3D-printen met polymeren:alles wat u moet weten in 2021
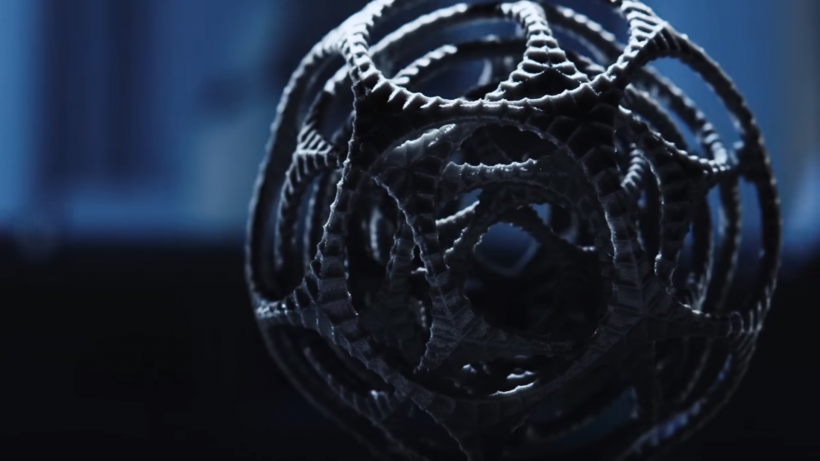
Een diepe duik in 3D-printen met polymeren:technologieën, veelbelovende ontwikkelingen, toepassingen en meer.
Nu grote chemische bedrijven toetreden tot de wereld van 3D-printen en steunpilaren van de industrie de mogelijkheden van de technologie verder ontwikkelen, krijgt 3D-printen met polymeren een enorme boost.
Om op de hoogte te blijven van de laatste ontwikkelingen, duiken we hieronder in de meest opwindende innovaties op het gebied van polymeer 3D-printen en de mogelijkheden die de technologie biedt. Maar laten we eerst eens kijken naar de algemene 3D-printtechnieken voor polymeren die in verschillende sectoren worden gebruikt.
Polymeer 3D-printen:de technologieën
Polymeer 3D-printers domineren de hardware-arena voor 3D-printen. Ze leiden op alle fronten:inkomsten uit zendingen, de installed base en het aantal ontwikkelingen dat in deze ruimte plaatsvindt.
Er werd voorspeld dat 3D-printen met polymeren in 2020 $ 11,7 miljard aan inkomsten zou hebben gegenereerd, een cijfer dat de verkoop van hardware, materialen en 3D-geprinte onderdelen samen omvat.
Hieronder bekijken we de belangrijkste technologieën die deze groei stimuleren.
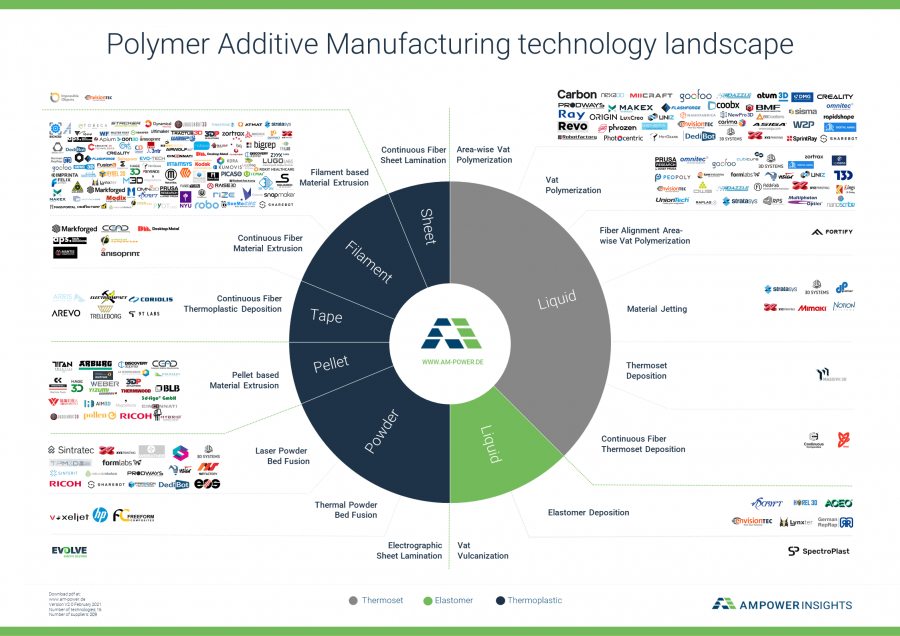
Vt-polymerisatie
Stereolithografie
De opkomst van stereolithografie (SLA) in de jaren tachtig markeerde het begin van het 3D-printtijdperk. SLA is een ideale technologie voor het produceren van fantastisch uitziende onderdelen met een uitstekende oppervlakteafwerking. Vanwege de nauwkeurigheid en hoge resolutie worden SLA-onderdelen meestal gebruikt voor vorm- en pasvormconceptmodellen of als basispatronen voor vormtoepassingen.
