De kosten van 3D-printmaterialen met continue vezels verlagen
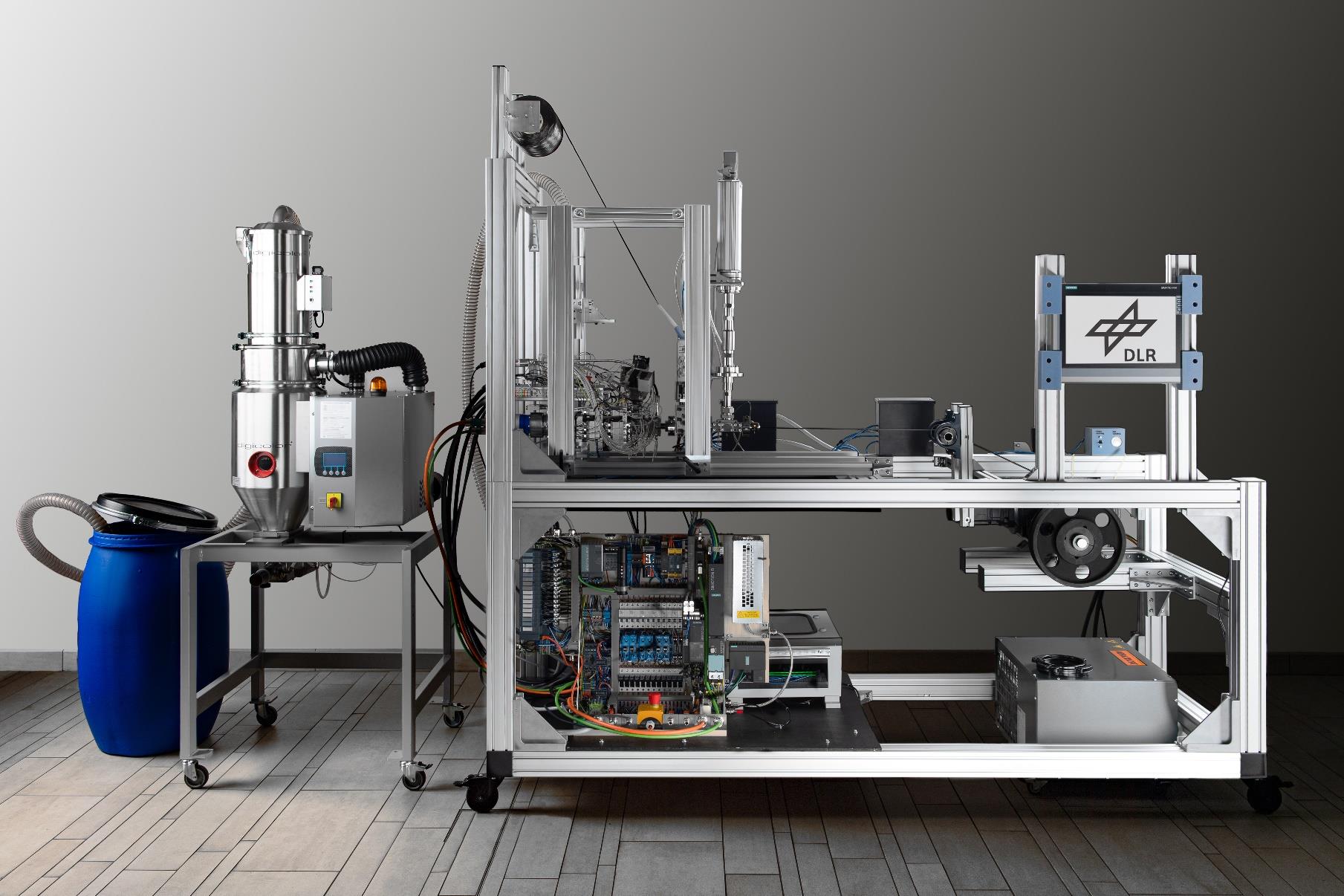
DLR Institute of Composite Structures and Adaptive Systems (Braunschweig, Duitsland) is een toonaangevende onderzoeksinstelling op het gebied van lichtgewicht constructie, die nieuwe technologieën nastreeft op vier strategische gebieden:ontwerp tot certificering, digitalisering en Industrie 4.0, recycling en additieve composietstructuren. CW eerder dit jaar gerapporteerd over het EmpowerAX Innovation Lab van het instituut om de overdracht van additieve extrusie naar de industrie voor 3D-geprinte composieten te versnellen, versterken en verbreden. voltooit ook een reeks R&D-projecten, waaronder simulatie van additieve extrusie, modificatie van thermoplasten voor verbeterde prestaties bij 3D-printen en productie van printerfilamenten met continue vezels.
