Kwaliteitsborging voor metaal 3D-printen:3 veelvoorkomende uitdagingen oplossen
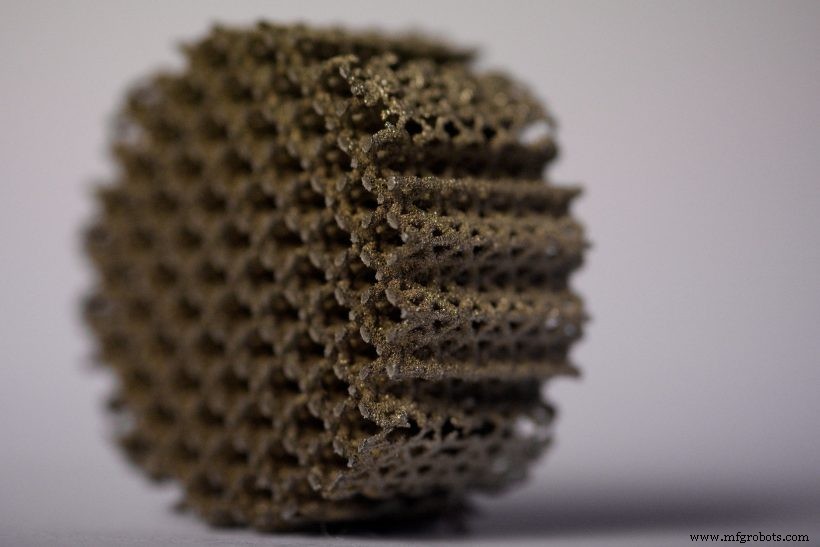
Kwaliteitsborging (QA) is misschien wel de belangrijkste en toch een van de meest uitdagende stappen in 3D-printen.
Omdat 3D-printen steeds vaker wordt gebruikt in hoogwaardige industriële toepassingen, moet de technologie consistent en betrouwbaar hoogwaardige onderdelen leveren met de eigenschappen die nodig zijn om aan veeleisende toepassingen te voldoen. Als het gaat om 3D-printen van metaal, is dit echter een voortdurende uitdaging geweest voor veel fabrikanten die in de technologie willen investeren.
Het artikel van vandaag gaat in op enkele van de belangrijkste uitdagingen waarmee bedrijven worden geconfronteerd wanneer ze om QA-processen voor metalen 3D-geprinte onderdelen vast te stellen en enkele van de beschikbare oplossingen te verkennen.
Uitdaging 1:Zorgen voor de kwaliteit van uw materialen
Ervoor zorgen dat een 3D-geprint onderdeel voldoet aan de normen van zeer veeleisende toepassingen, hangt sterk af van de kwaliteit van het gebruikte materiaal.
Materiaalkwalificatie is echter een voortdurende uitdaging voor bedrijven die metaalpoeders produceren of hanteren. Een factor die het proces bemoeilijkt, is de noodzaak om de zuiverheid van metaalpoeders die worden gebruikt voor additieve fabricage te behouden.
Dit is met name het geval voor veiligheidskritieke toepassingen, zoals vliegtuigonderdelen of medische apparaten, waarbij het materiaal gebruikt moet 100% vrij zijn van vervuiling. Onzuiverheden kunnen de eigenschappen van het uiteindelijke onderdeel veranderen, wat op zijn beurt kan leiden tot een mislukte afdruk.
Er zijn echter verschillende manieren waarop metaalpoeders besmet kunnen raken.
Het risico op besmetting kan bijvoorbeeld ontstaan tijdens het drukproces zelf of tijdens opslag, transport en handling. Om het eerste voorbeeld te nemen:er kan bijvoorbeeld wat residu van een ander poeder achterblijven op de bouwplaat, wat leidt tot het mengen van twee verschillende poeders. Het grondig reinigen van de bouwplaat na elke productierun is daarom een belangrijke preventieve stap.
Een ander risico ontstaat wanneer poeder, overgebleven uit het drukproces, wordt hergebruikt. Hoewel de mogelijkheid om poedermateriaal te hergebruiken kan helpen om verspilling te verminderen, is het belangrijk op te merken dat herhaaldelijk hergebruik van poeder op deze manier de samenstelling van de deeltjes kan veranderen, omdat vocht, zuurstof en stikstof worden geabsorbeerd.
