Plant Tour:STELIA Aerospace, Méaulte, Frankrijk
Met 7.000 medewerkers wereldwijd en een omzet van € 2,2 miljard in 2018, geeft STELIA Aerospace (Toulouse, Frankrijk) duidelijk zijn belangrijkste product- en industriepositie aan:nr. 1 in Europa/nr. 3 in de wereld voor vliegtuigconstructies, nr. 1 wereldwijd voor stoelen voor piloten en bemanningsleden en nr. 3 wereldwijd voor passagiersstoelen in de eerste en zakelijke klasse.
Het gebruik van composieten door STELIA Aerospace strekt zich uit tot de voorste rompsecties van de Airbus A350, vleugels voor ATR-turbopropvliegtuigen, verschillende helikopterconstructies en in sommige stoelproducten, waaronder de nieuwste OPAL-stoel. De productiefaciliteiten voor composieten omvatten de Franse vestigingen Méaulte (grote rompdelen) en Salaunes (kleinere composietonderdelen), gedetailleerde onderdelen en assemblage in Marokko en Tunesië en een breed scala aan composietonderdelen voor vliegtuigen, defensie en ruimtevaart op de vorige Composites Atlantic-locatie in Lunenburg, Nova Scotia, Canada.
STELIA Aerospace is ontstaan uit de fusie in 2015 van twee eerdere Airbus-dochterondernemingen - Aerolia en Sogerma. De vestiging in Méaulte, op 1,5 uur rijden ten noorden van Parijs, beslaat 49 hectare met 150.000 vierkante meter productieruimte, 1.500 werknemers en 500 onderaannemers en is een belangrijk onderdeel van de toeleveringsketen van Airbus. De locatie in een klein stadje logenstraft een productiekrachtpatser, "die in 2018 860 neusrompdelen voor de A320, A330, A350, A380 en A400M leverde", zegt STELIA Méaulte-communicatiemanager Francois Fournier. Hij is mijn gids door de "Factory of the Future" A350-neusrompproductie en de STELIALAB R&T-faciliteit, vergezeld door Olivier Canal, STELIA Aerospace Méaulte hoofd van R&T-productie, assemblage en automatisering, composieten en digitale fabriek, en Simon Maire-Vigeur , hoofd R&T-composietproductie, STELIALAB.
'Fabriek van de toekomst'
Tijdens een inleidende presentatie in het hoofdkantoor van de locatie legt Fournier uit dat STELIA Aerospace heeft geïnvesteerd in toekomstige technologieën, zoals digitale productie en automatisering, waaronder augmented reality/virtual reality die wordt gebruikt om de efficiëntie in de productie te verhogen en robots/cobots voor efficiëntere assemblage.
“De toekomst is composieten en metalen constructies”, merkt Canal op. "We proberen toekomstige oplossingen te definiëren, niet om onze werknemers te vervangen, maar om ze efficiënter te maken."
Dit streven naar efficiëntie wordt misschien het best geïllustreerd door het initiatief 'Factory of the Future' dat vijf jaar geleden is gestart om de oprijplaten in de A320- en A350-productie te ontmoeten. "We omarmden een nieuwe industriële strategie voor deze site", herinnert Canal zich, die projectmanager was voor het initiatief. "We wilden de mogelijkheid hebben om te voldoen aan variabele productiesnelheden en ontwikkelden flexibele tooling die we van het ene programma naar het andere konden hergebruiken."
Een ander resultaat van deze heroverweging was het wijden van gebouwen aan specifieke programma's. "Elk zou één lijn en één team hebben", zegt Canal, "en ontworpen zijn met een lean manufacturing-aanpak die zich richt op het elimineren van verspilling in arbeid, beweging, materialen en processen." STELIA Aerospace heeft ook de A320-lijn opnieuw ontworpen en de productiviteit met 10-20 procent verbeterd, "wat eigenlijk een aanzienlijke verbetering is", zegt Canal. "We hebben dit in 2,5 jaar bereikt, waarbij we meer dan 50 procent van de voetafdruk van de productie van deze site hebben veranderd, terwijl de productie en gehandhaafd blijft. 100 procent stipte levering zonder kwaliteitsverlies.” Dit succes wordt toegeschreven aan de steun van het management op hoog niveau, "maar we hebben ook hard gewerkt om de arbeiders eigenaar te maken", merkt hij op.
Canal legt uit dat het ontwerp van het 30.000 vierkante meter grote A350-productiegebouw werd bepaald door de stroming, geïllustreerd in de U-vorm, waarbij grondstoffen aan het ene uiteinde binnenkwamen en afgewerkte rompdelen het andere uiteinde verlieten. “Alles voor de productie van onze A350-constructies is in dit gebouw, van de eerste lay-out tot de uiteindelijke montage. Dit is bijvoorbeeld belangrijk om eventuele kwaliteitsproblemen snel en gemakkelijk te kunnen identificeren en oplossen”, zegt hij.
