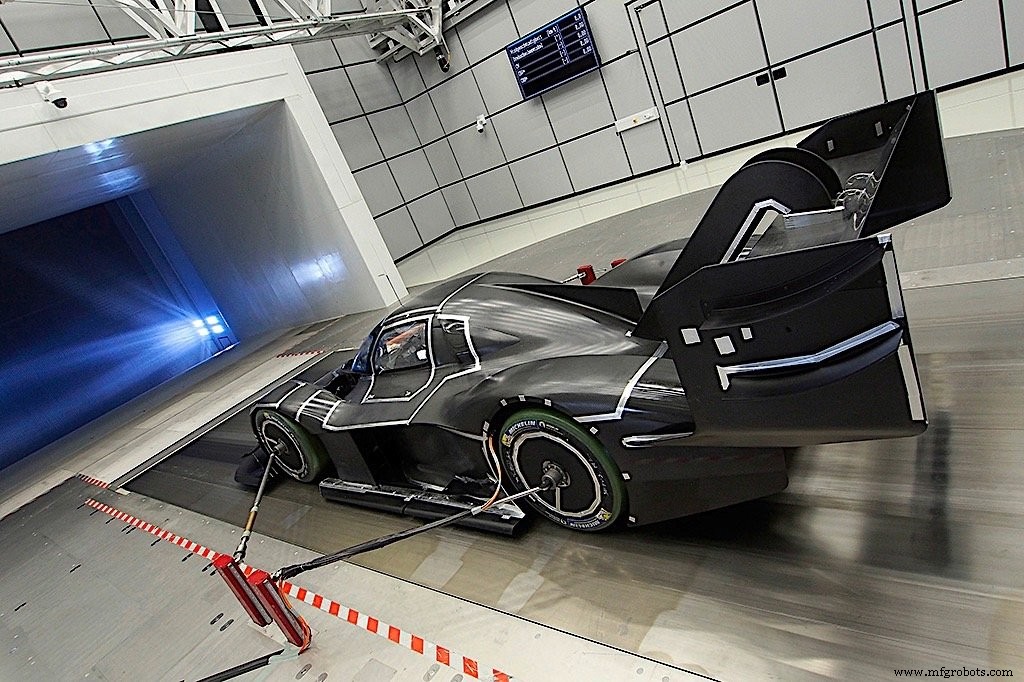
In Formule 1-races betekent de prestatie van een raceauto vaak het verschil tussen een overwinning of een verlies. Het bouwen van een succesvolle raceauto is echter een uitdaging, niet in de laatste plaats vanwege de hoge kosten en de snelle ontwikkelingscyclus die nodig is.
Windtunneltesten is een van de essentiële fasen van het ontwikkelingsproces van raceauto's.
Autofabrikanten gebruiken windtunnels om de aerodynamische eigenschappen van een raceauto te verifiëren en aan te passen. Tijdens de testfase in de windtunnel wordt een model van een auto op een loopband geplaatst om te testen hoe de auto zal presteren in een gesimuleerde race-omgeving.
Momenteel wordt 3D-printen het meest gebruikt in de autosport om onderdelen te maken die op deze replica raceauto kunnen worden getest. Het Zwitserse Alfa Romeo Sauber F1 Team zou bijvoorbeeld een 60% schaalmodel van een Formule 1-raceauto hebben gebruikt, waarbij veel van zijn componenten 3D zijn geprint met SLS- en SLA-technologieën.
Ingenieurs bij Sauber zijn in staat om onderdelen zoals voorvleugels, remleidingen, ophanging en motorkappen veel sneller en met een grotere ontwerpflexibiliteit te printen dan bij traditionele productie mogelijk zou zijn.
Een ander voorbeeld komt van Volkswagen Motorsport, dat 3D-printen gebruikte voor de ontwikkeling van zijn elektrische I.D. R Pikes Peak raceauto. Met slechts acht maanden om de auto te ontwikkelen, zet het Volkswagen-team in op 3D-printen om het proces te versnellen en de ontwikkelingsdeadlines te halen.
De technologie werd gebruikt om onderdelen te produceren voor het 50% schaalmodel van de I.D. R Pikes Peak-auto. Er zijn ongeveer 2.000 afzonderlijke onderdelen voor het windtunnelmodel vervaardigd, waarbij onderdelen binnen een paar dagen worden geproduceerd in plaats van de weken die nodig zijn voor CNC-bewerking of gieten.
