Hoe 5 grote autofabrikanten 3D-printen gebruiken
3ERP heeft veel van de verschillende manieren behandeld waarop autofabrikanten profiteren van de voordelen die 3D-printen op de voorgrond brengt. Nu technologie steeds meer voet aan de grond krijgt in de auto-industrie, merken veel bedrijven dit op, maar velen gebruiken het in verschillende hoedanigheden en voor verschillende doeleinden. Deze behoeften kunnen alles omvatten, van gereedschap tot reserveonderdelen/supply chain management tot eindgebruiksonderdelen en zelfs volledige auto's.
Het is interessant om te zien hoe ver de technologie is gekomen, hoe deze wordt gebruikt door de grote namen in de industrie en waar ze het zien gaan voor hun toekomstige productieketens. Dit artikel is bedoeld om inzicht te geven in de vele manieren waarop enkele van de grootste autofabrikanten ter wereld 3D-printen in hun workflow gebruiken.
BMW
Aangezien het meeste 3D-printen wordt gebruikt voor productieruns van kleinere volumes, is er veel ruimte voor maatwerk en het toevoegen van complexiteit met behulp van de unieke elementen die 3D-printen mogelijk maakt. BMW is geen onbekende in dergelijke vormen van ontwerp en productie, waarbij 3D-printen wordt gebruikt in pre-ontwikkeling, voertuigvalidatie en testen, of in concept- en showauto's. Ze gebruiken de technologie voor grotere volumes, maar kleinere productieruns stellen hen in staat om producten precies aan te passen aan de behoeften van hun klant.
Het bedrijf is productief geweest in het gebruik van additieve productie en merkt op dat ze mogelijk "groot toekomstig potentieel zien voor serieproductie en nieuwe klantenaanbiedingen ” (volgens BMW-experts in Duitsland). Ze hebben de technologie gebruikt om zowel plastic als metalen componenten te verbeteren. Ze hebben het meest bekend om hun samenwerking met HP om producten te produceren op hun grootschalige productiesystemen.
Net als veel andere bedrijven op deze lijst, heeft BMW het gebruikt als een middel om onderdelen te produceren die andere technologieën niet kunnen maken. Een goed voorbeeld hiervan is de bovenklep van de i8 Roadster. Het maken van de montage voor dit onderdeel zou niet mogelijk zijn geweest met een traditioneel gietproces. Afgezien van de uitbreiding van de ontwerpmogelijkheden, is het 3D-geprinte auto-onderdeel duurzamer en weegt het ook minder dan eerdere iteraties.
Evenzo onthulde BMW de iFE.20 Formula E-racer met een 3D-geprinte koelschacht vervaardigd uit vlasvezels. Het onderdeel werd eind 2019 getoond. In vergelijking met de gebruikelijke koolstofmaterialen heeft vlas een grotere absorptie en grotere slagvastheid, wat voordelig kan zijn op de stratencircuits met hun hobbels en vangrails, waarop de Formule E plaatsvindt. Dit maakte het de eerste BMW-raceauto die werd ingezet door een werkteam met onderdelen gemaakt van hernieuwbare textielvezels, wat hem ook milieuvriendelijk maakt.