SLA is gebaseerd op vloeibare foto-uithardbare harsen. Deze worden door een UV-laser laag voor laag selectief uitgehard, waardoor de hars stolt.
Hoewel SLA-onderdelen een geweldige oppervlakteafwerking bieden, zijn ze doorgaans minder duurzaam dan onderdelen die met andere additieve technologieën zijn geproduceerd. Omdat SLA-materialen gevoelig zijn voor UV-licht, kunnen hun mechanische eigenschappen ook veranderen als gevolg van overmatige blootstelling aan zonlicht, waardoor ze ongeschikt zijn voor gebruik buitenshuis.
SLA-fotopolymeren zijn verkrijgbaar in verschillende kleuropties en in verschillende speciale materialen (gietbaar, duurzaam, hoge temperatuur, medische kwaliteit).
De materiaalkeuze voor SLA breidt zich voortdurend uit. In de afgelopen 12 maanden hebben we meerdere aankondigingen gehoord over nieuwe 3D-printharsen van onder meer Formlabs, Henkel, Zortrax, DSM en nog veel meer.
Wat uit het recente nieuws kan worden afgeleid, is dat de ontwikkeling van hars voor 3D-printen een nieuw niveau heeft bereikt:bedrijven zijn extreem gericht op geavanceerde toepassingen, met name op medisch, tandheelkundig en technisch gebied.
Lees ook:3D-printen voor productie van digitale tandheelkunde en heldere uitlijners
Materiaal extrusie
FDM/FFF
Fused Deposition Modeling (FDM), ook wel fused filament fabricage (FFF) genoemd, is een van de meest populaire 3D-printmethoden voor industrieel gebruik. Volgens een marktonderzoeksbureau, CONTEXT, kwamen de grootste inkomsten uit verzendingen in 2020 uit deze categorie machines, tot bijna $ 150 miljoen.
FDM werd in de jaren negentig commercieel beschikbaar en diende als een betaalbare en gebruiksvriendelijke prototyping-technologie. Sindsdien is FDM geëvolueerd om een grotere betrouwbaarheid, nauwkeurigheid en materiaalkeuze te bieden, waardoor het geschikt is voor een aantal productietoepassingen, zoals fabricagehulpmiddelen.
Lees ook:3D-printen voor vliegtuigcabines
FDM gebruikt thermoplastische filamenten die laag voor laag door een mondstuk op het printplatform worden geëxtrudeerd. Een van de belangrijkste beperkingen van FDM-onderdelen is anisotropie, wat betekent dat hun mechanische eigenschappen niet in alle ruimtelijke dimensies gelijk zijn. Dit kan resulteren in zwakkere onderdelen.
Bovendien heeft FDM een lagere afdruksnelheid in vergelijking met andere 3D-technologieën zoals SLS of SLA, waardoor het over het algemeen onpraktisch is voor serieproductie.
Tegenwoordig hebben fabrikanten een verscheidenheid aan FDM-filamenten tot hun beschikking, van elastische TPU tot duurzaam en versterkt ABS en hoogwaardige materialen zoals PEEK. Met de beschikbaarheid van productiekwaliteit thermoplasten, is FDM ideaal voor het produceren van functionele, duurzame producten.
Poederbed Fusion
Selectief laser sinteren
Selective Laser Sintering (SLS) is een additief fabricageproces waarbij plastic poedermateriaal wordt versmolten met behulp van een krachtige laser. Met een combinatie van hoge nauwkeurigheid, snelheid, betrouwbaarheid en gebrek aan ondersteunende structuren, wordt SLS zowel gebruikt voor functionele prototyping als voor productie in kleine volumes.
SLS gebruikt doorgaans polyamide (nylon) poeders, waarbij PA11 en PA12 de twee meest gebruikte polyamiden zijn, naast flexibel TPU-materiaal.
Bedrijven voegen echter voortdurend nieuwe materiaalaanbiedingen toe. In 2018 bracht Evonik bijvoorbeeld 's werelds eerste flexibele plastic PEBA-gebaseerde (polyetherblokamide) poeder voor SLS op de markt.
De Duitse 3D-printerfabrikant EOS heeft naast het gecertificeerde PEEK-materiaal ook met koolstofvezel versterkt PEKK-thermoplast beschikbaar gesteld voor zijn SLS-systemen. De nieuwe PEKK thermoplast zou aluminium onderdelen in de ruimtevaart en industriële toepassingen kunnen vervangen.
Met name EOS is momenteel de enige fabrikant die een SLS-systeem aanbiedt dat in staat is om hoogwaardige thermoplasten zoals PEEK en PEKK te verwerken - de EOS P800.
Historisch gezien was SLS-technologie duurder voor bedrijven om te verwerven (kosten in de honderdduizenden dollars). In 2014 liep het patent voor de technologie echter af, waardoor er meer betaalbare alternatieven ontstonden, zoals de Formlabs Fuse 1 benchtop 3D-printer.
Multi Jet Fusion
Sinds de introductie op de markt in 2016 heeft HP's Multi Jet Fusion (MJF) een nieuwe dimensie geopend voor de productie van functionele onderdelen en prototypes van industriële kwaliteit.