Dit laatste project, getiteld ENDLOSEFFEKT ("eindeloos effect"), is ontworpen om de produceerbaarheid, kwaliteit en kosten van vezelversterkte materialen met een eindeloze lengte te verbeteren. "De beschikbaarheid van voorgeïmpregneerde continue vezelprintfilamenten is beperkt", legt Maik Titze uit, verantwoordelijk voor additive manufacturing bij het DLR Institute of Composite Structures and Adaptive Systems in Braunschweig. “Deze beperkte beschikbaarheid en verscheidenheid aan bruikbare materialen, evenals de materiaalprijzen, vormen een barrière voor toepassing. We wilden een impregneermondstuk ontwerpen zodat dezelfde apparatuur die wordt gebruikt om standaard, met gehakte vezel gevulde filamenten voor FDM [fused deposition modeling] te produceren, ook continue vezelversterkte filamenten kan produceren. Deze apparatuur is bedoeld voor bedrijven die filamenten voor 3D-printers maken, met als doel de kosten van 3D-printen met continu vezelversterkte materialen te verlagen.”
Momenteel worden de meeste continu vezelversterkte 3D-printerfilamenten gemaakt door dezelfde bedrijven die continue vezeldrukmachines verkopen, waarbij elk materiaal is ontwikkeld en geoptimaliseerd voor een bepaald printsysteem. Deze materialen zijn meestal wat duur.
"Ons idee is om te beginnen met droge vezels van elke grootte, bijvoorbeeld 1K koolstofvezel tot 50K, en vervolgens directe smeltimpregnering te gebruiken van standaard thermoplastische pellets of korrels via extrusie, omdat dit zeer kosteneffectief is", zegt Titze. “Je hoeft geen polymeerpoeder of folies te produceren, noch dure persen of honderden rollen te gebruiken om de vezel te impregneren. De verwerking wordt dus veel toegankelijker en betaalbaarder.”
