Nabewerking voor industrieel 3D-printen:belangrijkste trends die u moet kennen
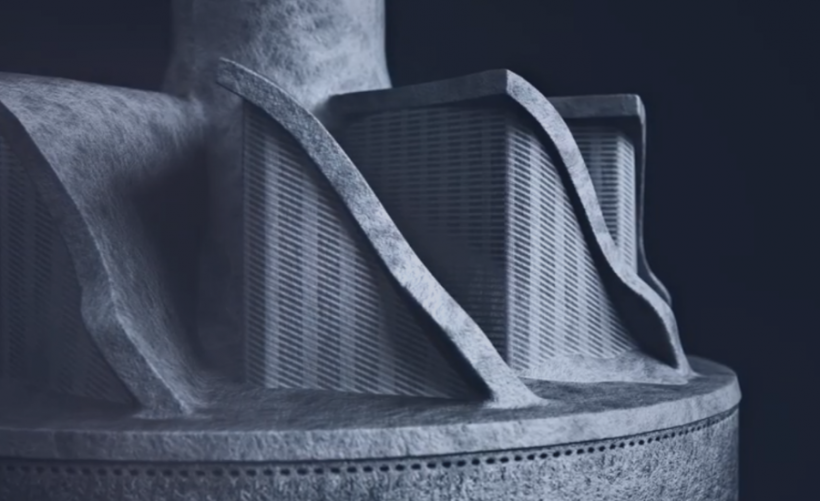
Nabewerking kan een van de belangrijkste knelpunten zijn bij het gebruik van additive manufacturing (AM) als industrieel proces. Elke AM-technologie vereist zijn eigen set van nabewerkingsoplossingen, die zoveel mogelijk moeten worden geautomatiseerd om een levensvatbaar gebruik van de technologie in de productie mogelijk te maken.
Gelukkig is de industrie begonnen met het aanpakken van uitdagingen op het gebied van nabewerking, waarbij steeds meer bedrijven oplossingen introduceren om de post-printworkflow te automatiseren en optimaliseren.
In het artikel van vandaag bekijken we enkele van de beschikbare oplossingen voor 3D-printen van polymeren en metalen, en onderzoeken we waarom nabewerking de sleutel is tot meer productiviteit met AM.
Bekijk de andere artikelen die in deze serie worden behandeld:
Hoe de 3D-printhardwaremarkt evolueert in 2019
De evolutie van de markt voor 3D-printmaterialen:trends en kansen in 2019
3D-printsoftware:echte digitale productie bereiken
Automatisering van nabewerking voor 3D-geprinte polymeeronderdelen
In het domein van 3D-printen van polymeren is er een sterke focus op het automatiseren van de nabewerkingsfase.
Verwijderingsprocessen, zoals het verwijderen van dragers, hars- of poederverwijdering, zijn de meest gebruikte nabewerkingen. Ze worden meestal handmatig uitgevoerd, wat veel tijd en arbeidskrachten kost.
Wat deze fase verder compliceert, is het feit dat veel bedrijven verschillende 3D-printtechnologieën gebruiken, elk met hun eigen nabewerkingsvereisten.
Dus hoe kunnen bedrijven hun nabewerkingsactiviteiten verbeteren, voordat ze worden geconfronteerd met knelpunten bij het toevoegen van meer printers of het introduceren van een andere 3D-printtechnologie?
Bedrijven, zoals Rösler, PostProcess Technologies, AMT en DyeMansion hebben oplossingen ontwikkeld om AM-gebruikers te helpen de nabewerking te stroomlijnen.
Ontwikkelen van een end-to-end naverwerkingsoplossing
Een bedrijf dat de nabewerkingsworkflow wil vereenvoudigen, is het in het VK gevestigde Additive Manufacturing Technologies (AMT).
