Polymeer 3D-printen:6 innovatieve voorbeelden van de technologie in actie verkennen
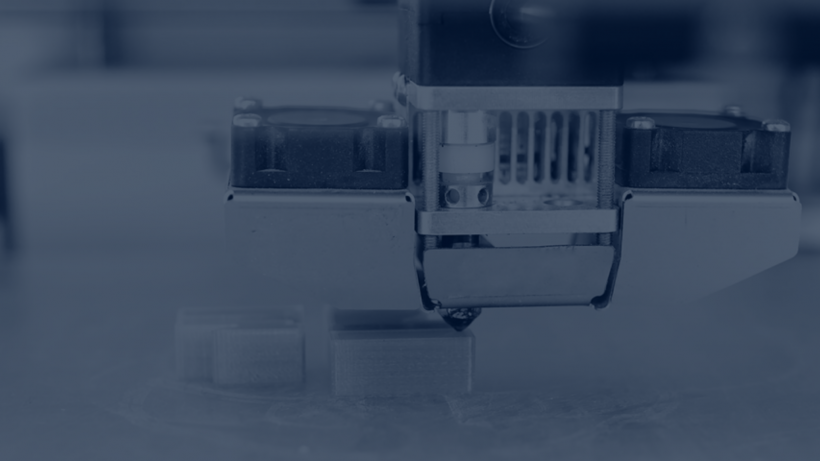
Bedrijven in bijna alle sectoren passen polymeer 3D-printen toe om innovatie in productontwerp, ontwikkeling en productie te stimuleren.
Vandaag bekijken we 6 voorbeelden van recente innovaties, mogelijk gemaakt dankzij polymeer 3D-printen, om te ontdekken hoe de technologie het spel verandert voor bedrijven in de automobiel-, medische en consumptiegoederensectoren.
1. Autostoelen aanpassen
Het ontwikkelen van innovatieve 3D-printtoepassingen is niets nieuws voor de auto-industrie. Een recent voorbeeld komt van een luxe autofabrikant, Porsche.
Eerder dit jaar introduceerde het bedrijf een nieuw concept voor sportwagenstoelen dat gebruikmaakt van 3D-printen en roosterontwerp.
De nieuwe stoelen zijn voorzien van 3D-geprinte centrale zit- en rugleuningkussensecties, geproduceerd met thermoplastisch polyurethaan, ook wel bekend als TPU, een zacht, rubberachtig plastic. Door dit flexibele materiaal te gebruiken, kunnen stoelen worden aangepast met 3 stevigheidsniveaus:hard, medium en soft.
Het 3D-geprinte gebied heeft een roosterachtige structuur en is gebonden aan een plastic schaal en bedekt met Porsche's ademende Racetex mesh-bekledingsmateriaal. Nou, niet helemaal bedekt - Porsche laat, wat het noemt, 'raampanelen' achter, waardoor de roodgekleurde 3D-geprinte dempingslaag zichtbaar wordt, zoals je kunt zien in de afbeelding hierboven.
Voor deze toepassing liet de Duitse autofabrikant zich inspireren door de motorsportsector, waar op maat gemaakte bestuurdersspecifieke stoelmontage de norm is.
Er zijn 3D-geprinte volledige kuipstoelen beschikbaar sinds mei 2020 voor 40 spoorbestuurders. Porsche verzamelt nu feedback van klanten die het zal gebruiken om de laatste straatlegale stoelmodellen voor medio 2021 te ontwikkelen. stoel naar de specifieke lichaamscontour van een klant. 3D-printen blijft momenteel de enige technologie die dit niveau van maatwerk mogelijk maakt.
2. Veiligere fietshelmen ontwikkelen
3D-printen van sportartikelen kent een groeiende belangstelling van veel consumentenmerken. Een zo'n merk is HEXR, een Brits bedrijf dat op maat gemaakte fietshelmen maakt met behulp van 3D-printen en 3D-scannen.
Hoewel het niet de eerste fietshelm is die 3D-geprint is, is de debuuthelm van HEXR de eerste die gebruikmaakt van Polyamide 11, een stevig nylon materiaal.
Traditioneel worden binnenvoeringen van helmen gemaakt van geëxpandeerd polystyreenschuim (EPS). Het HEXR-team was echter van mening dat de op maat gemaakte nylon fietshelmen rijders betere bescherming bieden dan helmen op basis van schuim. Om dit te bewijzen vergeleek het bedrijf hun PA 11-helmen met andere fietshelmen in snelheids- en acceleratietests. HEXR beweert dat hun helm gemiddeld 30 procent beter heeft gepresteerd op een steekproef van meer dan 40 helmen.
De sleutel tot het succes van de nylon helm is het op maat gemaakte, honingraatontwerp, gestructureerd om te verdrijven de energie. Dit helpt om de energie over een groter gebied te verspreiden en het risico op ernstig letsel te voorkomen.