Net als SLS maakt de technologie gebruik van nylonpoeders. In plaats van lasers te gebruiken, werkt MJF door een smeltmiddel op elke laag poeder te laten vallen, dat vervolgens wordt versmolten door een infraroodlichtbron.
In vergelijking met SLS biedt MJF een snellere workflow dankzij HP's innovatieve nabewerkingsstation, dat het koelproces versnelt en helpt bij het verwijderen van poeder. De Jet Fusion 300/500-serie biedt ook full-colour 3D-printmogelijkheden.
Er zijn een paar beperkingen met HP's Multi Jet Fusion, bijvoorbeeld de momenteel beperkte materiaalkeuze (PA11, PA12, PA12 gevuld met glasparels).
HP promoot echter een Open Platform-model, dat samenwerking met materiaalontwikkelaars aanmoedigt. Door deze aanpak werkt HP samen met meer dan 50 bedrijven, waaronder Evonik, BASF en Lubrizol, die werken aan de ontwikkeling van nieuwe materialen die geschikt zijn voor de technologie.
Lees ook:
–De evolutie van HP's 3D-printtechnologie:van polymeer tot metaal AM
–AMFG- en HP-compatibiliteit zorgt voor AM-systeemconnectiviteit
Materiaalspuiten
Material Jetting is een inkjetprintproces waarbij een vloeibaar, fotoreactief materiaal laag voor laag op een bouwplatform wordt gedeponeerd. Net als bij SLA maakt Material Jetting gebruik van harsen, die stollen onder een UV-licht.
Een van de belangrijkste voordelen van Material Jetting is de mogelijkheid om tijdens het printproces twee of meer fotopolymeren te combineren, wat resulteert in een onderdeel met hybride eigenschappen (bijvoorbeeld het combineren van stijfheid met flexibiliteit). Bovendien is de technologie in staat om full-colour onderdelen te produceren, wat het ideaal maakt voor prototypes met een eindproduct-look.
Harsen die worden gebruikt in Material Jetting zijn vergelijkbaar met die gebruikt in SLA, maar hebben een minder viskeuze, inktachtige vorm. Hun kosten zijn doorgaans ook hoger.
Een van de beperkingen van de technologie zijn de slechte mechanische eigenschappen van de bedrukte onderdelen, waardoor onderdelen die met materiaal worden gespoten over het algemeen ongeschikt zijn voor functionele toepassingen.
Polymeer 3D-printen:de kansen en toepassingen
Industrieel 3D-printen met polymeermaterialen ontsluit een breed scala aan mogelijkheden voor zowel productie- als productontwikkelingsafdelingen. Hieronder hebben we de meest prominente van hen geschetst.
Snel prototypen
Prototyping blijft een van de belangrijkste toepassingsgebieden voor 3D-printen met polymeren. Met de evolutie van 3D-printtechnologieën kunnen prototypes nu veel sneller worden geproduceerd, ze zijn duurzamer en visueel aantrekkelijker.
De auto-industrie, die naar verluidt in 2017 het grootste aantal printers heeft gekocht, is een prominente gebruiker van 3D-printen met polymeren voor prototyping-doeleinden. Hier worden allerlei 3D-printtechnologieën ingezet, zowel voor vorm en pasvorm, als voor functioneel, testen en valideren.
Een voorbeeld is Audi, dat de J750 PolyJet 3D-printer van Stratasys gebruikt om onderdelen, zoals achterlichtkappen, voor zijn auto's te ontwerpen en te valideren.
Als een full-colour proces met meerdere materialen, maakt Stratasys Polyjet 3D-printen het mogelijk om fysieke prototypes te bouwen met de uiteindelijke productlook, waardoor het productontwikkelingsproces aanzienlijk wordt vereenvoudigd en versneld.
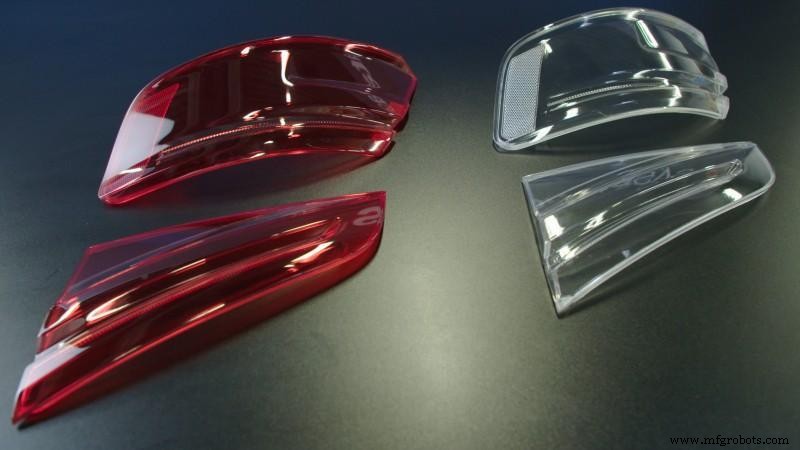
In de motorsportsector is 3D-printen een go-to-technologie als het gaat om het produceren van functionele onderdelen voor het testen van racewagens. Het Alfa Romeo Sauber F1-team maakt bijvoorbeeld veelvuldig gebruik van SLS- en SLA 3D-printen om onderdelen te produceren, waaronder voorvleugels, remleidingen en ophangingsafdekkingen, evenals motorafdekkingen, interne leidingen en handgeleiders voor automodellen in de windtunnel.