In plaats van persen, banden en rollen bedacht DLR een systeem met ultrageluid. "We gebruiken een sonotrode van 19,5 kilohertz die trillingen in de gesmolten thermoplast die de vezel omringt, leidt", legt Titze uit. “Dit de matrix en wapening bij 19.500 keer per seconde, wat resulteert in een zeer goede impregnatie.”
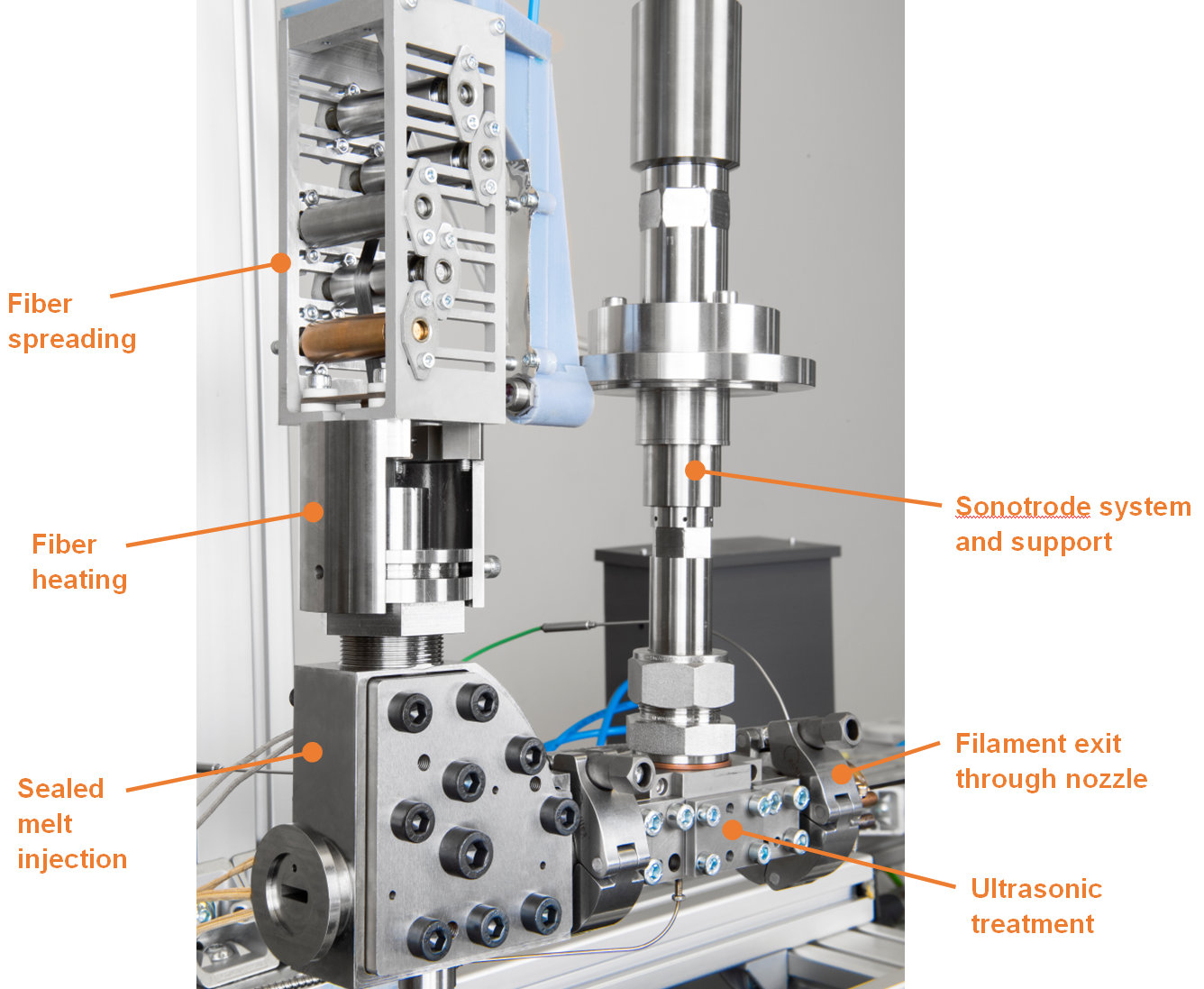
Het procestraject begint met vezelverspreiding en verwarming (afb. 1). Deze wapening wordt vervolgens in een afgesloten kamer gevoerd waarin het gesmolten polymeer wordt geïnjecteerd. Terwijl de vezel door deze kamer gaat, bedekt gesmolten hars de vezel. "De vezel en het polymeer gaan vervolgens naar een ultrasone kamer, die met een lengte van 80 millimeter erg klein en compact is", merkt Titze op. “De door de sonotrode uitgestraalde trillingen zorgen ervoor dat het vezelversterkte polymeerfilament de nozzle verlaat in elke gewenste vorm. Het mondstuk kan bijvoorbeeld rond of plat zijn.”
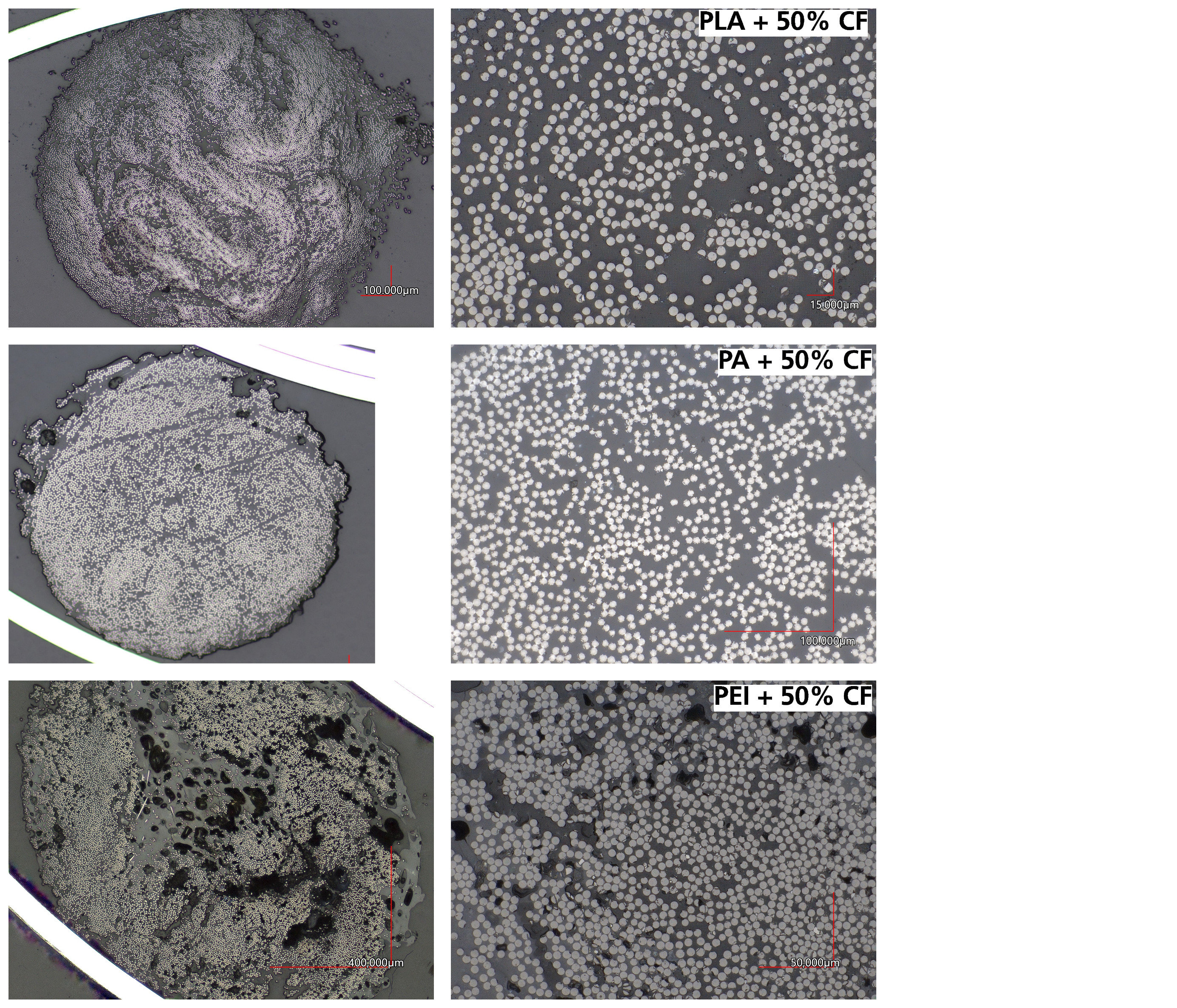
De microfoto's in Fig. 2 tonen 12K koolstofvezel geïmpregneerd met polymelkzuur (PLA), polyamide (PA) en polyetherimide (PEI) met een vezelvolume van 50%. Het vezelvolume is instelbaar (30-50%) door het ontwerp van de spuitmond, zegt Titze. “We denken dat tot 60% mogelijk zal zijn. Over het algemeen is er meer werk nodig aan het proces, maar we hebben laten zien dat het werkt met goede eerste resultaten en een lijnsnelheid van 5 millimeter/seconde.” Hij geeft toe dat dit traag en niet economisch is, maar in juni zou een nieuw ontwerp van de apparatuur worden getest, dat al was gericht op het bereiken van 3 meter/minuut.
"Normaal gesproken zouden snelheden dichter bij 10 meter / minuut liggen", zegt Titze. “De technologie is echter ook bedoeld om flexibele productie van nieuwe materiaalcombinaties mogelijk te maken, dus een iets lagere snelheid zou kunnen helpen om kleinere productieruns betaalbaar te maken.