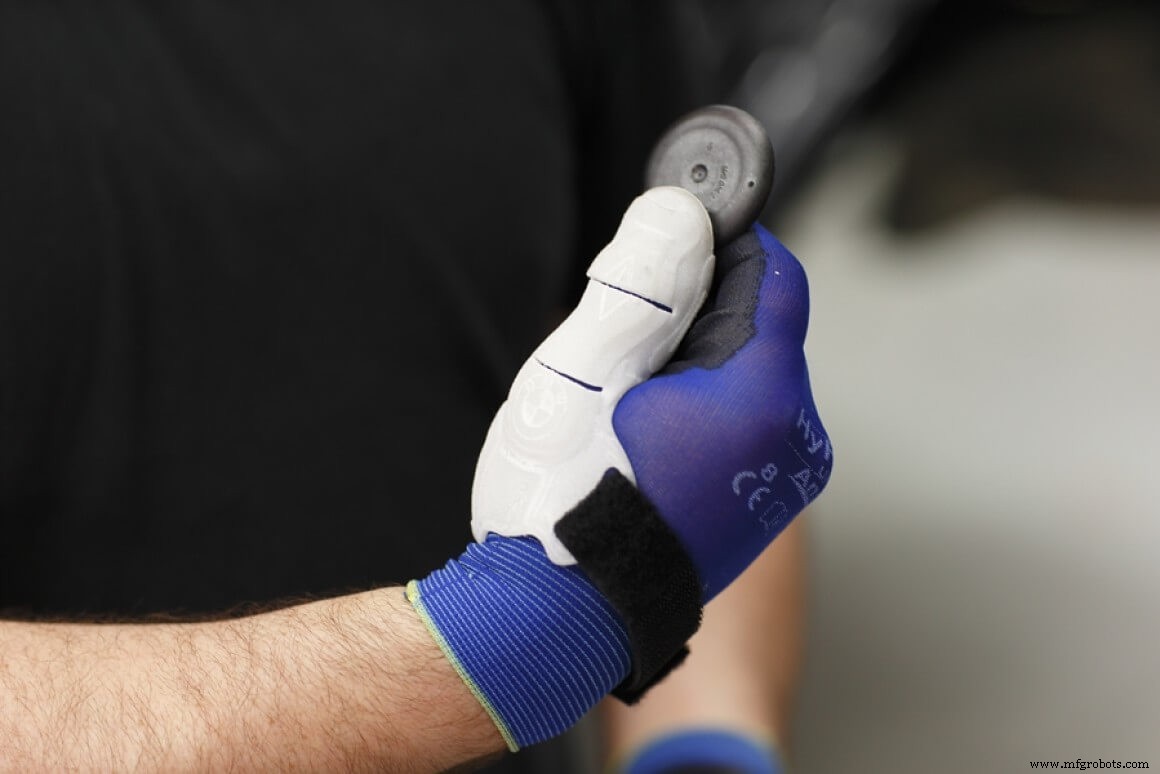
BMW's Handschoenen Met Beschermde Duim
Het bedrijf gebruikt ook 3D-printen voor tooling en veiligheid. Een goed voorbeeld hiervan zijn de gespecialiseerde handschoenen die ze gebruiken om de stoppers voor afvoergaten af te werken. Deze stoppers moeten handmatig worden ingesteld met de vingers van de monteur, wat veel druk op de duimen betekent. Gelukkig kwamen ze met de 3D-geprinte oplossing die op de werkhandschoenen kon worden gepast.
Zelfs afgezien van hun werk aan hun eigen auto's, hebben de ingenieurs van het bedrijf een handje geholpen bij externe projecten. Een voorbeeld is de ontwikkeling van de op maat gemaakte 3D-geprinte stoelen voor het Britse Paralympische basketbalteam. Met behulp van 3D-lichaamsscans en het nieuwste op het gebied van additieve fabricage hebben de ingenieurs van BMW een hele vloot rolstoelen geconstrueerd waardoor spelers een meer geavanceerd niveau van atletisch vermogen kunnen tonen.
Ford
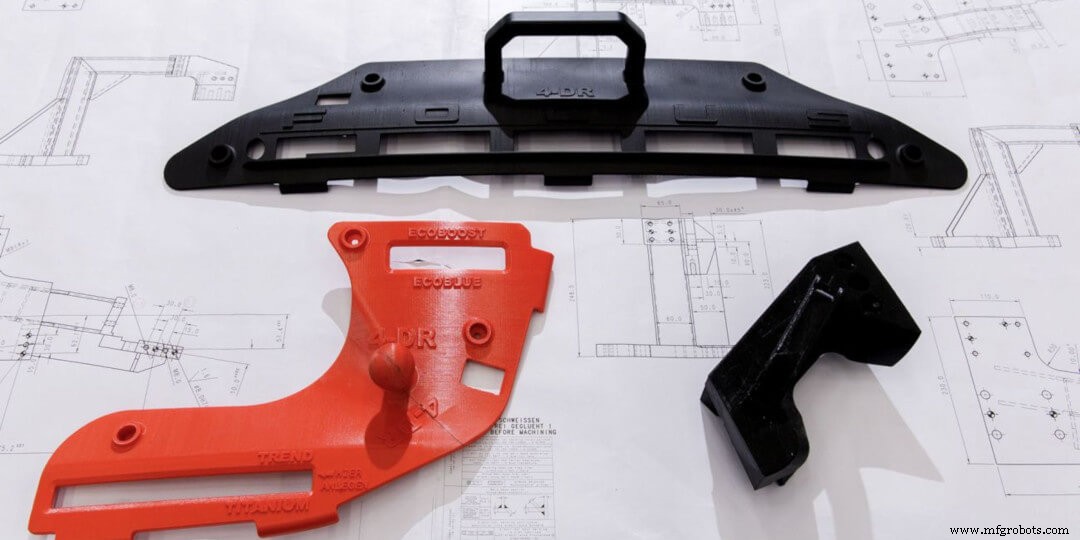
Jigs &Armaturen van Ford
Wat de toewijding aan 3D-printen betreft, loopt Ford voorop in het omarmen van de technologie. Het bedrijf zette een centrum voor additieve productie op en paste zijn activiteiten op grote schaal toe in hun workflows. Op het gebied van het maken van plastic en metalen prints hebben ze een langdurige samenwerking gehad met verschillende bedrijven zoals Ultimaker, Stratasys en GE Additive, die machines leveren voor allerlei AM-toepassingen in de productieketen.