Efficiëntere tooling
3D-printen voor tooling is naar voren gekomen als een van de meest veelbelovende toepassingen van de technologie. Van mallen en armaturen tot investeringsgietpatronen, polymeer 3D-printen opent de deur naar snellere, goedkopere en op maat gemaakte gereedschappen.
Over het algemeen wenden bedrijven zich tot FDM- en SLA-technologieën om tooling te produceren vanwege hun relatieve betaalbaarheid en gebruiksgemak.
Autofabrikant Ford zou Ultimaker FDM 3D-printers gebruiken om aangepaste tools te maken.
De voordelen gaan ook verder dan de betaalbaarheid. Volgens de technisch leider van Ford, Harold Sears, is 3D-printen "mensen helpen hun werk te doen door gereedschappen te maken die ergonomischer zijn voor operators. Dit is misschien een klein voordeel, maar het is zeker nuttig als operators gelukkiger en comfortabeler hun werk doen. Ze zullen ook beter werk leveren, wat de kwaliteit alleen maar verbetert.”
Bovendien zijn de momenteel beschikbare 3D-printbare thermoplastische materialen soms zelfs sterk genoeg om metalen gereedschappen te vervangen, wat het assemblageproces een stuk eenvoudiger maakt en de kosten van het aangepaste gereedschap verlaagt.
Medische toepassingen
De medische industrie was een van de early adopters van polymeer 3D-printen. Tegenwoordig heeft de technologie een aantal toepassingen gevonden in de sector, van 3D-geprinte chirurgische handleidingen en hulpmiddelen tot replica's van menselijke organen voor preoperatieve planning.
In toenemende mate wordt 3D-printen gebruikt om direct medische hulpmiddelen op maat te produceren, waaronder goedkope protheses en tandheelkundige hulpmiddelen zoals aliners en bruggen.
Een van de sectoren van de industrie die volledig is getransformeerd door 3D-printen, zijn hoortoestellen. Tegenwoordig wordt meer dan 90% van de hoortoestellen wereldwijd vervaardigd met behulp van SLA 3D-printtechnologie.
Sinds het uitbreken van de pandemie heeft 3D-printen met polymeren zich ook bewezen als een levensvatbare technologie voor de productie van ventilatorkleppen, veiligheidsbrillen, gezichtsbescherming en teststaafjes.
Lees ook:3D-printen in de gezondheidszorg:waar staan we in 2021?
Consumentenproducten op maat
Bedrijven in consumentengoederen zien steeds vaker plastic 3D-printen als een optie voor massa-aanpassing. Omdat 3D-printen geen arbeidsintensieve en dure tooling vereist en complexe objecten kosteneffectief kan maken, maakt het de productie van gepersonaliseerde producten op maat van de consument mogelijk.
Een merk dat 3D-printen onderzoekt, is Dr. Scholl's, de leverancier van voetverzorgingsproducten. Het werkt samen met technologiebedrijf Wiivv om op maat gemaakte 3D-geprinte inzetstukken te maken.
Met behulp van Wiivv Fit-technologie biedt Dr. Scholl's een aanpassingsapp, die 400 punten op de voeten van elke gebruiker in kaart brengt met een paar telefoonfoto's. Hoewel dit proces, dat minder dan vijf minuten duurt, inlegvellen kunnen worden ontworpen en vervolgens afgedrukt volgens de exacte specificaties van de voeten van de klant.
Lees ook:
• 3D-printen voor schoenen
• 5 manieren waarop 3D-printen de consumentengoederenindustrie ten goede kan komen
Spannende technologische ontwikkelingen in polymeer 3D-printen
De 3D-printindustrie maakt grote sprongen in het ontwikkelen van nieuwe polymere 3D-printtechnologieën en het verbeteren van bestaande. Hieronder hebben we de recente belangrijkste technologische ontwikkelingen op het gebied van polymeer 3D-printen geschetst.
EOS' nieuwe LaserProFusion-technologie
De LaserProFusion-technologie van EOS, aangekondigd op Formnext 2018, is een innovatieve polymeer 3D-printtechnologie die wordt ontwikkeld om seriële additieve productie mogelijk te maken. Het proces is afhankelijk van maximaal een miljoen diodelasers die een uitgangsvermogen van maximaal 5 kW kunnen bereiken om plastic materialen te printen.