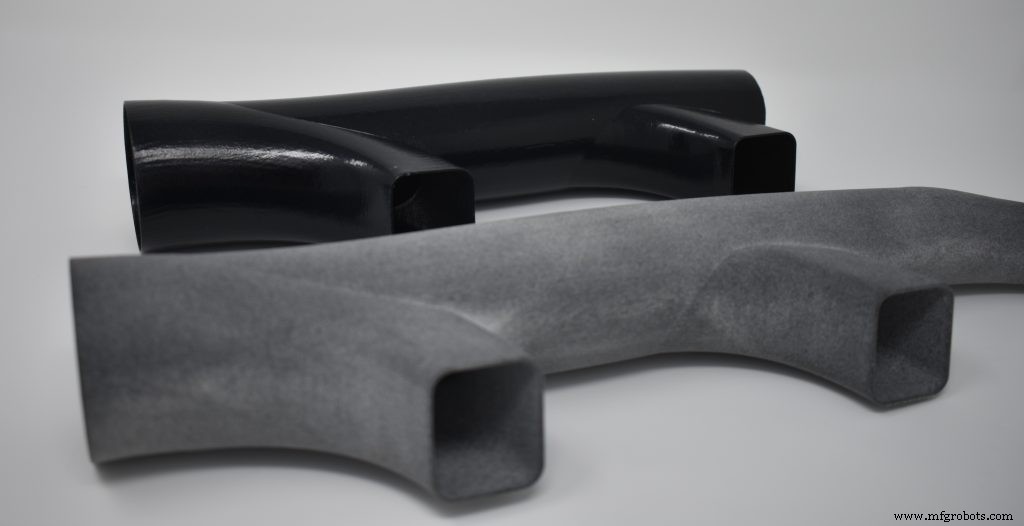
Vorig jaar gelanceerd, maakt AMT's eerste onderdeelafwerkingssysteem, PostPro3D, gebruik van een chemisch dampafvlakkingsproces, waarbij gepatenteerde chemicaliën worden toegepast om het oppervlak van een 3D-geprint polymeeronderdeel glad te maken.
De chemische oplossing sluit het oppervlak af en verwijdert de porositeit van het onderdeel. Het voorkomt ook het binnendringen van water of gas en verbetert zelfs de mechanische eigenschappen.
AMT's oplossing is gericht op polymeeronderdelen die zijn geproduceerd met poederbed- en extrusiegebaseerde technologieën.
De PostPro3D kan geprinte onderdelen afwerken met behulp van hoogtechnologische polymeren zoals ULTEM, nylons, TPU en TPE, enz. Volgens het bedrijf zijn meer dan 95 polymeren gevalideerd voor zijn systemen.
Meer recentelijk heeft het bedrijf ook een kleinere en goedkopere PostPro3D Mini-eenheid op de markt gebracht, gericht op onderzoeksinstituten en kleinere servicebureaus.
In de toekomst is AMT van plan om zijn Digital Manufacturing System te lanceren, dat ontpoederen, gladmaken, kleuren en inspecteren combineert om elk van de handmatige nabewerkingsstappen te automatiseren.
DyeMansion's VaporFuse Surfacing-technologie
Een ander bedrijf dat AM-afwerkingssystemen levert, is het Duitse bedrijf DyeMansion. Vorige maand onthulde het bedrijf zijn nieuwe Powerfuse S-systeem, gebaseerd op VaporFuse Surfacing (VFS)-technologie, een gesloten, geautomatiseerd proces dat in staat is om gladde, hoogglanzende oppervlakteafwerkingen te bereiken voor 3D-geprinte onderdelen.
Delen die zijn behandeld met het VFS-proces zijn ook waterafstotend en gemakkelijk schoon te maken. Volgens DyeMansion is de oppervlaktekwaliteit van een VFS-onderdeel vergelijkbaar met die van spuitgegoten onderdelen.
Qua materialen is de nieuwe VFS-technologie van DyeMansion compatibel, niet alleen met harde polymeren zoals PA11 of PA12 , maar ook met flexibele materialen zoals TPU, wat een uitdaging kan zijn om handmatig af te werken.
Om de lat hoger te leggen op het gebied van automatisering en digitalisering van nabewerking, heeft DyeMansion ook een volledig automatische laadoptie, connectiviteit en batchtracking-functies geïntroduceerd in het nieuwe systeem.