3D-printen en 3D-scannen gaan hand in hand om dit ontwerp mogelijk te maken. Het team van HEXR gebruikt een 3D-scan naar 3D-printworkflow die een mobiele aanpasapp, EOS' polymeer Selective Laser Sintering-technologie (SLS) en plantaardige materialen van Arkema combineert.
Volgens HEXR, 3D-printen is de enige manier om de honingraat en ingewikkelde holtes te creëren voor verwijderbare opvulling, schelpen, riemen en andere elementen. Bovendien vereist 3D-printen geen mallen, wat betekent dat elke helm kan variëren zonder extra kosten.
In navolging van zijn mantra 'Geen twee hoofden zijn hetzelfde, dus waarom zouden helmen dat ook zijn?', gelooft HEXR in de waarde van op maat gemaakte helmen - en snel voortschrijdende 3D-printtechnologieën helpen deze visie te verwezenlijken.
3. Een verbeterde rijervaring met 3D-geprinte zadels
De wielerwereld lijkt bijzonder gastvrij te zijn voor 3D-printtechnologieën. Terwijl sommige bedrijven helmontwerpen opnieuw uitvinden, gebruiken anderen 3D-printen om superieure fietszadels te ontwikkelen.
Bij het fietsen staat comfort voorop, maar de meeste zadels moeten nog de balans vinden tussen comfort, prestatie en stabiliteit.
Een manier waarop 3D-printen kan helpen, is door het intelligente ontwerp in staat te stellen de prestaties en het comfort van het zadel te verbeteren.
De ontwikkelaar van 3D-printtechnologie, Carbon, is een samenwerking aangegaan met een fietsbedrijf, Fizik, om fietszadelontwerpen te innoveren door middel van digitale productie.
Door de 3D-printtechnologie van Carbon, genaamd Digital Light Synthesis (DLS), en de expertise van Fizik te combineren, waren de bedrijven in staat om meerdere functionele zones in het zadel te ontwerpen en te vervaardigen, waarbij ze elk afzonderlijk werden verfijnd. voor specifieke mechanische eigenschappen.
Dit betekent dat elke zone een onderscheidende demping en mechanische respons heeft. Het midden biedt bijvoorbeeld ondersteuning bij het trappen op de kappen en de achterkant is zacht gedempt voor meer achterwaartse posities.
Een combinatie van 3D-printen, intelligent ontwerp en drukmapping heeft geholpen om het zadel te verbeteren prestatievoordelen bieden, zoals een lager gewicht, ademend vermogen en verbeterd comfort.
Fietsers zijn voortdurend op zoek naar manieren om hun rijervaring en prestaties te verbeteren, en 3D-printen lijkt een haalbare oplossing in hun gereedschapskist te worden.
4. Een slimmer ontwerp voor snowboardbindingen
Om ons sportthema voort te zetten, zijn polymeer 3D-printen en kunstmatige intelligentie (AI) onlangs gecombineerd om, misschien wel de slimste, snowboardbinding te creëren.
Bij snowboarden bieden bindingen een directe verbinding met een snowboard en om de beste rijervaring te garanderen, moeten ze goed zijn afgestemd op het board en de stijl van de rijder.
Snowboardmerk Now en het Spaanse 3D-printbedrijf Addition hebben hun kennis en vaardigheden gecombineerd om 's werelds eerste AI-ontworpen en 3D-geprinte binding te realiseren.
Met behulp van computersimulatie en generatieve ontwerptools kon het team een belastingsgeval bouwen dat de spanning nabootste die bindingen ondergaan tijdens agressief carven en draaien.
Na uren van simulatie en data-analyse kwamen de bedrijven met het definitieve ontwerp dat gedrukt moest worden in nylon 12, met behulp van polymeerpoederbedfusietechnologie (PBF).
Maar wat heeft de 3D-geprinte en AI-ontworpen binding te bieden? Allereerst is het 25 procent lichter dan traditionele bindingen. Een vermindering van het gewicht heeft een positief effect op de reactie van de binding. Dit betekent dat de bindingen zorgen voor directe randcontrole en dus krachtigere bochten.
Natuurlijk was het niet zomaar een bevlieging om 3D-printen te gebruiken om de binding te maken. Het bleek simpelweg een fabricagemethode te zijn die goed past bij ontwerpen die zijn gemaakt met behulp van generatieve ontwerptools.
3D-printen, in combinatie met geavanceerde ontwerpsoftware, heeft zeker de weg vrijgemaakt voor een nog innovatievere, geoptimaliseerde en meer op maat gemaakte productontwikkeling in de snowboardindustrie.
5. 3D-geprinte wattenstaafjes vullen het gat in COVID-19-testkits
Als het gaat om het stoppen van de COVID-19-crisis, is virustesten essentieel voor het diagnosticeren en volgen van de epidemie. Maar veel landen vinden het nog steeds moeilijk om de testcapaciteit te vergroten, niet in de laatste plaats vanwege het gebrek aan testkits - de lange neusuitstrijkjes en chemicaliën die nodig zijn om ze te verwerken.