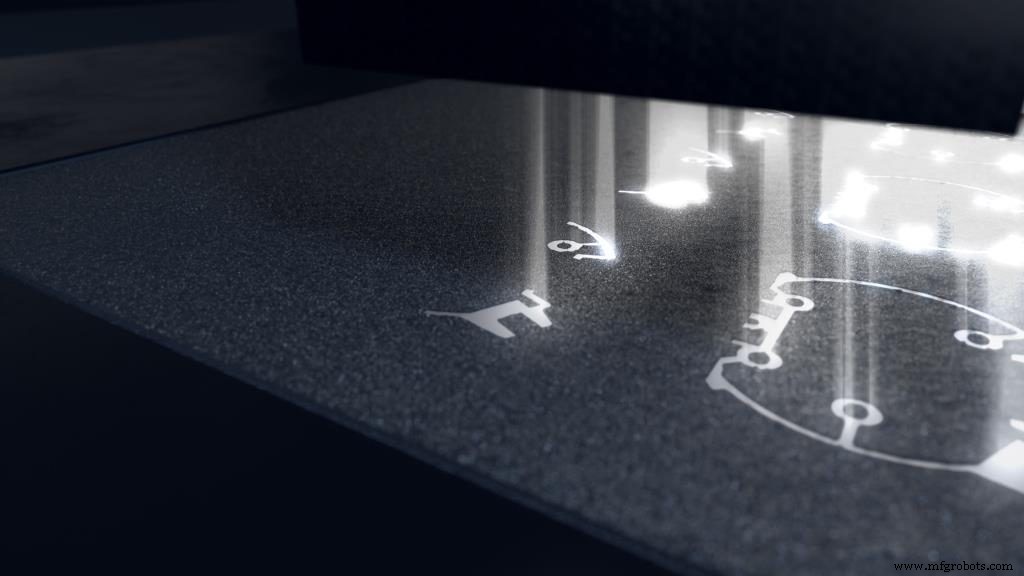
Met deze technologie zou het fabricageproces tien keer sneller zijn, waardoor hetzelfde productiviteitsniveau wordt bereikt als bij spuitgieten.
Hoewel het onduidelijk is wanneer het systeem commercieel beschikbaar komt, is de aankondiging de zoveelste indicator van de industrialisatie van 3D-printtechnologieën.
Hoge snelheid fotopolymerisatie
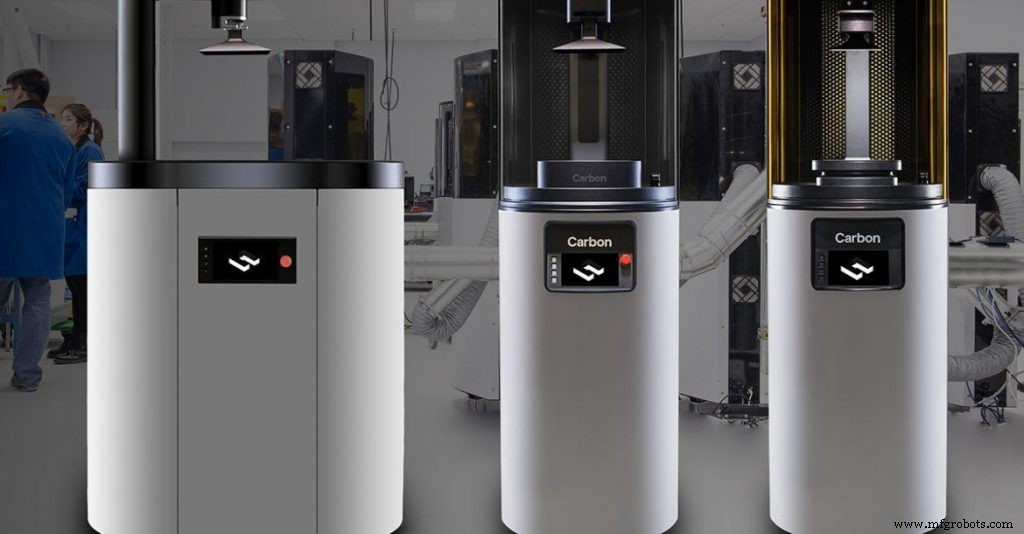
Fotopolymerisatie, waartoe ook de SLA- en DLP-processen behoren, is de afgelopen jaren aanzienlijk geëvolueerd.
Deze technologie heeft vooruitgang geboekt als een massaproductieproces en de recente introductie van fotopolymerisatie met hoge snelheid heeft deze trend alleen maar versneld.
Bijna alle grote spelers op dit gebied hebben systemen geïntroduceerd die in staat zijn functionele harsonderdelen te printen die dicht bij spuitgietvolumes liggen.
In 2014 introduceerde Carbon zijn high-speed Digital Light Synthesis-technologie, die evolueerde naar een M2 3D-printer die in staat is om te printen met een snelheid van 20 cm/uur.
Lees ook:mede-oprichter van Carbon, Philip DeSimone, over de overgang naar productie van hoge volumes met 3D-printen
In 2016 onthulde 3D Systems zijn kijk op snelle, geautomatiseerde SLA - het figuur 4-systeem. Recente gegevens markeren Afbeelding 4 Printsnelheden van productieonderdelen tot 65 mm/uur en prototypingsnelheden tot 100 mm/uur.
