Een inleiding tot de productie van draadboogadditieven [update 2020]
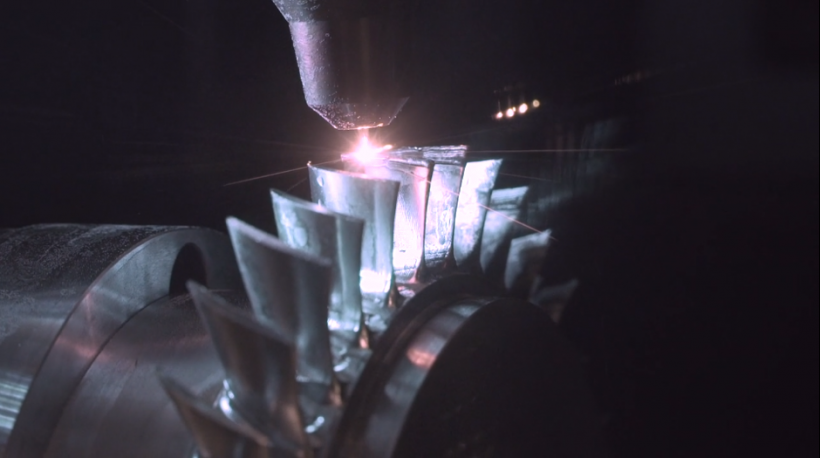
Wire Arc Additive Manufacturing (WAAM) is een van de minder bekende metaal 3D-printtechnologieën, maar wel een met een enorm potentieel voor grootschalige 3D-printtoepassingen in meerdere industrieën.
Deze gids zal zich richten op hoe WAAM werkt, de voordelen en beperkingen, evenals de belangrijkste WAAM-bedrijven en succesvolle toepassingen.
Hoe werkt Wire Arc Additive Manufacturing?
WAAM is een variant van een Direct Energy Deposition-technologie en maakt gebruik van een booglasproces om metalen onderdelen in 3D te printen.
In tegenstelling tot de meer gebruikelijke AM-processen met metaalpoeder, werkt WAAM door het smelten van metaaldraad met behulp van een elektrische boog als warmtebron.
Het proces wordt bestuurd door een robotarm en de vorm is gebaseerd op een substraatmateriaal (een basisplaat) waaruit het onderdeel kan worden gesneden zodra het klaar is.
De draad wordt, wanneer gesmolten, geëxtrudeerd in de vorm van kralen op het substraat. Terwijl de kralen aan elkaar plakken, creëren ze een laag metaalmateriaal. Het proces wordt vervolgens laag voor laag herhaald totdat het metalen deel is voltooid.
Je kunt het proces hier in actie zien:
Materialen
WAAM kan met een breed scala aan metalen werken, mits in draadvorm. Deze lijst omvat roestvrij staal, legeringen op nikkelbasis, titaniumlegeringen en aluminiumlegeringen. Elk metaal dat kan worden gelast, kan ook worden gebruikt met WAAM.
De voordelen van productie van draadboogadditieven
De mogelijkheid om grote metalen onderdelen in 3D te printen
WAAM is met name geschikt voor het vervaardigen van grootschalige metalen onderdelen. Dit in tegenstelling tot Powder Bed Fusion (PBF) metaal AM-technologieën, die doorgaans kleinere, high-definition componenten produceren.
In tegenstelling tot PBF AM-machines, die een beperkte bouwomhulling hebben, heeft de robotarm van een WAAM-machine meer bewegingsvrijheid, wat betekent dat de grootte van een onderdeel niet wordt beperkt door de ruimte, maar alleen door de afstand die de robotarm kan bereiken. Dit maakt de productie van grotere onderdelen mogelijk, wat niet mogelijk zou zijn met PBF-processen.
Goedkoper proces en materialen
In termen van materiaalkosten is de lasdraad die wordt gebruikt in het WAAM-drukproces aanzienlijk goedkoper dan het metaalpoeder dat wordt gebruikt in metalen PBF.
Dit komt omdat de WAAM-technologie gebaseerd is op lassen, een gevestigde productietechnologie op zich. WAAM-hardware omvat meestal kant-en-klare lasapparatuur, die minder duur is dan veel metalen 3D-printers die op de markt verkrijgbaar zijn.
Bovendien is draad doorgaans gemakkelijker te hanteren dan poeder, waarvoor gespecialiseerde beschermingsmiddelen nodig zijn gebruiken.