Door een uiterst flexibel en zeer snel ontwikkelingsproces mogelijk te maken, heeft 3D-printen Volkswagen Motorsport geholpen om de auto op tijd op de weg te krijgen. En deze inspanning werd onlangs beloond:net vorig jaar werd de I.D. R Pikes Peak-raceauto vestigde een nieuw record voor de heuvelklim in Pikes Peak Racing.
Met bewezen effectiviteit bij het verkorten van ontwikkelingstijden, vindt 3D-printen nu zijn weg naar eindtoepassingen die raceteams aanzienlijke prestatievoordelen kunnen bieden.
9. 3D-printen reserveonderdelen voor klassieke auto's
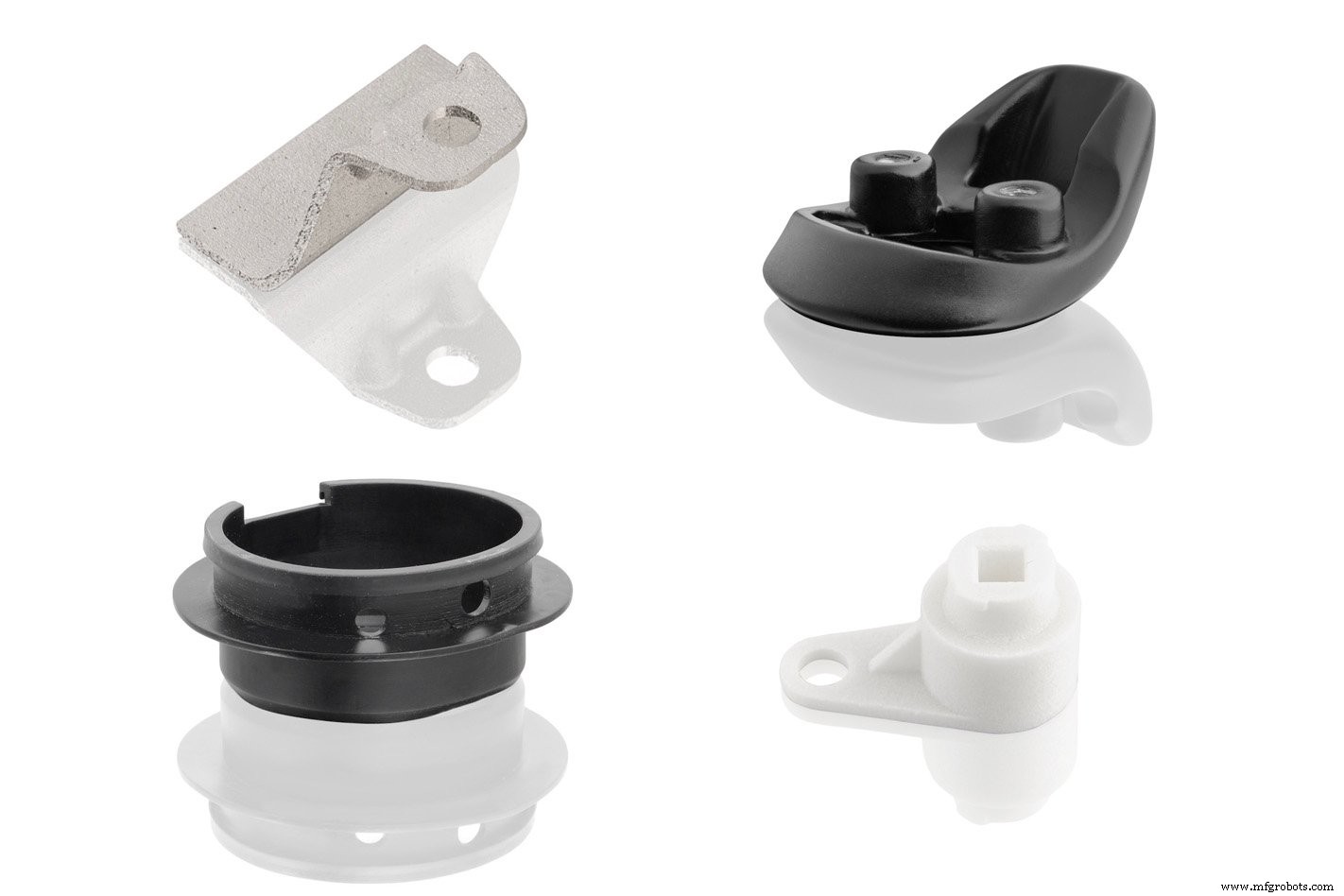
Reserveonderdelen zijn nog een andere toepassing van 3D-printen in de auto-industrie - en een Porsche Classic maakt daar ten volle gebruik van.