Andere bedrijven volgden, zoals EnvisionTEC (overgenomen door Desktop Metal), Nexa3D, Origin (overgenomen door Stratasys) en NewPro.
Processnelheid bij 3D-printen is lange tijd een van de zwakste kanten geweest. Dit is met name een obstakel voor adoptie in industrieën die worden aangedreven door massale serieproductie, zoals auto's en consumptiegoederen. In deze industrieën moeten producten in een zo kort mogelijk tijdsbestek worden vervaardigd en geleverd om de productie-efficiëntie te behouden.
Nu, met de vooruitgang in high-speed polymerisatie, is er een haalbare optie voor fabrikanten die onderdelen in hogere volumes in 3D willen printen.
Rize's Augmented Polymer Deposition (APD)-technologie
Het elimineren van nabewerking is een lang gekoesterde droom in de 3D-printindustrie - en de technologie van Rize belooft de pijnpunten van de nabewerking te verwijderen. De in de VS gevestigde fabrikant van 3D-printers heeft zijn hybride Augmented Polymer Deposition (APD)-technologie ontwikkeld, die materiaalextrusie combineert met inkjettechnologie.
Deze combinatie maakt het printen van ondersteunende structuren mogelijk die gemakkelijk met de hand kunnen worden verwijderd zodra het printproces is voltooid, en zonder dat er verdere nabewerkingen nodig zijn.
APD-technologie is gebruikt om isotrope, full-colour, industriële onderdelen te maken voor prototyping, tooling en productietoepassingen.
Vorig jaar introduceerde het bedrijf ook een nieuwe functie, waarbij gebruikers met behulp van de technologie beveiligde informatie, zoals een QR of barcode, op een onderdeel 3D kunnen printen. Dit zou bijvoorbeeld een ingenieur in staat stellen om alle informatie voor een specifiek onderdeel digitaal op te slaan en een digitale inventaris bij te houden.
BigRep's grootschalige FDM 3D-printing
Een van de belangrijkste belemmeringen voor de bredere acceptatie van FDM voor industriële toepassingen is de grootte van de bouwschil. Dit is een barrière die het Duitse bedrijf BigRep herhaaldelijk probeert te overwinnen met zijn ongelooflijk grote en zeer capabele lijn van 3D-printers.
Op formnext 2018 onthulde BigRep twee 3D-printers van de volgende generatie - de BigRep PRO (1005 x 1005 x 1005 mm) en BigRep EDGE (1500 x 800 x 600 mm) - gericht op industrieel gebruik.
Beide systemen zijn uitgerust met gepatenteerde Metering Extruder Technology (MXT), waardoor ze zich onderscheiden van andere grootschalige opties. Deze nieuwe extrudertechnologie zorgt voor een duidelijke scheiding tussen filamenttoevoer, smelten en extrusie, waardoor hogere printsnelheden met grotere precisie en kwaliteit mogelijk worden. De BigRep PRO zou bijvoorbeeld vijf keer de doorvoersnelheid van het filament en drie keer de gemiddelde extrusiesnelheid bieden, vergeleken met andere FDM-machines die op de markt verkrijgbaar zijn.
De MXT is geoptimaliseerd om te werken met professionele materialen zoals ASA/ABS en nylon die BigRep produceert in samenwerking met het Duitse chemiebedrijf BASF.
De BigRep PRO bevat met name de modernste CNC-besturingssystemen en aandrijvingen van Bosch Rexroth, waardoor IoT en gegevensverwerkingsmogelijkheden mogelijk zijn. Dit zal uiteindelijk helpen om de integratie van de printer in de Industrie 4.0-visie te versnellen.
Meer hierover:4 indrukwekkende toepassingen van grootschalig 3D-printen
Evolve's STEP-technologie
Steeds meer fabrikanten van 3D-printers richten hun blik op massaproductie, en Stratasys spin-off Evolve Additive Solutions is niet anders.
Na bijna een decennium van ontwikkeling, onthulde het bedrijf vorig jaar zijn nieuwe productiesnelheid "STEP" (afkorting voor Selective Toner Electrophotographic Process) voor polymeren.
Het STEP-proces van Evolve biedt een nieuwe benadering van volumeproductie met additive manufacturing, niet in de laatste plaats omdat het 50 keer sneller is dan de snelste beschikbare 3D-printtechnologieën.
Bovendien beweert het bedrijf dat de technologie in staat is om onderdelen te produceren met een kwaliteit die vergelijkbaar is met die gemaakt met conventionele methoden, en niet alleen in termen van esthetische afwerking, maar ook sterkte. Bovendien biedt de STEP-technologie mogelijkheden voor afdrukken op meerdere materialen en in full colour.
Hoewel Evolve nog twee jaar verwijderd is van commercialisering, zal hun technologie er een zijn om in de gaten te houden.
SAF van Stratasys
De steunpilaar van de 3D-printindustrie, Stratasys, blijft ook zijn aanwezigheid vergroten in het snelgroeiende gebied van 3D-printsystemen van productiekwaliteit. Het bedrijf heeft zojuist de aankomende lijn van op poederbedfusie (PBF) gebaseerde 3D-printers gepresenteerd.