Hoge kwaliteit onderdelen
Onderdelen geproduceerd met WAAM vallen vooral op vanwege hun hoge dichtheid en sterke mechanische eigenschappen, die vergelijkbaar zijn met onderdelen die zijn vervaardigd met traditionele productiemethoden.
Aangezien de draadgrondstof een 100 procent dicht invoermateriaal is, wordt er een verwaarloosbare porositeit geïnduceerd in het fabricageproces, wat leidt tot een zeer dicht einddeel.
Het is geschikt voor reparatiewerkzaamheden
WAAM is ook een goede optie voor reparatie- en onderhoudswerkzaamheden voor specifieke componenten zoals turbinebladen, maar ook voor mallen en matrijzen.
Versleten onderdelen of beschadigde onderdelen kunnen met WAAM worden gerepareerd door nieuw materiaal te deponeren op zijn oppervlak. Dit kan leiden tot aanzienlijke kostenbesparingen omdat het niet nodig is om een nieuw onderdeel helemaal opnieuw te produceren.
De beperkingen van WAAM
Resterende spanningen en vervormingen
Een van de uitdagingen van WAAM is warmtebeheer.
Het printproces gaat gepaard met hoge temperaturen, waardoor restspanning ontstaat - een probleem dat vaak voorkomt bij 3D-metaalprinten. Omdat restspanning vaak kan leiden tot vervormingen in een onderdeel, moet er rekening worden gehouden met koeling.
Sommige materialen vereisen afscherming
Bij het gebruik van bepaalde materialen, zoals titanium, is afscherming nodig om een inerte atmosfeer te creëren om de juiste bouwomstandigheden te garanderen.
Dit betekent dat het proces moet plaatsvinden in een inerte gaskamer. De kamer met inert gas beperkt echter de afmetingen van de onderdelen die met deze technologie kunnen worden geproduceerd en het installeren van een dergelijke kamer zal de kosten van de apparatuur verhogen.
Lage resolutie
WAAM produceert typisch bijna netvormige onderdelen met een slechte oppervlakteafwerking. Het oppervlak van een onderdeel moet daarom machinaal worden afgewerkt.
Belangrijke WAAM-spelers en technologietoepassingen
WAAM3D
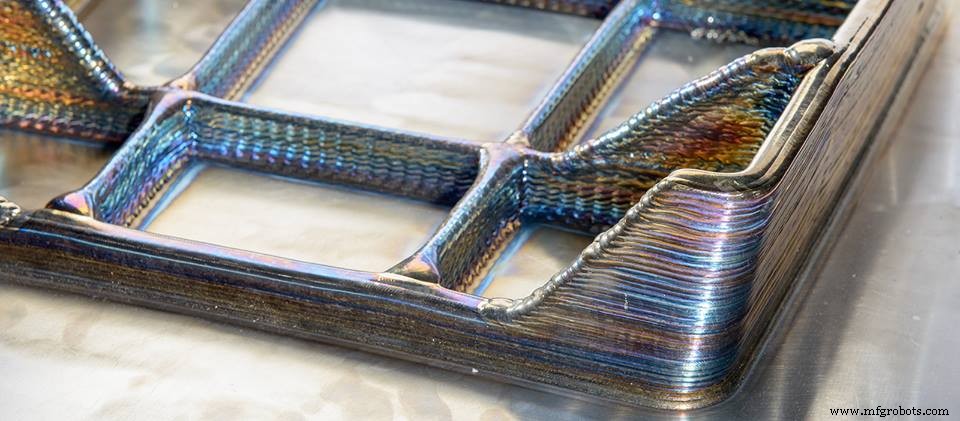
Vanaf 2020 blijft de WAAM-markt klein, met een handvol bedrijven die deze metalen 3D-printtechnologie actief ontwikkelen.
WAAM3D is misschien een van de minder bekende namen in het veld, maar het bedrijf heeft uitgebreid onderzoek gedaan voordat het zijn technologie op de markt bracht.
WAAM3D werd opgericht in 2018 om het intellectuele eigendom van Cranfield University op het gebied van WAAM te commercialiseren.
Volgens het bedrijf heeft het gebrek aan toeleveringsketen – namelijk softwaretools, door WAAM ontworpen hardware, grondstoffen, training en diensten – de verdiende industriële acceptatie van WAAM-processen belemmerd, ondanks de bewezen zakelijke voordelen .
Het bedrijf streeft ernaar een dergelijke toeleveringsketen te creëren en het gebruik van WAAM in de lucht- en ruimtevaart- en defensie-, olie- en gas-, energie- en nucleaire industrie te bevorderen.