Het is onvermijdelijk dat er testmethoden nodig zijn die geschikt zijn voor additive manufacturing om er zeker van te zijn dat er geen contaminatie is.
Oplossing:overweeg CT-scanning
Een van de meest nauwkeurige manieren om verontreiniging in metaalpoeders te detecteren, is door gebruik te maken van computertomografie (CT)-scanning.
Een CT-scanner werkt door honderden röntgenfoto's vanuit verschillende hoeken te maken, van waaruit een 3D-beeld wordt gemaakt. Moderne CT-scanners kunnen details tot drie micron vastleggen, met enkele microCT-scanners met hoge resolutie, die op een veel kleinere micrometerschaal werken en een voxelgrootte van 0,5 micron bereiken.
De huidige microCT-apparatuur kan metalen inspecteren variërend van aluminium en titanium tot zwaardere metaallegeringen zoals roestvrij staal en Inconel.
Wanneer ze worden gebruikt voor het kwalificeren van metaalpoeders voor 3D-printen, kunnen CT-scanners ingenieurs voorzien van diepgaande gegevens over de microstructuur van poeder. Deze gegevens kunnen worden gebruikt om verontreinigingen met vreemde deeltjes te detecteren, evenals om de deeltjesgrootte en vormverdelingen te meten en de porositeit in de deeltjes te detecteren. Het verkrijgen van deze informatie is een manier waarop ingenieurs de toepasbaarheid van het poeder voor productie kunnen bevestigen.
Een bedrijf dat CT-scandiensten levert voor additieve productie is Expanse Microtechnologies.
In een interview met AMFG merkt James Hinebaugh, president en mede-oprichter van het bedrijf op dat "Poeders het belangrijkste aandachtspunt zijn in de hele toeleveringsketen van additive manufacturing. Begrijpen wat een goed poeder maakt dat zich goed verspreidt en goed print, is een belangrijke zorg voor bedrijven.
“Het is belangrijk om te begrijpen 1) of er een ideale morfologie of een ideale grootte of morfologische distributie is die goed kan samenwerken met een grote verscheidenheid aan recoaters en printers, en 2) hoe we de defecten in poeders, zoals insluitsels en poreusheid binnen de deeltjes, kunnen verminderen die, zoals studies hebben aangetoond, vaak vast komen te zitten in een onderdeel en tijdens het printproces niet aan het onderdeel kunnen ontsnappen.”
Dit zijn de twee gebieden die Expanse Microtechnologies aanpakt met zijn gepatenteerde MicroCT-scanoplossing.
Het bedrijf heeft geavanceerde beeldverwerkingsmethoden ontwikkeld, van waaruit het in staat is om diepgaande rapporten te genereren over materiaalporositeit, deeltjes- en poriemorfologie, evenals de grootte- en vormverdelingen van deeltjes.
Met deze informatie kunnen gebruikers van additive manufacturing eventuele problemen met grondstoffen identificeren en de verbanden begrijpen tussen de materialen die ze gebruiken en het kwaliteitsniveau van de geprinte componenten.
Hoewel het testen en kwalificeren van grondstoffen voor additive manufacturing een uitdaging kan zijn, is het een van de belangrijkste stappen om de kwaliteit van een additief vervaardigd onderdeel te waarborgen. Momenteel biedt CT-scanning een van de meest robuuste en nuttige tools die kunnen worden gebruikt om onbewerkte AM-materialen te valideren.
