Low-Code en No-Code software:de toekomst van kwaliteitscontrole
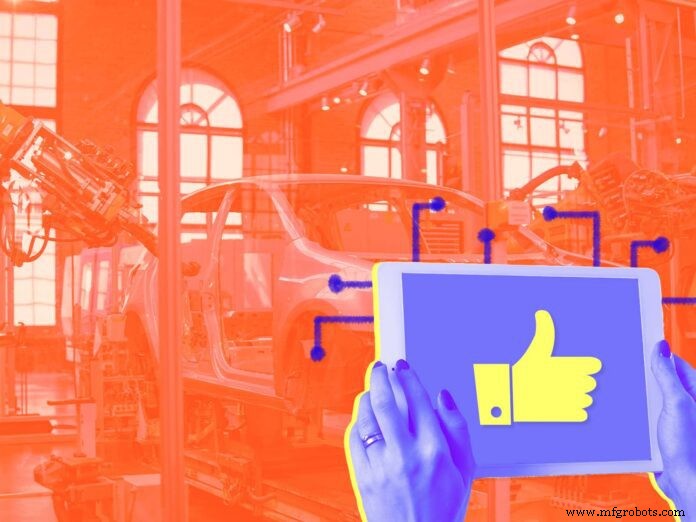
Het proces van kwaliteitscontrole zorgt ervoor dat de productienormen van een product worden gehandhaafd en verbeterd. Het kwaliteitscontroleproces stelt bedrijven in staat om aan de verwachtingen van de klant te voldoen en tegelijkertijd een consistent niveau van productkwaliteit te garanderen. Door deze normen aan te nemen, ontstaat een bedrijfscultuur waarin alle medewerkers worden aangemoedigd om te streven naar productienormen van hoge kwaliteit. Low-code en no-code software kan een game-changer worden voor kwaliteitscontroleteams die hun gegevens en analyse willen digitaliseren.
Waarom kwaliteitscontrole implementeren?
Het primaire doel van kwaliteitscontrole is om te zoeken naar eventuele corrigerende maatregelen om producten tijdens het productieproces te verbeteren. Een essentieel onderdeel van kwaliteitscontrole is het opzetten van een controlesysteem dat acceptabele productparameters schetst en productieprocessen standaardiseert. Er worden normen opgesteld en beoordeeld over de hele productielijn, waar medewerkers de grondstoffen assembleren en afgewerkte producten produceren. Door elk product in verschillende stadia van ontwikkeling te testen, kunnen productieproblemen worden geïdentificeerd en snel verholpen.
Vaak hebben bedrijven gespecialiseerd personeel in dienst, creëren ze kwaliteitsbenchmarks en testen ze producten in verschillende productlijnen. Deze praktijken stellen niet alleen normen voor de productie, maar ze kunnen er ook voor zorgen dat werknemers niet betrokken raken bij taken die ze niet kennen.
Kwaliteitscontrolemethoden zijn afhankelijk van het soort producten dat het bedrijf vervaardigt en de gerelateerde industrie. Als het bedrijf bijvoorbeeld actief is in de voedings- of geneesmiddelenindustrie, moeten fabrikanten ervoor zorgen dat hun producten niemand ziek maken of niet besmet zijn. Er kunnen ook strenge fabrieks- of productielijncertificeringen of wettelijke vereisten zijn waaraan moet worden voldaan.
Voordelen van consistente kwaliteitscontrole
In de hele maakindustrie biedt kwaliteitscontrole enorme voordelen. Sommigen van hen omvatten:
#1:kostenefficiëntie
Effectieve kwaliteitscontrole verlaagt de productiekosten. Zorgvuldige normen zorgen ervoor dat defecte producten snel worden geëlimineerd en dat er verbeteringen worden aangebracht om de problemen te verhelpen. Naarmate de kwaliteit verbetert, verlaagt het bedrijf de lopende kosten van herbewerking, afval en verspilde arbeidstijd. Dit betekent een optimale benutting van middelen, waardoor de leverings- en productiekosten afnemen.