Het proces dat DLR heeft ontwikkeld, is niet selectief voor één materiaal - elke vezel of polymeer kan worden gebruikt, zegt Titze. "Dit is belangrijk omdat processen blijven hybridiseren en er nieuwe materialen nodig zijn. Materialen voor 3D-printen moeten concurrerender worden, anders heeft 3D-printen met continue vezels geen grote toekomst. Door thermoplastische korrels of korrels te gebruiken, kunnen we de kosten aanzienlijk verlagen en past de apparatuur in een kleine installatieruimte, zodat zelfs kleine bedrijven het kunnen implementeren.”
DLR Institute of Composite Structures and Adaptive Systems startte dit project in oktober 2019 en zal het in januari 2022 afronden. "Ons doel is om de technologie verder te miniaturiseren en te integreren in een printkop", zegt Titze. “Dus dit zou directe impregnering zijn in lijn met het bedrukken. Beide benaderingen zal worden overgedragen aan de industrie.” Hij legt uit dat DLR als non-profit van de overheid niets zal "verkopen" en daarom exclusieve rechten. "Ons doel is om printkopleveranciers erbij te betrekken om de materiaalprijzen over de hele linie te verlagen en de industriële toepassing van continue vezeladditieve productie te verbreden."
Hars
- De verborgen voordelen van het verlagen van de materiaalkosten voor 3D-printen
- 6 manieren om de kosten van 3D-printen te verlagen
- 5 trends die de markt voor 3D-afdrukmaterialen in 2019 vormgeven
- De totale eigendomskosten verlagen
- De kosten van koolstofvezel:waarom de kwaliteit de moeite waard is
- Koolstofvezelkosten:factoren die de meeste invloed hebben
- De rol van koolstofvezel in ruimtevaartmaterialen
- De voordelen van vezelversterkte kunststof versus traditionele materialen
- Continue vezelproductie vervaagt de grens tussen 3D-printen en AFP
- 3D-print composieten met continue vezels
- De beste flexibele materialen in 3D-printen