3D-printen – vooral met harsen – bleek een van de oplossingen te zijn voor de productie van neusswabs, omdat ze snel, goedkoop en op grote schaal kunnen worden geproduceerd.
3D-printen heeft aangetoond dat het kan worden gebruikt als een levensvatbare productiemethode wanneer er verstoringen in de toeleveringsketen zijn of de traditionele productie beperkt is.
In het geval van de neusuitstrijkjes, Op hars gebaseerde 3D-printers en materialen die zijn ontwikkeld voor de tandheelkundige industrie zijn aangepast voor de productie van neusuitstrijkjes. 3D-printen met hars is een proces met hoge resolutie dat geschikt is voor de fijne kenmerken van een neusuitstrijkje. Bovendien hebben veel 3D-printers van tandheelkundige hars gecertificeerde biocompatibele materialen die meteen kunnen worden gebruikt.
Veel hars 3D-printerbedrijven, van Formlabs en Carbon tot EnvisionTEC en Origin, hebben neusswabs 3D-geprint voor COVID-19-tests, en miljoenen swabs zijn al naar ziekenhuizen over de hele wereld verzonden.
3D-geprinte neusuitstrijkjes vormen een aanvulling op de lijst van andere essentiële benodigdheden die nog steeds schaars zijn, waaronder 3D-geprinte gelaatsschermen, ademhalingstoestellen en ventilatoren. 3D-printen kan een unieke kans bieden om aan deze dringende behoeften te voldoen en de acceptatie van digitale productie in de medische industrie als geheel te stimuleren.
6. De toekomst van 3D-geprinte stoffen
Hoewel polymeer 3D-printen in meerdere industrieën wordt gebruikt, moet het potentieel ervan in de textielsector nog volledig worden gerealiseerd. Een ontwikkeling van Polymer-specialisten, Polymaker en Covestro, kan de acceptatie van 3D-printen voor kleding echter aanzienlijk versnellen.
Tot voor kort waren 3D-printbare synthetische materialen, zoals polymelkzuur (PLA), niet flexibel en comfortabel genoeg om als textiel te worden gebruikt. In de meeste gevallen wordt de technologie in de mode-industrie gebruikt om stijve elementen te creëren die bovenop conventionele stoffen worden toegevoegd.
De nieuwe aanpak van Polymaker en Covestro kan echter veranderen hoe 3D-printen wordt gebruikt in de textiel- en mode-industrie.
In samenwerking met fabrikanten van 3D-printers hebben de twee bedrijven een nieuwe technologie ontwikkeld voor 3D-geprinte stoffen. Deze technologie omvat hardware (flexibele materiaal gespecialiseerde 3D-printers), flexibele materialen zoals TPU en nieuwe ontwerpsoftware specifiek voor stofontwikkeling.
Deze combinatie maakt de productie van 2D-stoffen mogelijk, meestal slechts 2 tot 5 lagen dik , die vervolgens worden geïntegreerd in de bestaande workflow om kledingstukken zoals hoeden, schoenen en handschoenen te maken. Een van de belangrijkste voordelen van dit proces is dat het 3D-geprinte stuk stof geen overtollige stof produceert die moet worden afgesneden en weggegooid, wat resulteert in minder verspilling.
Tot nu toe waren 3D-geprinte stoffen in wezen wetenschappelijke en mode-experimenten, met weinig praktische waarde. De recente ontwikkeling van Polymaker en Covestro opent de mogelijkheid om 3D-printen te gebruiken bij de productie van textiel, waardoor 3D-geprinte stoffen uiteindelijk uit laboratoria en modeshows kunnen worden gehaald en in echte consumententoepassingen worden gebracht.
Polymeer 3D-printen:bedrijven in staat stellen te innoveren
Hoewel we zes voorbeelden van innovatieve 3D-printtoepassingen hebben behandeld, is dit slechts het topje van de ijsberg:het aantal gebruiksscenario's voor 3D-printen met polymeren groeit met grote sprongen.
Met rijpende polymeer 3D-printtechnologieën en een steeds groter wordende materiaalkeuze, is er een belangrijke kans om uitstekende items te ontwikkelen met 3D-printen en de verandering in uw branche te leiden.
3d printen
- Stereolithografie — de originele 3D-printtechnologie
- Polyjet 3D-printen verkennen
- 3D-printen van plastic in de ruimte — het nieuwste van Made in Space
- Het 3D-geprinte 'Iron Man'-pak — een perfect voorbeeld van rapid prototyping in actie
- 6 manieren om de kosten van 3D-printen te verlagen
- Interview met expert:VELO3D's VP of Technology Partnerships over uitbreiding van de mogelijkheden van 3D-metaalprinten
- 10 spannende voorbeelden van 3D-printen in de auto-industrie in 2021
- De zekering 1 afdrukken met de zekering 1
- Evonik vestigt nieuw 3D-printtechnologiecentrum in de VS
- De toekomst van 3D-printen in de maakindustrie
- Is 3D-printen de toekomst van productie?