Tot nu toe heeft WAAM3D verschillende succesvolle toepassingen van zijn technologie gepubliceerd.
One is een achterframe voor de Eurofighter Typhoon-jager van BAE Systems. Het titanium onderdeel, dat 2,5 mx 1,5 m meet in vlak gebied, ondersteunt de dubbele Eurojet EJ200-motoren die 60 kN (13.500 lbf) droge stuwkracht kunnen produceren.
Een ander titanium onderdeel, een 1 m lange druk schip, is vervaardigd voor Thales Alenia Space. Door WAAM te gebruiken om dit onderdeel te vervaardigen, bespaarde het team meer dan 200 kg materiaal per item en kon het twee delen van het vat samenvoegen tot één.
Bovendien duurde de productie van het onderdeel naar verluidt enkele dagen – een aanzienlijke verkorting van de doorlooptijd, aangezien de productie van het onderdeel gewoonlijk enkele maanden duurt.
Eerder dit jaar rondde WAAM3D zijn eerste Series A-financieringsronde af, die het bedrijf naar verwachting verder zal brengen naar commercialisering van WAAM-technologie.
AML3D
Cranfield University inspireerde de oprichting van een ander bedrijf:AML3D. De algemeen directeur van AML3D, Andrew Sales, studeerde aan Cranfield en, gefascineerd door het potentieel van de technologie, richtte hij in 2014 een WAAM-servicebureau op in Australië.
In 2019 behaalde het bedrijf de certificering van de wereldwijde accreditatie-instantie voor de scheepvaartindustrie, Lloyd's Register. Met de certificering op zijn plaats, leverde AML3D zijn eerste onderdeel aan een maritieme klant:een set martensitische roestvrijstalen slijtringen.
De onderdelen zijn traditioneel gesmeed en vereisen een extra nabewerkingsstap met warmtebehandeling. Dit proces verhoogt de totale doorlooptijd tot zes tot acht weken. Dergelijke artikelen met een lange doorlooptijd moeten in een fysieke inventaris worden bewaard of voortijdig worden vervangen.
Door WAAM te gebruiken, kon AML3D de ringen produceren voor dezelfde kosten, terwijl de doorlooptijd werd teruggebracht tot slechts enkele dagen. Dit is een cruciale verbetering voor schepen die voor een beperkte tijd in het dok blijven.
Om zijn capaciteit verder te vergroten, is het bedrijf nu van plan om op korte termijn een productiefaciliteit in Singapore te lanceren. Dit wordt gedreven door de vraag vanuit de maritieme hub van Singapore, aangezien de locatie een strategische hub is voor commerciële scheepvaartroutes.
Ramlab
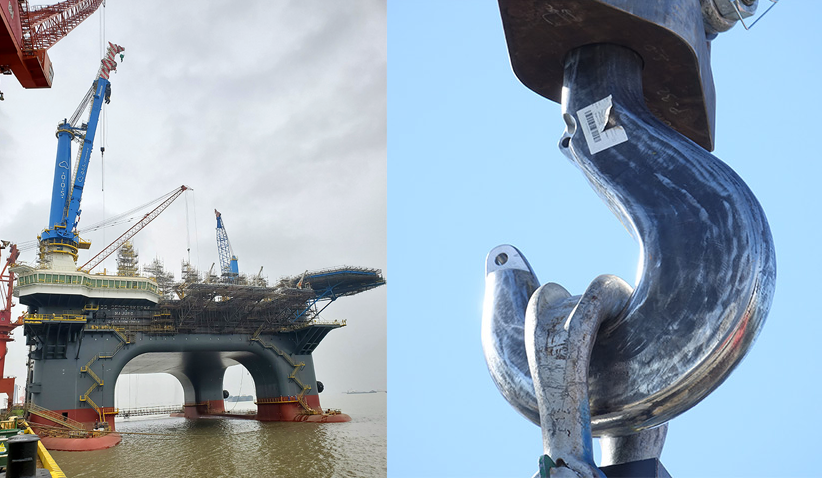
In dezelfde geest gebruikt het Additive Manufacturing Fieldlab (RAMLAB) van de Haven van Rotterdam WAAM om de productie van maritieme onderdelen te versnellen. Het bedrijf maakte in 2017 furore door 3D-printen van een volledig prototype van 's werelds eersteklas goedgekeurde scheepsschroef.