#2:Naleving
Het consequent produceren van hoogwaardige producten zorgt ervoor dat het bedrijf kan voldoen aan industriële kwaliteitsnormen en aan strenge regelgeving. Wanneer de kwaliteitscontrole zorgvuldig wordt ingericht om te voldoen aan de nalevingsbehoeften, kan de productielijn soepel draaien, zelfs in een industrie zoals medische apparaten, die sterk gereguleerd is.
#3:klantloyaliteit behouden
Het produceren van hoogwaardige producten helpt bij het koesteren van een positief merkimago. De klanttevredenheid zal hoger zijn en hopelijk leiden tot langdurige klantloyaliteit. Kopers zullen meer vertrouwen krijgen in uw merk en het aanbevelen aan hun vrienden en familie, wat uiteindelijk de verkoop zal verbeteren.
#4:uitdagingen rond het digitaliseren van kwaliteitsgegevens
Kwaliteitscontrole is essentieel voor de productie. Daarom is het digitaliseren van het verzamelen en analyseren van kwaliteitsgegevens een prioriteit voor veel fabrikanten. Helaas zijn IT-teams onderbemand en overbelast en kunnen ze niet de desktop- of mobiele apps bouwen die nodig zijn voor modern kwaliteitsbeheer. Meer kwaliteitsteams nemen het op zich om hun processen te digitaliseren om hun inspanningen te stroomlijnen en beter met hun gegevens om te gaan.
Low-Code en No-Code Software
Low-code en no-code software kan een game-changer worden voor kwaliteitscontroleteams die hun gegevens en analyse willen digitaliseren. Low-code software maakt het kwaliteitsbeheerproces eenvoudiger en naadloos. Kwaliteitsteams hebben meestal IT-hulp nodig als ze nieuwe digitaliserings- of gegevensanalysemogelijkheden willen toevoegen aan het bestaande productiesysteem. Low-code software kan belangrijke MES- (Manufacturing Execution System) of QMS (Quality Management System)-systemen verbeteren, waardoor bedrijven gerichte, taakgebaseerde apps kunnen bouwen om het verzamelen van gegevens te versnellen zonder IT-hulp van bronnen.
Kwaliteitsteams kunnen low-code software gebruiken om apps voor gegevensverzameling of inspectie in weken of dagen te maken en te implementeren. Met low-code software kunnen kwaliteitsteams op papier gebaseerde processen elimineren door het verzamelen van gegevens te automatiseren en kwaliteitscontroleprocessen te digitaliseren, vaak zonder dat de app-bouwer weet hoe apps moeten worden gecodeerd. Leden van kwaliteitsteams, vloerleiders en productie-experts met kennis van de industrie kunnen low-code of no-code software gebruiken om snel hun eigen gespecialiseerde tools te bouwen en de IT-afdeling niet te verzanden met meer softwareverzoeken.
Voordelen van low-code voor kwaliteitscontrole
Er zijn verschillende voordelen van het gebruik van low-code of no-code software voor kwaliteitscontrole en -beheer:
#1:Behendigheid
In de maakindustrie zijn machines onderling afhankelijk, dus als zich een probleem voordoet in de ene machine, heeft dit gevolgen voor de andere machines. Door handmatig gegevens te verzamelen of sensoren te gebruiken en de gegevens aan een dashboardtoepassing te leveren, kunnen managers de status van het productieproces volgen. Als een machine bijvoorbeeld offline gaat, kan een app die machinesensorgegevens verzamelt, onmiddellijk een waarschuwing sturen dat de machine buiten acceptabele parameters is gevallen. Productie- of kwaliteitsmanagers kunnen direct actie ondernemen. Na verloop van tijd kunnen gegevenstrends worden geanalyseerd om inzichten te ontdekken en de prestaties van de apparatuur te verbeteren.