Ze gebruiken ook 3D-printen om kosten en tijd voor gereedschap te besparen, omdat het bedrijf ontdekte dat het sneller was om hun eigen onderdelen in de fabriek te maken in plaats van te wachten op leveranciers en dergelijke. Ze passen dezelfde principes ook toe op mallen en armaturen, die ze in faciliteiten over de hele wereld ontwikkelen.
Ze hebben hun 3D-printactiviteiten in de loop van de afgelopen decennia uitgebreid, waarbij ze zowel metalen als plastic componenten produceren. Zoals het bedrijf stelt:“In de afgelopen decennia heeft Ford meer dan 500.000 onderdelen geprint en miljarden dollars en miljoenen uren werk bespaard. Waar het 4-5 maanden zou hebben geduurd en $ 500.000 zou hebben gekost om een prototype met traditionele methoden te produceren, kan een 3D-geprint onderdeel in een kwestie van dagen of uren worden geproduceerd tegen een kostprijs van een paar duizend dollar ”.
Evenzo hebben de verschillende dochterondernemingen van Ford hun AM-karbonades getoond, met name de ontwerpteams achter de Shelby GT500. Dit jaar hebben ze binnen enkele dagen de meest veelbelovende ontwerpen voor de nieuwe GT500 in 3D geprint, wat de verbeterings- en testfasen enorm versnelde. Dit tempo stelt hen in staat om de Shelby GT500 beetje bij beetje snel aan te passen, waardoor nieuwe fysieke ontwerpen met halsbrekende snelheden worden geïntroduceerd. Ze ontwikkelden ook een nieuw hybride ontwerp met spoilervleugels dat het team 'de schommel' noemt. Dit nieuwe ontwerp is een prominente factor in de indrukwekkende aerodynamische mogelijkheden van de GT500.
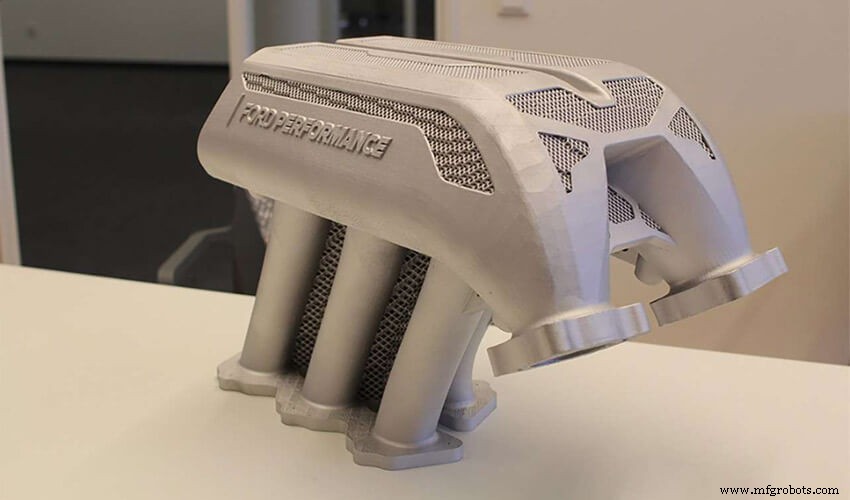
EcoBoost-motor
Het bedrijf zette in februari nog een belangrijke mijlpaal op het gebied van 3D-printen. Hun Ford Performance-divisie, die zich bezighoudt met hoogwaardige componenten, heeft 3D-geprint wat volgens hen het grootste metalen auto-onderdeel is voor een werkend voertuig in de autogeschiedenis. Het metalen onderdeel werd geïnstalleerd in de Hoonitruck, een Ford F-150 uit 1977 met een 3,5-liter V6 EcoBoost-motor met dubbele turbo. Het onderdeel zelf is een aluminium spruitstukinlaat, bedrukt met GE Additive's Concept Laser X LINE 2000R.