Als het gaat om de plannen voor de langere termijn, zullen het Powerfuse S-afwerkingsplatform - en de VFS-technologie - worden geïntegreerd in de Print-to-Product Workflow van DyeMansion. In deze workflow kan het VFS-proces worden geïmplementeerd als een tweede (of aanvullende) surfacing-optie naast PolyShot Surfacing (PSS) en kan het worden gevolgd door het kleurproces.
Rösler's AM-oplossingen
Naast AM-specifieke nabewerkingsbedrijven, zijn grote bedrijven die doorgaans traditionele industrieën bedienen, begonnen met het ontwikkelen van oplossingen voor AM.
Een van die bedrijven is de Rösler Group, een Duitse specialist in oppervlakteafwerkingsoplossingen.
Rösler levert al meer dan 80 jaar diensten op het gebied van oppervlakteafwerking. Het conglomeraat biedt een uitgebreid portfolio van massaafwerkingssystemen, gritstralen, verbruiksartikelen en nabewerkingsoplossingen in 15 verschillende dochterondernemingen.
Het bedrijf trad vorig jaar toe tot de 3D-printindustrie door een multifunctioneel platform te lanceren voor oppervlakteafwerking 3D-geprinte onderdelen, RapidFinish genaamd.
Dit jaar besloot het bedrijf zijn AM-activiteiten, waaronder ook diensten vallen, te bundelen onder de merknaam AM Solutions.
De 3D-nabewerkingsafdeling van AM Solutions biedt mogelijkheden zoals uitpakken, verwijderen van ondersteunende structuren, verwijderen van restpoeder, oppervlaktereiniging, gladmaken, polijsten en verven van 3D-geprinte onderdelen.
Deze diensten zijn beschikbaar voor 3D-geprinte onderdelen van metaal, polymeer en legeringen, met behulp van AM Solutions' selectie van nabewerkingsapparatuur. Sommige van de machines zijn ontwikkeld door Rösler, terwijl andere van andere leveranciers zijn, zoals PostProcess Technologies en GPA INNOVA.
De verschillende nabewerkingsfasen worden elk uitgevoerd door een geautomatiseerd systeem, dat naar verluidt gebruikers in staat stelt om een hoge mate van herhaalbaarheid en hogere productiviteit te bereiken.
Rösler verkoopt niet alleen machines voor oppervlakteafwerking, maar past zijn oplossingen ook aan specifieke 3D-printers aan. Zo kondigde AM Solutions vorige maand een samenwerkingsovereenkomst met HP aan. Volgens de overeenkomst zal het bedrijf zijn expertise op het gebied van oppervlakteafwerkingsoplossingen gebruiken om deze specifiek aan te passen aan HP's Multi Jet Fusion-technologie.
Nabewerking van metalen 3D-geprinte onderdelen
Als het gaat om de nabewerking van metalen 3D-prints, is de workflow ingewikkelder dan die van polymeer en vereist veel gespecialiseerde apparatuur. 3D-geprinte metalen onderdelen moeten van hun bouwplaat worden weggesneden en vervolgens een warmtebehandeling ondergaan om de interne spanningen die tijdens het printproces ontstaan te verwijderen.
Bovendien kunnen verschillende metalen 3D-printprocessen verschillende nabewerkingen vereisen oplossingen. Voor het nabewerken van onderdelen die zijn geproduceerd met een metal binder jetting 3D-printer, heeft een bedrijf bijvoorbeeld extra apparatuur nodig voor debinding en sinteren.
Tegelijkertijd zijn er minder oplossingen speciaal ontwikkeld voor de nabewerking van metaal AM. In de meeste gevallen passen AM-gebruikers dezelfde set nabewerkingsapparatuur toe die ze gebruiken voor metalen onderdelen, geproduceerd met traditionele technologieën.
Dat gezegd hebbende, is er één veelbelovende nabewerkingsoplossing voor AM die kan worden gebruikt om steunen van metalen onderdelen te verwijderen en kan in een geautomatiseerde omgeving gladde oppervlaktestructuren bereiken.