De “WAAMpeller” gebruikt 298 lagen nikkel aluminium brons legering en weegt 400 kg. Het onderdeel werd in zeven maanden voltooid, wat het potentieel van WAAM aantoont om de productie van toekomstige scheepscomponenten te optimaliseren.
In 2018 startte Ramlab, in samenwerking met Huisman Equipment, een ander project om een grote offshore 3D-print te maken kraanhaak, weegt bijna 1000 kg. Huisman Equipment ging nog verder in dit project en 3D-geprint, gecertificeerd en geïnstalleerd een 36.000 kg zware WAAM haak, speciaal ontworpen voor gebruik in offshore hijswerkzaamheden.
MX3D
Een van de eerste toepassingen die WAAM-technologie voor de wereld opende, was een 3D-geprinte stalen brug, ontwikkeld door de Nederlandse start-up MX3D.
Het brugproject, dat in 2018 van start ging, nam meer dan een jaar in beslag, maar diende als een showcase van het potentieel van grootschalig 3D-metaalprinten.
Meer recentelijk gebruikte het MX3D-team zijn technologie om een aluminium fietsframe in 3D te printen. Het futuristisch ogende frame is ontworpen met behulp van generatieve ontwerpsoftware en 3D-geprint in twee delen binnen 24 uur, wat de hoge afdruksnelheid van MX3D's WAAM-technologie laat zien. MX3D ontwikkelde ook een 'slimme armatuuropstelling', waarmee naar verluidt elk aangepast WAAM-frame gemakkelijk kan worden voorbereid om te rijden.
Gefertec
Een andere speler in de WAAM-arena is het Duitse bedrijf Gefertec. In 2017 onthulde het zijn 3DMP®-productietechnologie, die deel uitmaakt van de GTarc AM-machineserie van Gefertec.
Het grootste systeem heeft een 3-assig systeem voor de productie van onderdelen tot 3 m3 met een maximum massa van 3000 kg.
Het interessante aan de machines van Gefertec is dat ze kunnen worden geïntegreerd met een freessysteem. Dit betekent dat er de mogelijkheid is om een hybride systeem te creëren, waarbij 3DMP®-technologie wordt gebruikt om een onderdeel te creëren dat vervolgens direct wordt afgewerkt met bewerking.
Een voorbeeld van het gebruik van de technologie van Gefertec is het 3D-printen van een metalen wiellagerdeksel voor een locomotief. Dit locomotiefmodel is in de jaren '60 en '70 in gebruik genomen, waardoor het moeilijk kan zijn om reserveonderdelen te verkrijgen, die vaak niet meer verkrijgbaar zijn.
Als gevolg hiervan zou de levering van het onderdeel traditioneel tot negen maanden duren, en gedurende deze tijd zou de locomotief buiten dienst zijn, met hoge kosten tot gevolg.
Gefertec's Er werd een 3D-printer gebruikt om dit reserveonderdeel te produceren en het project, van het eerste ontwerp tot reverse engineering en productie, was binnen twee maanden voltooid. Hoewel dit de eerste keer was dat een werkstuk werd geproduceerd, is het met een vaststaand proces mogelijk om de doorlooptijd nog verder te verkorten, mogelijk tot slechts enkele weken.
WAAM – de haalbare optie voor grootschalige productie van additieven voor metalen
Met relatief nieuwe technologie zoals WAAM, kost het tijd om applicaties te ontwikkelen en de voordelen worden in de hele industrie gevoeld. We zien echter de vraag naar grote metalen 3D-geprinte componenten groeien, wat suggereert dat de adoptie van WAAM zal versnellen.
Uiteindelijk is het duidelijk dat WAAM de manier waarop grote metalen onderdelen worden geproduceerd transformeert, waardoor bedrijven de mogelijkheid krijgen van een snellere en kosteneffectievere productiemethode.
3d printen
- Additieve productie versus subtractieve productie
- Voordelen van additieve fabricage
- Een onderzoek naar workflows voor additieve productie
- Interview met expert:Nanci Hardwick, CEO van MELD Manufacturing, over het benutten van het potentieel van de productie van metaaladditieven
- Productie van metaaladditieven:5 vragen om een potentiële leverancier van metaalpoeder te stellen
- Additive Manufacturing Podcast Aflevering 3
- Additive Manufacturing Podcast Episode One
- De beste metalen 3D-printmaterialen voor additieve productie
- Additive Manufacturing in consumententoepassingen
- Additieve productie in elektronica
- Additieve productie in de lucht- en ruimtevaart