Volvo
Hoewel Volvo niet de meest prominente gebruiker van 3D-printen voor auto's is, heeft het de afgelopen jaren grote vooruitgang geboekt op dit gebied. Net als veel van de andere bedrijven op deze lijst, gebruikt Volvo 3D-printen voor tooling en supply chain management. Het gebruik van 3D-printen is met name nuttig geweest bij het aanvullen van de machines van het bedrijf met nieuwe prints voor onderdelen die niet meer in productie zijn. Volvo gebruikt voornamelijk 3D-geprinte plastic onderdelen en kijkt naar de implementatie van metalen onderdelen in de nabije toekomst.
Vanaf 2018 gebruikte het bedrijf additive manufacturing voornamelijk voor prototyping en tooling. "Omdat we slechts kleine hoeveelheden onderdelen hoeven te produceren voor prototyping, is dit een goede manier om te zien wat werkt", zegt Fredrick Andersson, Development Engineer for Wheel Loaders Powertrain Installation bij Volvo CE [construction equipment]. “We hebben veel kennis en kunnen met 3D-printen snel en eenvoudig veranderingen doorvoeren. En hierdoor is de time-to-market voor een nieuw product sneller, dus het is van groot voordeel voor ons bedrijf .”
De verhoogde snelheid van prototyping is enorm nuttig geweest voor het bedrijf, zoals verschillende nieuwe technologieën die ze aan het testen waren bewijzen. De ingenieurs van Volvo ontwierpen bijvoorbeeld nieuwe waterpompbehuizingen voor de A25G- en A30G-voertuigen van het bedrijf. Ze voerden simulaties uit om het ontwerp van interne stroomdoorgangen in de behuizing te optimaliseren, maar moesten een prototype bouwen om functionele tests uit te voeren om het nieuwe ontwerp te valideren. De gereedschapskosten voor dit project zouden ongeveer $ 9.090 zijn geweest, terwijl het onderdeel ongeveer $ 909 kostte. De doorlooptijd voor het produceren van het prototype zou minimaal 20 weken zijn geweest. Aan de andere kant kostte het 3D-printen van het prototype $ 770 en duurde het slechts twee weken.
In 2019 verhoogde het bedrijf echter de lat op het gebied van AM-processen, met name met zijn Volvo Trucks-tak. Hun fabriek in New River Valley (NRV) in Dublin, Virginia haalde dit jaar nogal wat krantenkoppen in de productiewereld. Ze gebruiken voornamelijk SLS, maar hebben zich ook verdiept in andere AM-methoden. Deze specifieke faciliteit produceert meer dan 500 productietools en armaturen die in gebruik zijn op de werkvloer, geproduceerd met behulp van 3D-printen. De faciliteit is ook een belangrijk knooppunt voor Noord-Amerikaanse autotechniek.
Naast commerciële auto's ontwikkelt het bedrijf ook bouwmachines. En ja hoor, 3D-printen heeft ook zijn stempel gedrukt op dit aspect van de activiteiten van het bedrijf. Volvo paste 3D-printing toe bij het ombouwen van hun gelede vrachtwagens, waardoor de kosten van prototyping met een tiende werden verlaagd. Dit stelde hen ook in staat om de tijdsbesteding te verminderen van 20 naar slechts 2 weken.