Voor de A350 produceert STELIA Aerospace de neusrompsectie 11, die volledig van metaal is om schade door vogels beter te weerstaan, evenals de complexe hybride metaal/composietconstructie voor sectie 12 en de sectie 11/12 onderste eenheid, die de neus omvat landingsgestel. Fournier toont de video "Factory of the Future" van STELIA Aerospace, waarbij hij wijst op de gepulseerde lijn, zoals die wordt gebruikt voor auto-assemblage. "We hebben een demolijn opgezet om de arbeiders in staat te stellen deze bewegende lijn te trainen en demystificeren, die op een specifieke takt-tijd werkt om aan de volledige productie te voldoen", zegt Canal.
Een ander aspect was digitale technologie. "Dankzij digitale oplossingen konden we alle technische schema's en stappen op een tablet zetten en ervoor zorgen dat elke sectie toegang had tot de nieuwste 3D-mockup", zegt Canal. Zo worden werknemers op de hoogte gehouden van cruciale details en wijzigingen, terwijl managers gemakkelijk op de hoogte worden gehouden van mogelijke problemen. "We hebben ook augmented reality ontwikkeld om de montage te vergemakkelijken, bijvoorbeeld door projectie op de rompschalen te laten zien welke onderdelen en waar de bevestigingen moeten worden gemaakt", merkt Canal op. Hij voegt eraan toe dat inspectie cobots worden gebruikt om 3D-scans van voltooide secties te voltooien die vervolgens worden vergeleken met de digitale mockup, waarbij eventuele vreemde objecten of ontbrekende onderdelen, kwaliteitsproblemen, enz. worden geïdentificeerd.
Onze rondleiding begon in de cleanroom van het A350-productiegebouw, waar Coriolis (Quéven, Frankrijk) geautomatiseerde vezelplaatsingsmachines (AFP) grote met koolstofvezel versterkte polymeer (CFRP) rompschalen voor de sectie 11/12 onderste eenheid en de kroon legden en twee zijschalen voor sectie 12. Deze schalen worden vervolgens gekoppeld aan geprefabriceerde stringers, vacuümzakken en gehard in een autoclaaf. Na uitharding worden ze bijgesneden en geladen op handlingtools die gemakkelijk transport door alle stappen voor montage mogelijk maken, inclusief robotboren en installatie van bevestigingsmiddelen. Elk paneel wordt geïnspecteerd met behulp van geautomatiseerd niet-destructief onderzoek (NDT). Voltooide assemblages worden geleverd aan de Airbus-rompassemblagelijn in Saint Nazaire, Frankrijk.
STELIALAB
De volgende halte is het 2000 vierkante meter grote STELIALAB R&T-centrum, dat de linkerhelft van IndustriLAB beslaat, een regionale technologie- en trainingsfaciliteit net ten zuiden van het STELIA-gated complex. De activiteiten van STELIALAB zijn gericht op composieten, assemblage en digitale technologieën.
De tour begint hier opnieuw in de salle blanche (schone ruimte), een vrij grote, open ruimte met opbergbenodigdheden en opmaakhulpmiddelen. Simon Maire-Vigueur legt uit dat het de missie van de groep is om de toekomst te identificeren voor goedkope, grootschalige productie van voornamelijk grote en complexe onderdelen. De industrialisatie van thermohardende composieten omvat snelle AFP- en vloeibare harsinfusieprocessen (LRI), waaronder harstransfervormen (RTM), voor grote, gesloten doosstructuren zoals vleugelcomponenten, horizontale staartvlakken en verticale staartvlakken.
Bij het verlaten van de cleanroom komen we in de AFP-ruimte waar een Coriolis-machine staat die onderdelen tot 4 meter lang kan leggen. Gewijd aan R&T, merkt Maire-Vigueur op dat het meer dan 200 dagen per jaar bezet is. STELIALAB heeft een proces ontwikkeld voor het integreren van door AFP gemaakte droge verstijvingen en huiden die worden uitgehard uit autoclaaf (OOA) met behulp van een oven of zelfverwarmde gereedschappen. "We geven de voorkeur aan LRI met een lagere injectiedruk omdat we goedkoper gereedschap kunnen gebruiken", zegt Maire-Vigeur.