De afdeling van het Duitse autobedrijf levert onderdelen voor zijn vintage en niet meer geproduceerde modellen, en gebruikt 3D-printen om zeldzame reserveonderdelen in kleine oplagen te produceren voor zijn oudere inventaris.
Veel van deze onderdelen worden niet meer geproduceerd en het gereedschap dat nodig is om ze te vervaardigen bestaat niet of is in slechte staat. Het vervaardigen van nieuwe gereedschapshulpmiddelen met traditionele methoden is inherent onbetaalbaar, vooral gezien de lage volumes in kwestie.
Om deze uitdagingen op te lossen, is Porsche Classic begonnen deze onderdelen (in metaal en plastic) on demand in 3D te printen.
Het printproces omvat het smelten van het metaalpoeder (of sinteren voor kunststoffen) met een hoogenergetische laserstraal in een nauwkeurig patroon, waardoor het driedimensionale object laag voor laag wordt opgebouwd. Het voordeel is dat onderdelen kunnen worden gemaakt zonder extra gereedschap en alleen wanneer dat nodig is, waardoor Porsche kan besparen op gereedschaps- en opslagkosten die gepaard gaan met het maken van deze reserveonderdelen met behulp van conventionele methoden.
3D-printonderdelen die zelden worden besteld of niet meer worden geproduceerd, is een groeiende trend binnen de toeleveringsketen van de auto-industrie. Mercedes-Benz Trucks, Volkswagen en BMW omarmen ook 3D-printen voor deze toepassing, waardoor de autofabrikanten kosten kunnen besparen, de operationele efficiëntie kunnen verhogen en de voorraad kunnen optimaliseren.
Lees ook:Hoe 3D-printen de reserveonderdelenindustrie transformeert
10. Zullen toekomstige motorfietsen 3D-geprint worden?
Tot nu toe hebben we bedrijven gezien die onderdelen voor auto's en zelfs hele carrosserieën 3D-printen, maar hoe zit het met motorfietsen?
Hoewel er nog geen commercieel verkrijgbare 3D-geprinte fietsen op de weg zijn, zijn er een aantal projecten die een kijkje bieden in wat de toekomst van de motorfietsproductie zou kunnen zijn.
APWORKS' Light Rider is een van de bekendste voorbeelden van het potentieel van het gebruik van 3D-printen voor de productie van motorfietsen.
Het Duitse bedrijf onthulde de 3D-geprinte, topologisch geoptimaliseerde, elektrische motorfiets in 2016. De motorfiets toont ook de eigenschappen van het gepatenteerde Scalmalloy-materiaal van APWORKS. Met behulp van Scalmalloy is het 3D-geprinte motorfietsframe 30% lichter dan zijn traditioneel gemaakte tegenhangers.