Hirtisation genoemd, het nieuwe proces is ontwikkeld door het Oostenrijkse bedrijf Hirtenberger Engineered Surfaces.
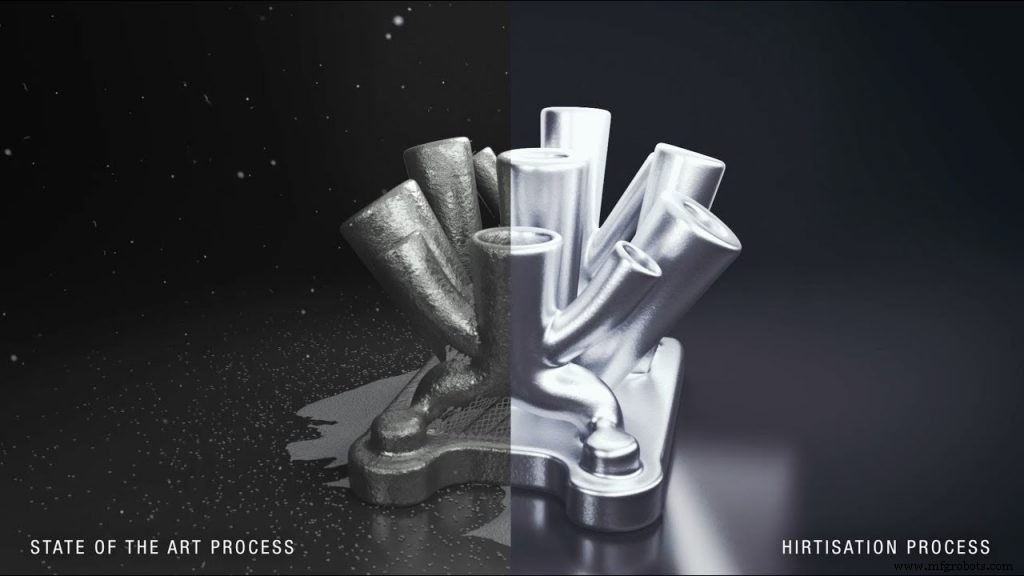
Het proces bestaat uit drie stappen. In de eerste worden ondersteunende structuren en poederkoek van het onderdeel verwijderd en wordt de oppervlakteruwheid aanzienlijk verminderd. In de tweede stap wordt de oppervlakteruwheid van het onderdeel verder verminderd, wat resulteert in een oppervlaktekwaliteit die geschikt is voor de meeste industriële toepassingen. De derde, optionele stap, is een hoog polijstproces dat een decoratieve, ultragladde afwerking creëert.
Volgens het bedrijf is Hirtisation geschikt voor alle metalen en legeringen die gewoonlijk worden gebruikt bij 3D-printen.
Oerlikon AM, de eenheid die AM-diensten levert, is onlangs een samenwerking aangegaan met Hirtenberger om het Hirtisatieproces te evalueren.
In de eerste fase van hun samenwerking ontdekten Oerlikon en Hirtenberger dat het Hirtisatieproces in staat was om onderdelen af te werken met geometrieën die voorheen moeilijk of onmogelijk waren om af te werken met andere oppervlaktebehandelingsmethoden.
De mogelijkheid om uiterst complexe metalen componenten efficiënter na te bewerken, is een enorm voordeel in industrieën die afhankelijk zijn van de ontwerpvrijheid die AM biedt. Systemen zoals Hirtisation helpen om dit voordeel te ontsluiten en verdere industrialisatie van de technologie te vergemakkelijken.
Een ontpoederingsprobleem oplossen
Bij de verwerking van 3D-printen van metaal op poederbasis moeten gebruikers doorgaans het poeder verwijderen dat overblijft na het printproces.
Het is echter geen gemakkelijke taak, want als een onderdeel een complex ontwerp heeft, bestaat het risico dat het poeder vast komt te zitten in het onderdeel. Het vrijgeven van het poeder gebeurt voornamelijk handmatig, wat niet efficiënt is bij de nabewerking van grote partijen onderdelen.