TPC-wegenkaart
Deze AFP-machine werd ook gebruikt om de huid op te leggen voor de volledig thermoplastische composiet (TPC) helikopterromp/tailboom-demonstrator als onderdeel van het ARCHES TP-ontwikkelingsprogramma. Getoond op de Paris Air Show 2017 en ook op JEC World in 2018 en 2019, werd het gemaakt met behulp van 8 kabels van 0,25 inch brede koolstofvezel/polyetherketoneketon (PEKK) tape met laserverwarming. "We hebben de blikseminslagbeveiliging geïntegreerd met de AFP tijdens de lay-up", merkt Maire-Vigeur op. "De huid is OOA-genezen met Kapton-zakfolie, wat eigenlijk niet erg handig is." Omega-vormige stringers werden gemaakt van gekochte platte panelen met unidirectionele tape die door Aviacomp (Toulouse, Frankrijk) werden gestempeld. Hetzelfde proces werd gebruikt voor frames, maar met behulp van platen gemaakt van geweven materiaal geleverd door Porcher (Badinières, Frankrijk) en gestempeld in Cetim (Nantes, Frankrijk). Hoewel de frames op standaard wijze mechanisch werden bevestigd, werden de stringers bevestigd met behulp van geautomatiseerd, dynamisch inductielassen. "Dit zorgt voor lagere kosten en nieuwe ontwerpmogelijkheden", merkt Maire-Vigeur op. "We hebben ook overmolding gedemonstreerd voor bevestigingspunten, zoals voor elektrische harnassen."
Gevraagd naar de uitdagingen van het programma, noemt Maire-Vigueur de lay-ups, het lassen en de tijdlijn van 15 maanden. "Zelfs het stempelen zonder al te veel vervorming in het geweven materiaal was niet eenvoudig", voegt hij eraan toe. Hoewel het ontwerp van de staartboom werd voltooid door het ontwerpbureau van STELIA Aerospace in Toulouse, stond de hele productie onder toezicht van STELIALAB. ARCHES TP was echter slechts één stap in de routekaart voor thermoplastische composieten van STELIA Aerospace. Het bedrijf blijft TPC-technologieën ontwikkelen om de haalbaarheid van een volledige TPC-romp in de volgende jaren aan te tonen.
Een nieuwe kijk op toekomstige luchtvaartstructuren
Bij het verlaten van de AFP-kamer gaat de rondleiding verder door een zeer grote, open hal die is opgedeeld in veilige "ontwikkelingscellen" door tijdelijke muren om intellectueel eigendom te beschermen. Als we door de hal lopen en naar links gaan, bereiken we een gebied met een kleine Scholz (Coesfeld, Duitsland) autoclaaf die geschikt is voor 450°C, en een injectiemachine voor harsinfusie. "Omdat het onze routekaart is om OOA te genezen, gebruiken we de autoclaaf eigenlijk als een oven, waarbij thermoplastische composieten zonder druk worden uitgehard", legt Maire-Vigueur uit. Er is een trimkamer met gordijnen en een ruimte ernaast met NDT-apparatuur, waaronder een klein C-scan-systeem.
We draaien weer om en gaan een groot testlaboratorium binnen. "We kunnen gepolijste doorsneden bestuderen voor kwaliteitscontrole en materiaal- en procesonderzoeken", zegt Maire-Vigeur. Het laboratorium beschikt ook over een Romer (Hexagon Manufacturing Intelligence, Shropshire, U.K.) arm voor coördinatenmeting en apparatuur voor vezelvolumeverhouding, hardheid en chemische testen. "Alle ingenieurs in ons R&T-team kunnen hun eigen materiaal- en procescontrole uitvoeren", merkt Maire-Vigueur op. “We leiden ze op om te kunnen werken van ontwerp tot fabricage tot inspectie en testen van definitieve onderdelen. Dit is belangrijk om het hele proces te begrijpen en maakt een snelle beoordeling van vermoedelijke problemen en hun oorzaken mogelijk. Ontwerp staat niet los van fabricage en kwaliteitstesten.”
De laatste stop is een groot automatiseringslab binnen een van de ommuurde ruimtes. Een korte blik binnenin toont werk dat nieuwe assemblage met robots en cobots verkent. "We kijken naar de verdere ontwikkeling van kleinere, functionelere gereedschappen en proberen ons voor te stellen hoe je onderdelen sneller en tegen lagere kosten kunt samenstellen", zegt Canal. “Onze cultuur is er een van grenzen verleggen en nieuwe wegen inslaan. We waren een leider in het implementeren van robotica en nu zijn we een leider in het pushen van composiettechnologie. We hebben laten zien dat we in staat zijn om de toekomst te heroverwegen en opnieuw voor te stellen en we zullen nooit stoppen.”