GM
General Motors, en zijn verschillende andere takken, zijn grote gebruikers (en ontwikkelaars) van 3D-printtechnologie. Vanaf 2018 bespaarde GM $ 300.000 per jaar op gereedschap en boekt het voldoende vooruitgang in de ontwikkeling van nieuwe technologieën met behulp van alternatieve brandstofbronnen. De toonaangevende autofabrikant kondigde vorig jaar aan van plan te zijn tegen 2023 wereldwijd 20 nieuwe elektrische en brandstofcelmodellen te lanceren.
Hoewel hun 3D-printactiviteiten grotendeels over prototyping gingen, breiden ze uit. Het bedrijf is van plan om hun printactiviteiten op te schalen om "tienduizenden onderdelen op schaal te produceren naarmate de technologie verbetert ”, aldus Kevin Quinn, directeur additief ontwerp en fabricage bij GM. Dit plan zal zich waarschijnlijk in de komende 5 jaar ontvouwen.
Het Warren Tech Center van het bedrijf produceert jaarlijks ongeveer 30.000 prototypeonderdelen. De onderdelen bestaan uit maar liefst negen soorten materialen, waarbij gebruik wordt gemaakt van combinaties van kunststoffen en metaal en poeders. Ze worden voornamelijk gebruikt voor prototyping, maar het bedrijf kijkt ook naar onderdelen voor eindgebruik. Ze zijn ook mede-eigenaar van HRL-laboratoria met Boeing, die eindigde met het produceren van een 3D-geprinte aluminiumlegering.
Dan Grieshaber, GM's directeur van wereldwijde productie-integratie, verklaarde dat de meeste fabrieken van GM nu 3D-printers hebben. Het bedrijf is van plan om het nog verder te verhogen, in ieder geval binnen hun Noord-Amerikaanse fabrieken. De verhuizing zal GM waarschijnlijk jaarlijks miljoenen dollars aan productiekosten besparen. GM is al lang een investeerder in 3D-printen en zijn verschillende subtaktechnologieën. Ze passen het toe voor het snel bouwen van gereedschappen en accessoires voor werknemers in hun fabrieken. Dit jaar nog verklaarde het bedrijf dat de implementatie van een 3D-printmachine van $ 35.000 het bedrijf in twee jaar tijd $ 300.000 heeft bespaard. Hoewel de productie van gereedschappen de primaire rol is die de printer speelt, is het mogelijk dat het bedrijf de rol van additive manufacturing in hun dagelijkse activiteiten zal vergroten.
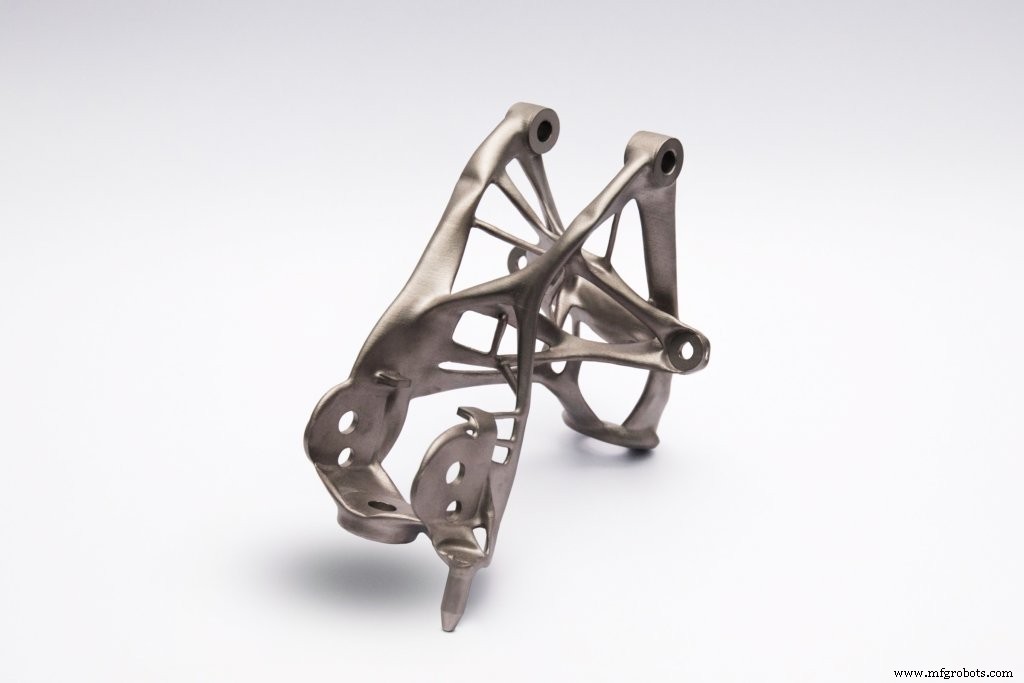
GM's Bracket ontwikkeld in samenwerking met Autodesk
Hun samenwerking met Autodesk is gunstig geweest voor de productie van lichtgewicht 3D-geprinte onderdelen die de autofabrikant zouden kunnen helpen zijn doelen te bereiken om voertuigen op alternatieve brandstof aan zijn productassortiment toe te voegen. Als onderdeel van dezelfde samenwerking toonden beide bedrijven in 2019 een 3D-geprinte stoelbeugel van roestvrij staal, ontwikkeld met de Autodesk-technologie.