Het nieuwe productieplatform uit de H-serie wordt aangedreven door Selective Absorption Fusion (SAF)-technologie die speciaal is ontworpen om te voldoen aan de behoeften van volumeproductie.
SAF is een op poeder gebaseerd 3D-printproces. Terwijl SLS echter een laser gebruikt om polymeerdeeltjes selectief samen te smelten, doet SAF iets heel anders.
SAF gebruikt een tegengesteld draaiende rol om poederlagen op een printbed te coaten en vervolgens laten printkoppen selectief absorberende vloeistof vallen om de laag van het onderdeel te vormen. De afgebeelde laag wordt versmolten door een IR-lamp over de gehele spanwijdte van het printbed te laten gaan, waardoor de geselecteerde gebieden versmelten.
Het goede aan dit nieuwe proces is dat het naar verluidt een hoge afdruksnelheid en schaalbaarheid biedt. De commerciële beschikbaarheid van 3D-printers op basis van SAF-technologie wordt momenteel verwacht in het derde kwartaal van 2021.
Als de SAF van Stratasys zijn visie waarmaakt, kan het een levensvatbaar alternatief worden voor de gevestigde SLS- en Multi Jet Fusion-processen.
Trends voor polymeer 3D-printen
Consolidatie van de markt voor polymeer 3D-printen
De additieve productie-industrie heeft de afgelopen zes maanden een golf van overnames en fusies meegemaakt, waarvan vele in de AM-polymeersector.
Hoewel fusies en overnames niets nieuws zijn in de AM-ruimte, hebben recente aankondigingen iets belangrijks gemeen:focus op productie.
Hier zijn enkele hoogtepunten van de recente fusies en overnames in 3D-printen van polymeren:
- In september 2020 kondigde Covestro het voornemen aan om de divisie DSM Resins &Functional Materials, inclusief DSM Additive Manufacturing, over te nemen.
- In december 2020 kondigde Stratasys de overname van Origin aan.
- In januari 2021 kondigde Desktop Metal de intentie aan om EnvisionTEC over te nemen.
Het is bemoedigend om te zien dat bedrijven samenkomen om hun aanbod te versterken en boeiende oplossingen voor industriële AM-productie te presenteren.
Deze wens om proces- en materiaalportfolio's uit te breiden met meer opties van een enkele moederbron die via een enkel distributienetwerk werkt, zal het mogelijk maken om aan veel meer klantverzoeken te voldoen.
Dit op grote schaal doen, met een focus op herhaalbaarheid en betrouwbaarheid, is een grote stap voorwaarts voor het 3D-printen van polymeren.
Plastic gebruiken in plaats van metaal
Gewichtsvermindering is een specifiek doel voor sommige industrieën, zoals de lucht- en ruimtevaart en de motorsport. Door een vliegtuig of voertuig lichter te maken, wordt het brandstofverbruik verminderd en de prestaties van een voertuig geoptimaliseerd.
Hoewel deze industrieën over het algemeen vertrouwen op metalen lichtgewichtoplossingen om het gewicht te verminderen, bieden de recente ontwikkelingen op het gebied van polymere 3D-printmaterialen een aantal opwindende kansen. De mogelijkheid om hoogwaardige thermoplasten zoals koolstofvezel, ULTEM en PEEK in 3D te printen, kan betekenen dat metalen in sommige toepassingen kunnen worden vervangen door kunststoffen.
Volgens één analyse kan het vervangen van aluminium vliegtuigbeugels door PEEK-alternatieven resulteren in een gewichtsvermindering van 5 tot 9%, wat een enorme impact kan hebben op het brandstofverbruik van een vliegtuig.
Het vervangen van een metalen onderdeel door 3D-geprint plastic kan ook gunstig zijn voor het versnellen van het onderhoudsproces. Een servicebureau heeft Stratasys FDM Nylon 12CF carbon gevulde thermoplast gebruikt om een vervanging te maken voor een metalen machine onderdeel. Het 3D-printen van het reserveonderdeel resulteerde in een superieur onderdeel, veel sneller geproduceerd dan zijn conventioneel vervaardigde tegenhanger.
Lees ook:Composiet 3D-printen:een opkomende technologie met een mooie toekomst
Dingen om te overwegen bij het gebruik van polymeer 3D-printen in eigen beheer
Duurzaamheid
Recycling en hergebruik van polymere 3D-printmaterialen is een belangrijke factor om te overwegen bij het intern toepassen van polymeer AM.
Bij 3D-printen op basis van filamenten is recycling gemeengoed, en veel bedrijven produceren plastic filamenten van gerecycled plastic.
Hoewel thermoplastische kunststoffen, zoals filament, eenvoudig te recyclen zijn door ze gewoon opnieuw te smelten, kunnen thermohardende kunststoffen niet worden omgesmolten, wat betekent dat ze niet kunnen worden gerecycled.