Uitdaging 2:Procesbeheersing tot stand brengen
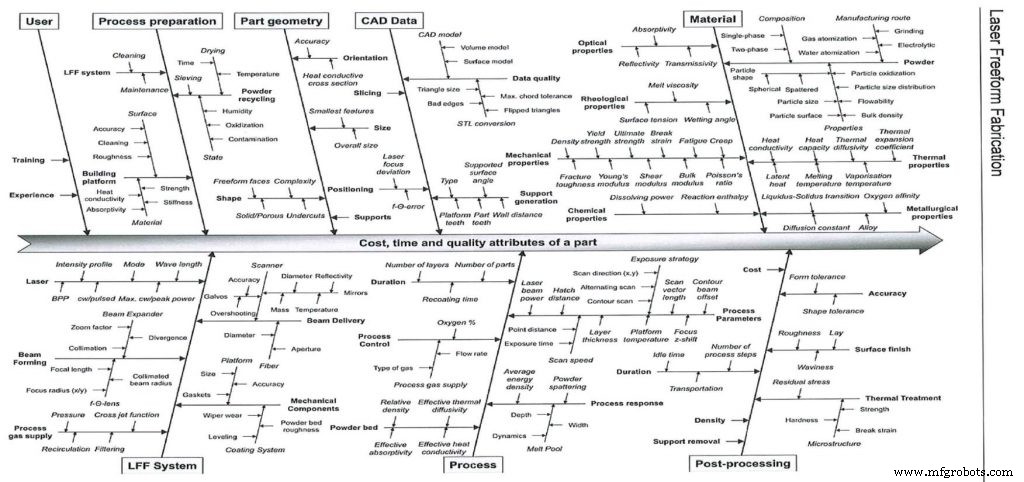
Als het gaat om 3D-printen van metaal - en met name poederbedfusietechnologieën - is er een breed scala aan variabelen die de vorm en structuur van een onderdeel kunnen beïnvloeden. Deze variabelen omvatten de hele AM-workflow, van ontwerp tot voorbereiding van de build en nabewerking.
Laten we het afdrukproces als voorbeeld nemen. Hier zijn slechts enkele van de parameters die het succes of falen van het proces bepalen, het pad en de intensiteit van de laser en de snelheid van het overcoaterblad van de printer. Andere factoren zijn onder meer het ontwerp van de ondersteunende structuren en zelfs subtiliteiten zoals het aantal keren dat het poeder is gerecycled.
Hoewel deze lijst niet eens in de buurt komt van volledig te zijn, heeft elke factor een impact op het resultaat van een constructie en afwijking op welke manier dan ook kan de kwaliteit van het uiteindelijke onderdeel beïnvloeden.
Momenteel is vallen en opstaan de meest gebruikelijke benadering om met het brede scala aan variabelen om te gaan om een proces te bereiken dat herhaalbare onderdelen. Dit kan echter inhouden dat het uiteindelijke onderdeel meerdere keren moet worden vervaardigd en dat het onderdeel zelf uitgebreid moet worden getest.
Natuurlijk is het toepassen van deze aanpak een zeer duur en inefficiënt proces, en doet het een van de belangrijkste voordelen van de technologie teniet:het kosteneffectief kunnen produceren van kleine batches onderdelen.
Bedrijven moeten daarom een meer duurzame en haalbare aanpak hanteren voor procesbeheersing en het kwalificeren van additief vervaardigde onderdelen.
Oplossing:ontwikkel een gesloten systeem voor kwaliteitscontrole
Drie elementen moeten samenkomen om een sneller, betrouwbaarder en duurzamer kwaliteitsborgingsproces voor 3D-geprinte onderdelen mogelijk te maken. Dit omvat buildplanning, buildmonitoring en feedbackcontrole.
- De bouw plannen
Een manier om het afdrukproces beter te begrijpen, is door middel van simulatie. Met behulp van simulatie kunnen ingenieurs testen hoe een onderdeel zich zal gedragen in een virtuele, digitale omgeving voordat een ontwerp wordt verzonden om te printen.
Door het AM-proces te simuleren, kunnen ingenieurs de complexe processen analyseren die plaatsvinden tijdens het printproces.
Omdat 3D-printen van metaal gevoelig is voor problemen als kromtrekken en vervorming, biedt simulatie belangrijke inzichten in hoe een onderdeel bijvoorbeeld tijdens het printproces zal vervormen. Een ander voorbeeld is het gebruik van simulatie om precies te bepalen hoe het materiaal zal smelten en stollen.
Ingenieurs kunnen deze gegevens vervolgens gebruiken om de bouw te plannen en de meest succesvolle onderdeeloriëntatie en ondersteuningsstrategieën te selecteren.
Dat gezegd hebbende, simulatiesoftware heeft zijn beperkingen. “Alle simulatiesoftware heeft tegenwoordig een bepaald niveau van aannames ingebouwd die de nauwkeurigheid die het kan leveren, beperken. Dat is op dit moment waarschijnlijk het grootste nadeel:ze kunnen niet zo nauwkeurig zijn als je zou willen", zegt Dave Conover, Chief Technologist van ANSYS, in een recent interview met AMFG.