Begin 2019 was GM op zoek naar een nieuwe ontwerptoepassing voor 3D-printen. In samenwerking met Michellin waren ze op zoek naar een nieuw type band met superieure duurzaamheid. De Uptis-band is nog steeds een werk in uitvoering, maar de bedrijven zijn overgegaan naar de testfase. Ze beweren dat de banden 100 procent duurzaam en resistent zijn en zelfs nog langer meegaan. Ze zijn ook een veel groener alternatief, met minder afval tijdens de productie. Onlangs gebruikten ingenieurs een vloot van Chevrolet Bolt EV's om de nieuwe banden in Michigan te testen en hebben ze de mogelijkheid geopperd om ze in 2024 voor het publiek beschikbaar te maken.
Porsche
Porsche gebruikt 3D-printen voor verschillende doeleinden, van belangrijke componenten tot het opnieuw uitvinden van de toeleveringsketen voor hun oudere modellen. Porsche gebruikt momenteel 3D-printen om zeer specifieke reserveonderdelen te produceren, maar niet zo uitgebreid. Dit komt door de strenge kwaliteitsnormen die ze moeten hanteren om de veiligheid op peil te houden. Het bedrijf werkt ook met een lager totaal aantal geproduceerde eenheden omdat ze meer van een klassiek en luxe automerk zijn.
Voor de ontwikkeling van onderdelen die niet meer in productie zijn, zoals de ontgrendelingshendel voor de koppeling van de Porsche 959, past het bedrijf lasersmelten toe. Ze maken gebruik van gepoederd gereedschapsstaal en halen het onderdeel er veel efficiënter uit dan anders mogelijk zou zijn met alternatieve methoden.
Het gebruik van 3D-printen heeft het bedrijf ook in staat gesteld om over te stappen op on-demand printen, waardoor veel lagere kosten voor materialen, transport en opslag mogelijk zijn. Dit is ook gunstig omdat er niet veel vraag naar deze onderdelen is en het vaak duur is om ze constant in productie te houden. Porsche heeft het meest bekend om de samenwerking met Markfordged om deze klassieke onderdelen nieuw leven in te blazen.
Ze gebruiken voornamelijk SLM en SLS voor de verschillende onderdelen die ze moeten produceren. Porsche heeft verklaard dat de 3D-geprinte onderdelen in veel gevallen superieur zijn aan de oudere. Hoewel ze momenteel een beperkt aantal onderdelen printen, hebben ze de portfolio sinds 2018 uitgebreid en toekomstige componenten getest.
CNC machine
- Hoe gebruiken we molybdeen?
- Hoe duurzaam is industrieel 3D-printen?
- Een functie gebruiken in VHDL
- Een procedure gebruiken in VHDL
- Hoe gebruikt u onze website?
- Hoe een acrylsnijmachine te gebruiken om acryl te snijden?
- Gereedschapssensor van Wood Cnc-router, hoe te gebruiken?
- Hoe 3D-printen wordt gebruikt in de matrijsindustrie
- Hoe fabrikanten Analytics kunnen gebruiken voor een betere klantervaring
- Hoe werkt offsetdruk?
- Hoe een snijmolen te gebruiken