Om het proces te automatiseren, heeft het Duitse bedrijf Solukon, in samenwerking met Siemens, het SFM-AT800S-systeem ontwikkeld voor het automatisch ontpoederen van 3D-geprinte onderdelen gemaakt met poederbedfusietechnologie.
Het ontpoederingssysteem is een roestvrijstalen kamer, die onderdelen van aluminium, titanium en nikkellegeringen toelaat met afmetingen tot 800 x 400 x 550 mm.
Zodra een onderdeel in de machine, begint het ontpoederingsproces. Met behulp van gecontroleerde trillingen, met brede frequenties en gemotoriseerde asrotatie, reinigt het systeem het gesinterde metaaldeel grondig van eventueel achtergebleven metaalpoeder.
Na het geautomatiseerde proces ondersteunt de machine ook handmatige reiniging met 6 bar perslucht of inert gas onder druk.
Een dergelijk proces helpt ook om het resterende poeder veilig terug te winnen, contaminatie te voorkomen en het voor te bereiden voor verdere verwerking.
Sommige fabrikanten van 3D-printers zijn ontwikkelen ook ontpoederingsoplossingen speciaal voor hun machines. Eerder dit jaar kondigde Digital Metal, een expert op het gebied van het stralen van metaalbindmiddelen, een automatiseringsoplossing aan, waarbij een CNC-machine wordt gebruikt om poeder te verwijderen in de nabewerking.
Een ander metaalbindmiddelstraalbedrijf, ExOne, heeft ook biedt een geautomatiseerd ontpoederingsstation aan dat is ontwikkeld voor zijn printers.
Aangezien 3D-metaalprinten in toenemende mate wordt gebruikt bij de productie van zeer complexe en ingewikkelde onderdelen, zoals brandstofsproeiers en warmtewisselaars, zal de behoefte aan geautomatiseerde ontpoederingsoplossingen alleen maar toenemen.
Uiteindelijk zal het overschakelen van handmatig naar geautomatiseerd ontpoederen helpen om de 3D-printworkflow van metaal aanzienlijk te optimaliseren, niet alleen door de handmatige arbeidstijd te verminderen, maar ook door poederafval en schrootdelen als gevolg van poederresten te minimaliseren problemen.
Nabewerking voor 3D-printen:een sleutel tot hogere productiviteit
Het schalen en automatiseren van nabewerkingen blijft een uitdaging. We zijn echter optimistisch dat deze uitdaging binnenkort tot het verleden zal behoren, aangezien verschillende spelers in de sector oplossingen ontwikkelen om deze te overwinnen.
Van ondersteuningsverwijdering tot ontpoedering, oppervlakteafwerking en kleuring, AM-gebruikers hebben tegenwoordig meer opties dan ooit om hun nabewerkingsstappen te optimaliseren en te automatiseren.
Uiteindelijk opent het hebben van de juiste infrastructuur voor nabewerking de deur naar een hoge mate van herhaalbaarheid en productiviteit met AM. Daarom moet het implementeren van nabewerking een prioriteit zijn voor diegenen die 3D-printen gebruiken voor productie of die het gebruik van de technologie in de toekomst willen uitbreiden.
3d printen
- 6 dingen die u niet wist over 3D-printen
- Industriële inkoopstrategieën die fabrikanten moeten weten
- Ondersteunende structuren voor 3D-printen:de belangrijkste dingen die u moet weten
- Industrieel 3D-printen:6 trends om op te letten in 2018
- 7 React-bibliotheken die je moet kennen
- Wat u moet weten bij het identificeren van een Wi-Fi MCU voor IIoT
- Top 4 tips voor machineonderhoud die u moet overwegen voor uw industriële apparatuur
- Koppeling geconfronteerd:alles wat u moet weten
- CNC-bewerking versus 3D-printen:de belangrijkste verschillen die u moet weten
- Technologieoverzicht:wanneer u echt voor metaal 3D-printen moet gaan
- CNC-bewerkingscentrum voor de energie-industrie:3 dingen die u moet weten