De simulatietechnologie evolueert echter snel, waarbij softwareleveranciers hun aanbod blijven verfijnen. Uiteindelijk zal het integreren van simulatiesoftware in de ontwerp- en planningsfase helpen om trial-and-error te elimineren, terwijl de kans op printfouten aanzienlijk wordt verkleind.
- De build volgen
In-procesbewakingssystemen kunnen het onderdeelkwalificatieproces verder ondersteunen. Sensoren en camera's kunnen worden gebruikt om meerdere aspecten van de bouw in realtime te meten, om het bouwproces te documenteren en ervoor te zorgen dat aan de vereisten wordt voldaan.
Met poederbed AM-processen kunnen camera's de grootte en temperatuur van het smeltbad vastleggen, wat een directe invloed heeft op de microstructuur, materiaaleigenschappen, oppervlakteafwerking en algehele prestaties van onderdelen.
Ingenieurs kan deze gegevens vervolgens gebruiken om de kans op defecten, zoals kromtrekken of scheuren, te voorspellen en ruim voordat de defecten optreden in het proces ingrijpen. Aangezien deze gegevens zijn gedocumenteerd, kan dit helpen om de procesomstandigheden te vermijden die in de toekomst tot deze defecten kunnen leiden.
Momenteel is er een beperkt aantal in-process bewakingstechnologieën geoptimaliseerd voor AM.
Sigma Labs is een bedrijf dat een oplossing biedt voor in-process AM-kwaliteitsborging. Het PrintRite3D-kwaliteitsborgingssysteem voor additive manufacturing combineert PrintRite3D SENSORPAK-multisensoren en hardware met een PrintRite3D INSPECT-softwaremodule.
Deze veelzijdige combinatie, gedeponeerd als IPQA-technologie, maakt het mogelijk om smeltbadomstandigheden te optimaliseren tijdens het AM-proces, met behulp van sensorgegevens en het vaststellen van in-process kwaliteitsstatistieken. Met behulp van statistische analyse van procesgegevens kan rapportage over de kwaliteit van onderdelen worden gegenereerd en gebruikt om de herhaalbaarheid te valideren.
In de toekomst is het bedrijf van plan een ANALYTICS-softwaremodule toe te voegen, gericht op het benutten van Big Data-analyse. De module zal in staat zijn om zinvolle en bruikbare informatie te extraheren uit de gegevens die tijdens het printproces zijn verzameld om de kwaliteitscontrole tijdens het proces verder te vereenvoudigen.
Wat betreft de 3D-printers zelf, sommige hebben al ingebouwde bewakingsfuncties. 3D-printerfabrikant EOS biedt bijvoorbeeld de EOSTATE-monitoringsuite aan. De hardware- en softwareoplossing is gebaseerd op vier verschillende monitoringmodules, waaronder System and Laser, PowderBed, MeltPool en Exposure OT (optische tomografie), die kwaliteitsrelevante gegevens in realtime kunnen vastleggen.
Met EOSTATE Exposure OT beweert EOS de enige fabrikant te zijn van metaalpoederbedsystemen die zijn klanten een kwaliteitsborgingsinstrument biedt dat optische tomografie omvat.
Dit monitoringsysteem maakt gebruik van een camera die lichtemissies in het nabij-infraroodspectrum verzamelt, vergelijkbaar met een warmtebeeldcamera. Het kan elk onderdeel tijdens het bouwproces volledig in kaart brengen, laag voor laag, ongeacht de geometrie en grootte. Met deze aanpak kunnen ingenieurs het bereik van detecteerbare fenomenen die relevant zijn voor de kwaliteit van AM-onderdelen uitbreiden.
MTU Aero Engines is een bedrijf dat deze monitoringoplossing al is gaan gebruiken in hun seriële productielijnen voor AM onderdelen voor vliegtuigmotoren.
- De cirkel sluiten
Het detecteren en documenteren van de parameters tijdens het printproces is cruciaal. Maar de mogelijkheid om in realtime op deze informatie te reageren - een proces dat bekend staat als feedbackcontrole - maakt deze aanpak nog effectiever.