Hoewel APWORKS enorm veel succes heeft geboekt met het project, met veel klanten die de Light Rider willen kopen, blijft het een uitdaging om de productie commercieel levensvatbaar te maken.
Een ander, recenter voorbeeld van een 3D-geprinte motorfiets is afkomstig van de Duitse FDM 3D-printerfabrikant BigRep.
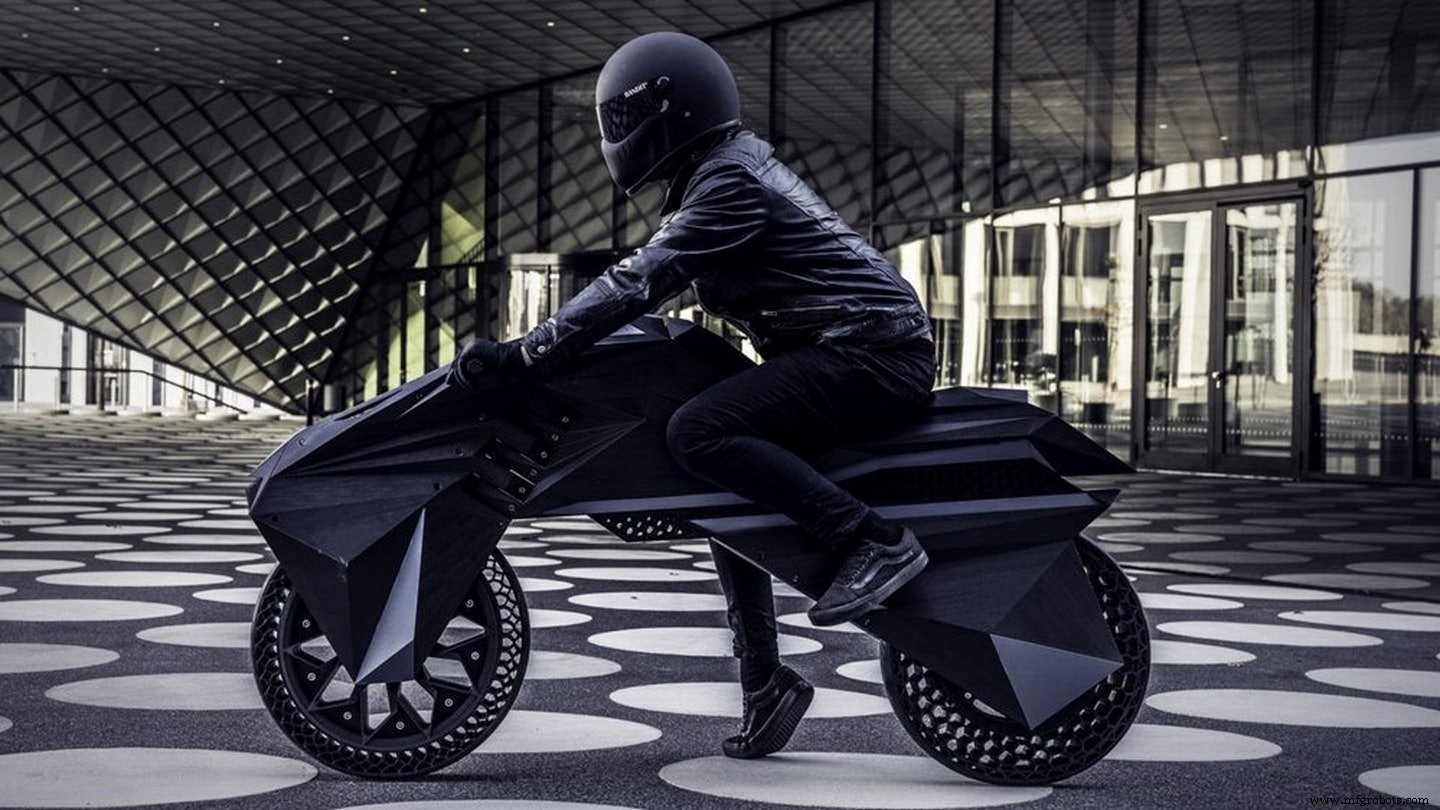
De NERA-motorfiets van het bedrijf - een volledig functioneel prototype - duurde slechts 12 weken om te produceren en was ontworpen om de mogelijkheden van 3D-printen te demonstreren.
Om het te maken, gebruikte BigRep zijn grootschalige 3D-printers en een reeks materialen, waaronder PLA, Pro FLEX (een op TPU gebaseerd flexibel materiaal) en het ProHT-filament van technische kwaliteit. Met uitzondering van de elektronica werden alle 15 onderdelen 3D-geprint, inclusief de velgen, frame, airless banden, zadel en een flexibele bumper.
Hoewel deze en andere projecten een opwindend kijkje bieden in het potentieel van 3D-printen voor motorfietsen, zal het nog geruime tijd duren voordat ze op de weg verschijnen. Maar het vermogen van 3D-printen om lichtgewicht onderdelen te maken, de prestaties te verbeteren en een snellere en goedkopere productie mogelijk te maken, maakt ons enthousiast over het toekomstige potentieel voor deze toepassing.
De toekomst van de autoproductie stimuleren
Hoewel deze lijst de belangrijkste toepassingsgebieden voor 3D-printen in de auto-industrie laat zien, is het slechts de oppervlakte van de mogelijkheden. Echter, aangezien autofabrikanten het potentieel van de technologie erkennen om een voorsprong op de concurrentie te bieden, zal het aantal toepassingen zeker toenemen.
Kijkend naar de toekomst van 3D-printen in de auto-industrie, zal de technologie blijven doordringen in productontwikkeling, productie, assemblage en de toeleveringsketen, waardoor nieuwe ontwerpen, concurrerende bedrijfsmodellen en, uiteindelijk, superieure voertuigen mogelijk worden.
3d printen
- De waarde van additieve productie in de auto-industrie
- Hoe digitalisering essentieel is voor de toekomst van medisch 3D-printen
- 4 manieren waarop 3D-printen de medische industrie transformeert
- Is de bouwsector klaar voor 3D-printen? (update 2020)
- 5 manieren waarop 3D-printen de elektronica-industrie kan transformeren
- Hoe verandert 3D-printen de defensie-industrie?
- Hoe verandert 3D-printen de auto-industrie? (2021)
- CNC-bewerking in de auto-industrie
- 5 manieren waarop 3D-printen de auto-industrie verandert
- Toepassing van 3D-printen in de auto-industrie
- Wat is de grafische industrie?