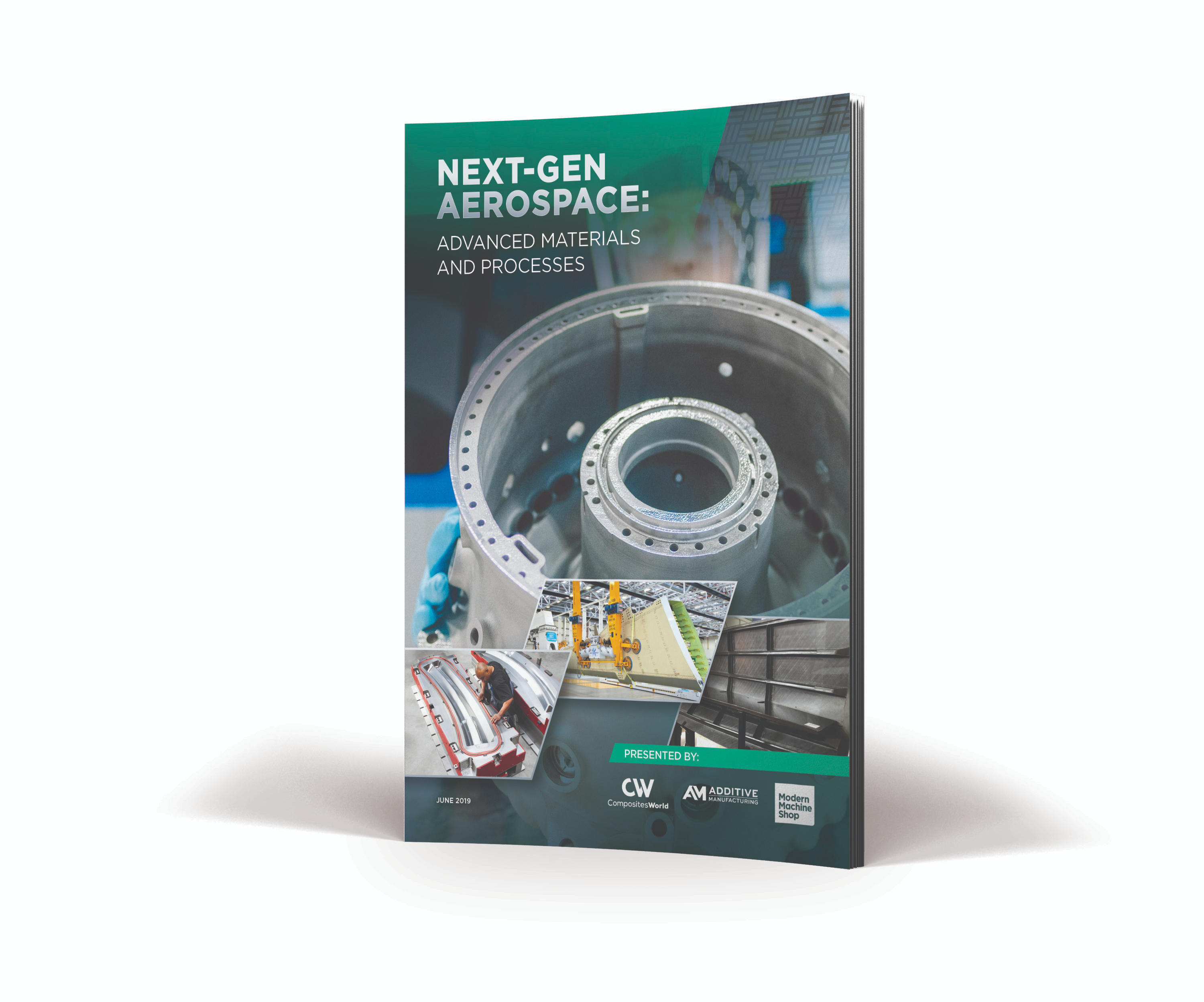
De volgende generatie lucht- en ruimtevaartfabricage
Aangezien de commerciële luchtvaartindustrie naar verwachting in de komende 20 jaar zal verdubbelen, zijn nieuwe technologieën en ongekende productiesnelheden nodig om aan de vraag naar passagiers- en vrachtvliegtuigen te voldoen.
Leer meer over de materialen en processen die de volgende generatie vliegtuigen zullen vormen in een verzameling verhalen van CompositesWorld, Modern Machine Shop en Additieve productie , beschikbaar om gratis te lezen of te downloaden . Download het hier.
Hars
- Vespel®:het ruimtevaartmateriaal
- Polyplastics breidt productie Topas COC uit
- Radici breidt de wereldwijde productiecapaciteit aanzienlijk uit
- Polykemi investeert in eigen Amerikaanse compounderingsfabriek
- Rethink Robotics krijgt nieuw hoofdkantoor en nieuwe productie-installatie
- Toyota kiest locatie in North Carolina voor productie-installatie voor EV-batterijen
- Fabrikanten bezoeken Southco voor fabrieksrondleiding, discussie over continue verbetering van best practices
- Arkema Inc. bouwt Amerikaanse PEKK-productiefabriek
- Hexion introduceert tweecomponenten epoxyoplossing voor de productie van composieten in de ruimtevaart
- Kaneka Aerospace behaalt AS9100D ruimtevaartcertificering
- Consortium thermoplastische composieten streeft naar productie in hoog volume voor Automotive en Aerospace