Bij poedergebaseerd 3D-printen van polymeren is hergebruik van poeder ook niet helemaal eenvoudig. In de meeste gevallen moet je 'gebruikt-maar-niet-gefuseerd' poeder mengen met ongeveer 50% nieuw poeder, om het opnieuw te kunnen gebruiken. Voor sommige hoogwaardige poeders, zoals PEEK, wordt de verversingssnelheid drastisch verlaagd en in sommige gevallen kan geen van de overtollige poeders opnieuw worden gebruikt.
Dus hoe kun je duurzaam printen met polymere 3D-printmaterialen? Eén manier is door afval te minimaliseren door betere ontwerpen. Zorg er daarnaast voor dat u contact opneemt met uw plaatselijke afval- of recyclingcentrum om te zien of zij de capaciteit hebben om 3D-geprinte polymeren veilig te verwijderen.
Meer hierover:hoe duurzaam is industrieel 3D-printen?
Nabewerking
Verwijderingsprocessen, zoals het verwijderen van dragers, hars- of poederverwijdering, zijn de meest gebruikte nabewerkingen bij 3D-printen van polymeren. Ze worden meestal handmatig uitgevoerd, wat veel tijd en arbeidskrachten kost.
Wat deze fase verder compliceert, is het feit dat je misschien verschillende 3D-printtechnologieën wilt gebruiken, elk met zijn eigen nabewerkingsvereisten.
Om de nabewerkingsactiviteiten te verbeteren, hebben bedrijven, zoals Rösler, PostProcess Technologies, AMT en DyeMansion, oplossingen ontwikkeld om AM-gebruikers te helpen de nabewerking te stroomlijnen.
Momenteel is de grootste trend het creëren van end-to-end nabewerkingsoplossingen, waaronder sorteren, materiaalverwijdering en ontpoedering, gladmaken en verven, en inspectie.
Bij het toepassen van 3D-printen met polymeren, is het noodzakelijk om de vereisten voor nabewerking te begrijpen. Niet-geoptimaliseerde nabewerking kan veel kosten toevoegen aan 3D-printbewerkingen, wat kan en moet worden vermeden door automatisering.
Workflowbeheer
Als u polymeer 3D-printen in-house toepast, moet u ook nadenken over benaderingen voor het beheer van activiteiten, zoals orderbeheer, kostenberekening, productieplanning, voorraadbeheer, enz.
Veel bedrijven vertrouwen tegenwoordig op oplossingen die oorspronkelijk zijn ontwikkeld voor traditionele productie of ontwikkelen hun software intern. Elke aanpak leidt vaak tot een silo-workflow, die niet zichtbaar is en niet gemakkelijk kan worden geschaald.
Om niet in de val te lopen van een inefficiënte, niet-schaalbare workflow, is het een goede gewoonte om oplossingen voor workflowbeheer en productie-uitvoering te implementeren die zijn ontwikkeld met de vereisten voor 3D-printen in gedachten.
Er zijn tegenwoordig verschillende opties op de markt, maar slechts enkele bieden end-to-end-oplossingen die de volledige 3D-printworkflow dekken.
Ontdek voor meer informatie over dergelijke oplossingen onze whitepaper "Additive Manufacturing MES Software:The Essential Guide"
De toekomst van 3D-printen met polymeren
Van realistische conceptmodellen tot stevige prototypes, ergonomische gereedschappen en functionele eindgebruiksonderdelen, de mogelijkheden die polymeer 3D-printen biedt, zijn enorm.
Hoewel er nog enkele uitdagingen moeten worden overwonnen, zoals het uitbreiden van de materiaalkeuze en het terugdringen van materiaalkosten, zullen de voortdurende ontwikkelingen in 3D-printen van polymeren bedrijven helpen de voordelen van de technologie verder te benutten.
Nu de AM-industrie als geheel, en polymeer 3D-printen in het bijzonder, steeds meer richting de productie van eindonderdelen gaat, zien we dat 3D-afdrukbare composieten en hoogwaardige thermoplasten steeds meer grip krijgen.
Hoewel 3D-printen met polymeren de conventionele processen niet zal vervangen, zal de technologie zeker de huidige productiemogelijkheden verbeteren en geavanceerde industriële toepassingen ontsluiten.
Op zoek naar meer inzicht in polymeer 3D-printen? Bekijk de onderstaande artikelen:
Stereolithografie en digitale lichtverwerking:waar staan we vandaag?
FDM 3D-printen:waar zijn we vandaag?
De evolutie van SLS:nieuwe technologieën, materialen en toepassingen
3d printen
- Alles wat u moet weten over vuurvaste metalen
- Ondersteunende structuren voor 3D-printen:de belangrijkste dingen die u moet weten
- De aankomende 3D-printermodellen die u moet kennen
- PLA 3D-printen:alles wat u moet weten
- 3D-printen met ABS-kunststof:alles wat u moet weten
- Nylon 3D-printen:alles wat u moet weten
- Alles wat u moet weten over het spuiten van metaalbindmiddelen
- Alles wat u moet weten over noodonderhoud
- Metallurgische montagepers:alles wat u moet weten
- Spuitgieten versus 3D-printen:alles wat u moet weten
- Wat u moet weten over polymeren