Feedback-controle, ook wel een closed-loop-systeem genoemd, verwijst naar de mogelijkheid om afwijkingen tijdens het printproces te detecteren en het systeem automatisch aan te passen om deze te compenseren. Door de controle over het bouwproces te behouden, kunnen fabrikanten consistente geometrieën, oppervlakteafwerkingen en materiaaleigenschappen bereiken die de kwaliteit ondersteunen.
Een bedrijf dat een feedbackgestuurd AM-proces heeft ontwikkeld, is Velo3D. Na meer dan $ 92 miljoen aan financiering te hebben opgehaald, verscheen Velo3D afgelopen zomer met de release als zijn end-to-end metal AM-oplossing. Het omvat de Velo3D Sapphire 3D-printer, de Flow printvoorbereidingssoftware en wat het bedrijf Intelligent Fusion-technologie noemt.
Met deze belangrijke elementen nauw met elkaar geïntegreerd, maakt de technologie thermische processimulatie, voorspelling van printprestaties en closed-loop controleverwerking mogelijk. Als gevolg hiervan kan het Sapphire-systeem herhaaldelijk en consistent onderdelen produceren met uitdagende geometrieën, zoals uitsteeklengtes met vrijwel geen ondersteunende structuren.
Velo3D's Flow-software speelt een integrale rol bij het mogelijk maken van deze voordelen. De software voert een pre-print simulatie en correctie uit, optimaliseert het ontwerp en past de geometrie en onderdeeloriëntatie aan. Dit helpt bij het voorbereiden van het bestand, waarbij eventuele vervormingen worden gecompenseerd, zodat het onderdeel er correct uitkomt. In-situ procesmetrologie vergezeld van closed-loop smeltbadcontrole werkt samen met software, waardoor het succes van het eerste deel uiteindelijk wordt verhoogd tot meer dan 90%.
Uitdaging 3:Het verminderen van menselijke fouten
Menselijke fouten zijn misschien wel de grootste risicofactor om ervoor te zorgen dat een 3D-geprint onderdeel aan alle vereiste normen voldoet.
Dit komt omdat 3D-printen nog steeds meer menselijke tussenkomst vereist dan je zou verwachten, van het ontwerpen en verwijderen van dragers tot nabewerking en het handmatig controleren of in elke fase aan de vereisten wordt voldaan.
Dit niveau van menselijke tussenkomst verhoogt onvermijdelijk het risico dat het laatste deel wordt aangetast.
Laten we de postproductiefase als voorbeeld nemen.
Zodra een build is voltooid, moet deze worden uitgepakt en moeten de verschillende onderdelen die in die build zijn afgedrukt, worden geïdentificeerd en geïnspecteerd voordat ze worden verzonden voor nabewerking.
De productie-engineer die deze taak uitvoert, moet doorgaans verwijzen naar een afgedrukt werkbriefje, in wezen een 2D-afbeelding afstemmen op zijn fysieke tegenhanger en een lijst met vereisten handmatig afvinken.
Deze benadering van inspectie is niet alleen tijdrovend, maar verwijdert ook de zichtbaarheid van de workflow uit de vergelijking.
Toch vinden veel bedrijven die AM gebruiken het een uitdaging om de handleiding te transformeren taken betrokken in een sneller, nauwkeuriger, geautomatiseerd proces.
Omdat het verkleinen van de kans op menselijke fouten zo belangrijk is om de kwaliteit van 3D-geprinte onderdelen te waarborgen, is een manier om dit te bereiken het gebruik van digitale methoden om zoveel mogelijk van de inspectiestappen te automatiseren.
Oplossing:werkstroomsoftware implementeren voor additieve productie
Workflowsoftware biedt een digitaal, gecentraliseerd platform om project- en productieteams te helpen bij het beheren van hun AM-productieprocessen.
In de context van kwaliteitsborging kan workflowsoftware vaak het complete raamwerk bieden om bedrijven te helpen ervoor te zorgen dat aan alle onderdelen wordt voldaan.
Bovendien kunnen productiemanagers workflowsoftware gebruiken om het proces van het inspecteren van onderdelen papierloos en traceerbaar te maken. In plaats van elk onderdeel handmatig te inspecteren, met het werkbriefje in de hand, kunnen fysieke onderdelen worden vergeleken met hun 3D, digitale tegenhangers.