#2:betere, nauwkeurigere productiegegevens
Papieren processen kunnen foutgevoelig zijn. Ze kunnen geen uitgebreide gegevens vastleggen, zoals afbeeldingen, tijd- en datumstempels, audio-interviews, streepjescodes, enz. Wanneer fabrikanten de gegevensverzameling digitaliseren, leggen ze rijkere, nauwkeurigere gegevens vast die onmiddellijk kunnen worden gedeeld en geanalyseerd in de hele organisatie. Dit bespaart tijd voor kwaliteitsinspecteurs en zorgt ervoor dat bedrijven beslissingen kunnen nemen op basis van nauwkeurige, volledige en direct beschikbare gegevens.
#3:werkprocessen eenvoudiger maken
Fabrikanten gebruiken al heel lang op papier gebaseerde instructies, beleidsregels en handleidingen. Dit kan leiden tot verouderde of onvolledige informatie of zelfs werknemers die moeten zoeken naar een handleiding wanneer ze deze nodig hebben. Papieren materialen kunnen ook geen interactieve informatie presenteren, zoals een video over het repareren van een offline apparaat. Fabrikanten gebruiken low-code-applicaties om productieapparatuur te inspecteren en onmiddellijk relevante PDF- of videohandleidingen voor gerelateerde reparaties te verstrekken. Deze apps kunnen ook worden gebruikt om nieuwe medewerkers op te leiden of ervoor te zorgen dat reparaties correct en tijdig worden uitgevoerd.
#4:Predictive Maintenance en Connected Factories
IoT-sensoren (Internet of Things) en kunstmatige-intelligentietechnologieën houden nieuwe beloften in voor fabrikanten. Op papier gebaseerde processen en klemborden op de productievloer kunnen de voordelen van deze technologieën niet realiseren. Een op IoT gebaseerde onderhoudstoepassing heeft het potentieel om de faalkans van een bepaalde machine nauwkeurig te voorspellen. Het analyseert gegevens van verschillende sensoren en waarschuwt supervisors over de mogelijkheid van een storing. Op hun beurt kunnen supervisors tijdig onderhoudsschema's maken om het probleem aan te pakken voordat het zich daadwerkelijk voordoet. Wanneer slimme fabrieken zijn verbonden, kan dit managers van meerdere locaties een krachtig inzicht geven in hun fabrieksactiviteiten.
#5:Voorraden bijhouden
Een low-code voorraadbeheertoepassing kan realtime inzicht bieden in beschikbare voorraad of leveringsmaterialen. Barcodes kunnen worden gescand en de voorraad kan worden beheerd via een mobiele app. Apps kunnen zelfs de verzending van grondstoffen volgen en ervoor zorgen dat ze op tijd worden geleverd en nauwkeurig worden gecatalogiseerd voor toekomstig gebruik. Kwaliteits- en productieteams kunnen materiaaltekorten voorkomen en ervoor zorgen dat leveringen niet op een dok blijven zitten door de gegevens digitaal te maken.
De toekomst van kwaliteitscontrole
Low-code en no-code programma's voegen een enorme waarde toe aan de Industrie 4.0-revolutie. Door de flexibiliteit, verbondenheid, efficiëntie, realtime zichtbaarheid en communicatie te verbeteren, zijn low-code en no-code apps de toekomst van kwaliteitscontrole. Met de meest robuuste software die kunstmatige intelligentie en machine learning-analyses mogelijk maakt om de kwaliteitscontrole te versterken, kan deze software fabrikanten ook voorbereiden om in de toekomst te innoveren.
Internet of Things-technologie
- Kwaliteitscontrole is de eerste stap naar motorbetrouwbaarheid
- De toekomst van snijsoftware
- De toekomst is verbonden en het is aan ons om deze te beveiligen
- Zijn IoT en cloud computing de toekomst van data?
- De IPC-vereisten van complexe besturing
- De toekomst van data-integratie in 2022 en daarna
- Software AG voorspelt de toekomst van het internet der dingen
- Het internet der dingen:huidige trends en de toekomst
- De geschiedenis en toekomst van aluminium extrusie
- Automatisering en de toekomst van digitale productie?
- De basisprincipes van kwaliteitscontrole en inspectie bij CNC-bewerkingen