De post-productiebeheertool van AMFG biedt bijvoorbeeld een 3D-viewer, die alle onderdeelgegevens bevat, zodat gebruikers een onderdeel en de eigenschappen ervan nauwkeuriger kunnen inspecteren.
Met de tool kunnen gebruikers de verhouding tussen succesvolle en mislukte onderdelen volgen. Onderdelen die als mislukt zijn gemarkeerd, worden automatisch teruggestuurd naar de interne productiewachtrij van het platform om te worden gereproduceerd. Het grootste voordeel hiervan is dat gebruikers elke actie die op een onderdeel wordt uitgevoerd, kunnen volgen, waardoor traceerbaarheid en verantwoording worden toegevoegd aan de behoefte aan kwaliteitsbeheer.
Zijn er branchebrede kwaliteitsnormen voor AM?
Tot dusverre hebben we gezien dat inzicht in het kwalificeren van processen, materialen en het implementeren van digitale strategieën essentieel is om ervoor te zorgen dat bedrijven kunnen profiteren van 3D-printen voor productie.
Industriebrede normen zullen een sleutelrol spelen bij dit proces. Met traditionele productie zijn normen al gemeengoed, waardoor bedrijven de kwaliteit van hun producten kunnen waarborgen en een gemeenschappelijke basis kunnen vinden. Natuurlijk heeft de traditionele productie decennia, zo niet eeuwen, gehad om relevante normen te ontwikkelen.
3D-printen is daarentegen nog een relatief nieuw proces en veel normen en certificeringen zijn nog in ontwikkeling. In de toekomst zal de industrie testmethoden, protocollen en referentiegegevens moeten ontwikkelen om de kosten en tijd te verminderen om AM-materialen, -processen en -onderdelen te kwalificeren.
Gelukkig is dit een gebied dat zich snel ontwikkelt. Vorig jaar publiceerde AMST International zijn F3303-standaard, die manieren beschrijft om machines en processen te kwalificeren die worden gebruikt om onderdelen te bouwen met behulp van laser- of elektronenstraalpoederbedfusie. Er werd ook opgemerkt dat er al een aanvullende norm is om de kwalificatie van onderdelen, kwaliteitsborging en nabewerking van poederbedfusieonderdelen te ondersteunen.
Naast ASTM International werkt het National Institute of Standards and Technology (NIST) aan de ontwikkeling van QA-standaarden voor de AM-industrie. NIST lanceerde bijvoorbeeld het AM Part Qualification-project, gericht op "de metingen, methoden en metrologische systemen die nodig zijn om robuuste post-process metingen te creëren, een goed begrip van mechanische prestaties te ontwikkelen en AM-onderdelen te kwalificeren".
Kwaliteit in de gaten houden
Het waarborgen van materiaalkwaliteit en procesbeheersing zijn cruciaal voor het produceren van metalen onderdelen van constante hoge kwaliteit met 3D-printen.
Hoe ingewikkeld dit op het eerste gezicht ook mag lijken, fabrikanten kunnen hun hart ophalen, aangezien er oplossingen bestaan om het kwaliteitsborgingsproces te ondersteunen, ondersteund door de voortdurende ontwikkeling van industriebrede normen.
Door deze uitdagingen aan te gaan en de juiste oplossingen voor uw bedrijf strategisch te implementeren, kunt u aanzienlijk profiteren van de voordelen van 3D-printen voor hoogwaardige, veeleisende toepassingen.
3d printen
- Vuurvaste metaalpoeders zullen naar verwachting grondstoffen worden voor 3D-printen
- Vuurvaste metaalpoeders VS 3D-afdruktechnologie
- Overwegend wat nieuwe metaalprinttechnologie betekent voor AM
- Realtime kwaliteitscontrole:welk systeem is geschikt voor u?
- Ondersteunende structuren voor 3D-printen met metaal — een eenvoudigere aanpak
- H.C. Starck's AMPERPRINT:een nieuwe tool voor 3D-printen van metaal
- Welke metalen 3D-printpoeders kun je gebruiken in 2020? [Gids]
- 6 belangrijke ontwerpoverwegingen voor 3D-metaalprinten
- Scalmalloy:het nieuwste hoogwaardige materiaal voor 3D-metaalprinten
- Ontwerptips voor Direct Metal Laser Sintering 3D Printing
- Technologieoverzicht:wanneer u echt voor metaal 3D-printen moet gaan